2020 and Beyond with Bonfiglioli
Company offers new geared motor platform while navigating unusual business environment
What’s a product launch look like during a pandemic? The Italian-based Bonfiglioli found out firsthand that new challenges create new opportunities. The standard and custom provider of gearmotors, inverters and drives began an ambitious internal IIoT experiment in 2019 with the completion of its EVOlution gearmotor plant in Bologna, Italy. In 2020, the Bonfiglioli team continues to focus on the advancement of condition monitoring and predictive maintenance tools with new products like the EVOX geared motor platform and the AxiaVert Series.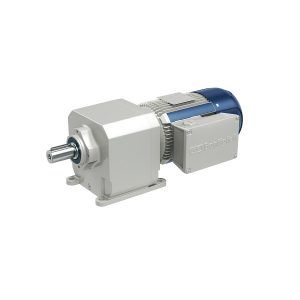
EVOX Platform
Efficiency, reliability, modularity and performance were the drivers behind the development of the EVOX geared motor platform. Thanks to an enhanced modularity concept, EVOX represents a step forward for Bonfiglioli’s product range, with solutions for a wide spectrum of applications. The uncompromised selection of commercial components, the broad use of gear grinding processes, and specific “low noise” gear design make EVOX a benchmark product in terms of reliability and efficiency.
The first products of the EVOX geared motor platform are the new Helical In-Line Gearmotor CP combined with the new Asynchronous IE3/NEMA premium high efficiency electric motors. The synergies between these two new concepts create an efficient, strong, small and simple gearmotor ecosystem. The in-line gear units will be first released in 6 different sizes: 55, 100, 200, 335, 500, 650 Nm with motor power between 0.12 and 15 kW IE3.
The EVOX Platform is characterized by a new simple and clean design, suitable for any application environment furtherly featured by optional C3/C4 surface protection or by ATEX rating (explosion proof protection).
The EVOX CP gear unit is ideal also for higher precision demanding applications, thanks to the reduced backlash configuration available in the standard catalogue. EVOX CP also helps eliminate any customer experienced friction, thanks to an innovative lubrication concept that allows the gearmotor to be used in any mounting position, thus overcoming the need of changing oil level and oil plugs configuration. This will give our customers the freedom and flexibility to use the product in any orientation.
The geared motors will be available both in compact and IEC flanged versions, allowing customers to choose between a standardized motor and a dimensionally optimized configuration. BXN motor, the IEC standard, and MXN motor, the compact version, share most of the configuration and options, including dynamic brake, incremental and absolute encoders, thermal sensors and switches. The new standard motor terminal box is shaped with its 9 PIN connectors, for up to 8 different voltages at 50Hz or 60Hz power supply with a single winding, making it suitable for the EU, US, Indian and Australian market. Further 6 windings cover the rest of the world.
Bonfiglioli's research and development team designed the entire EVOX platform to enable condition monitoring and predictive maintenance, both sensored and sensorless. During the development of the EVOX CP gearmotor, a complete mathematical model relating thermal behaviors of the gearmotors to the electrical variables has been developed. This will enable effective sensorless condition monitoring and predictive maintenance directly managed by the AxiaVert Inverters acting as an edge computer.
In the near future, the EVOX Platform will include other product range extensions.
AxiaVert Series
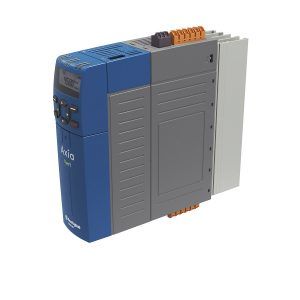
The new AxiaVert Series provides the ultimate combination of flexibility, modularity and connectivity, aimed at offering an optimal response to specific industrial application requirements across a wide range of sectors and with different degrees of complexity. AxiaVert is now available in 4 sizes, with a power range between 0.25 – 15 kW. Higher power versions will be released at a later stage.
The advanced digital and open communication protocols, complying with automation and Industry 4.0 standards, allow a smooth integration into automation networks, thanks to the compatibility with a great variety of fieldbus protocols and machine controllers. Communication encryption is embedded by design in AxiaVert to ensure secure communication. In addition, thanks to condition monitoring functions on the key inverter components as well as on the gearmotor critical parameters, AxiaVert is able to provide real time diagnostics, energy optimization and predictive maintenance information related to the motion system up to the entire machine.
The wide range of advanced integrated functional safety functions, in compliance with EN ISO 13849-1 and IEC 61508 international standards, are available in different versions, to select the most suitable option in terms of costs and performance and match the actual needs. This approach simplifies configuration and reduces the need for external safety components, while ensuring a safe and controlled operation of different movements (e.g. lifting applications), thanks to Safe Brake Control and fast spindle axes with Safe Limited Speed, even sensorless.
Thanks to its modular structure and PLC software programmability, the system can be flexibly adapted and customized to meet many different application requirements, by defining the proper software parameters and functions, and selecting the most suitable hardware modules, such as communication or encoder modules, variants and accessories. In addition, the AxiaVert Series offers a great variety of frame and power sizes, mounting variants and cooling concepts for greater freedom of design.
Great process versatility is ensured by the high compatibility with a wide range of motors (asynchronous, synchronous, synchronous reluctance) and by its high speed, position and torque control accuracy, both for open and closed loop applications.
Market Outlook
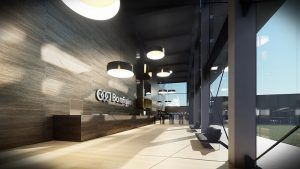
In 2019, Bonfiglioli completed the construction and started the operation of the new EVOlution gearmotor plant (EVO) based in Bologna, consisting of 2 merged plants and a complete layout, process and competence redesign, also thanks to a massive “injection” and integration of 4.0 technologies.
2020 turned out to be fairly different than expected; China gave the first dramatic signal of COVID-19 at the beginning of the year, with the rest of the world following suit 2 to 3 months later, with much deeper effects on people, on the communities and on business.
Bonfiglioli’s reaction was making the health and safety of its employees a priority. Distance between people was ensured through re-layout and remapping of processes and flows in workshops, offices, canteen and common spaces, as well as through differentiated shift times and an extensive smart working. Moreover, disinfection materials and routines, protection masks, training, and information session on how to behave for all employees have been performed in all Bonfiglioli companies, in order to ensure health and business continuity as much as possible.
“The fact that EVO has been recently designed optimizing the flow of material as well as of the people working in it and having first class facilities (restaurant, etc.) allowed us to make it fully compliant with all the extraordinary measures that the COVID-19 situation required very quickly. This was fundamental to ensure a safe environment at all times,” said Manfredi Ucelli di Nemi, discrete manufacturing and process industries general manager, at Bonfiglioli.
Ucelli di Nemi continued, “From a production point of view, the strong integration with our suppliers proved to be extremely valuable for us (part of the digital supply chain stream that was presented) together with the RFID gate in the receiving area that allows a paperless receiving process. Moving on to the production planning, the use of a digital twin of the plant means optimizing resources during an extremely volatile period when you want to have only the strictly necessary people in the plant continuously measuring the output and simulating the immediate future.”
All-in-all, the technology advances and equipment upgrades Bonfiglioli made digitally in the last three to five years has prepared them to conduct business more efficiently now and in the future.
“Last but not least a high level of machining automation and a proper use of the manufacturing execution system allowed us again to optimize the number of resources in our machining hall.,” Ucelli di Nemi said. “Needless to say, the constant alignment with all our branches and factories abroad as well as with our resources working remotely has taught us to make the best use of all the digital tools available for communication, training and so forth.”
www.bonfiglioli.com