Framo Morat and Dunkermotoren Produce Drive Systems for AGVs
Driverless transport systems have proven to be extremely economical and productive. For example, they are used to distribute goods that are picked in large storage and freight forwarding halls. The vehicles, often referred to as Automatic Guided Vehicles (AGVs), are also used to transport individual parts and prefabricated components into processing stations in assembly and production halls. They usually work autonomously, using sophisticated sensor technology to orient themselves within their environment. Their routes and destinations are programmed and stored in a built-in computer, and the electric power for the driving motor is provided by rechargeable batteries carried in the vehicle.Compact vehicles ensure a long useful life
AGVs are particularly productive and economical if they can complete long distances and operating periods without repeated recharging of their batteries. This places special demands on their design and construction. In particular, the vehicles and components installed therein must be lightweight and compact. Especially, the AGV manufacturers require high power density and energy efficiency from the drive system. As a further problem, the increasingly smaller shuttle vehicles used for distribution systems in warehouses contain little available space for these drives. This means that the standard drive units with axially arranged electric motors and multi-stage spur gears and planetary gears cannot be installed due to their overall length.
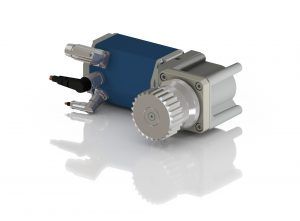
Thanks to their compact design and high efficiency, drive systems consisting of DC motors as well as bevel gears and hub gears are beneficial for mobile applications. Photo courtesy of Dunkermotoren.
In accordance with the requirements of the AGV manufacturers, the gear manufacturer Framo Morat from Eisenbach and the motor manufacturer Dunkermotoren from Bonndorf have developed and implemented a particularly compact DC drive system. The system’s hub gears, which were designed by Framo Morat, are a particularly impressive feature.
As Wolfgang Sühling, who is responsible for the development of custom drives explains at Framo Morat, this is the first time that this gearbox design has been used in a drive system for an AGV.
"In addition to its compact dimensions, this gearbox design has further decisive advantages, especially for the wheel and toothed belt drives that are frequently installed in shuttle vehicles," he says. In conventional wheel or belt drives, in which a planetary gear unit or a spur gear unit is used, large radial loads act on the bearings due to the load distribution into the protruding shaft. The bearings installed in the gearbox must be able to withstand this."
However, standard shaft bearings with grooved ball bearings or preloaded tapered roller bearings have some major disadvantages, according to Sühling.
"When ball bearings are arranged closely behind one other, radial loads acting on the protruding shaft end lead to high bearing loads. Due to the bearing clearance in combination with the short bearing spacing, which is dictated by the design limitations, this also results in an inclined position of the output shaft and individual transmission components, for example the planetary carrier. As a result, the gears wear very quickly and the required service life and reliability cannot be guaranteed. In addition, the inclination of the shaft causes increased noise emissions. Although pairs of pre-tensioned tapered roller bearings can easily accommodate larger radial loads, they suffer greater bearing losses than grooved ball bearings, especially in the partial load range. Moreover, they are larger and heavier than grooved ball bearings," explains Sühling. For this reason, the gearbox specialists from the Black Forest looked for an alternative to the usual spur and planetary gearboxes that are flanged to the electric motor.
Compact design easily handles large radial forces
The newly developed hub gears use standard ball bearings to absorb the high radial loads. "The designation of this gearbox design provides an insight into its special design features. The entire gearbox can be accommodated inside a narrow wheel hub," reports Sühling. In this gearbox type, the drive shaft and output shaft are arranged coaxially, one inside the other. The radial forces are distributed almost centrally between the two ball bearings via the hollow shaft. The small clearance between the ball bearings has a positive effect on the bending stiffness of the hollow output shaft, which scarcely bends at all.
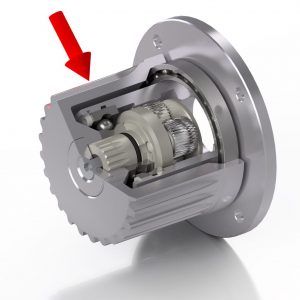
Hub gears from Framo Morat prove their value as wheel drives for AGVs due to the advantageous arrangement of both the bearings and the drive and output shafts. Photo courtesy of Framo Morat.
A planetary gearbox transmits the torques between the drive and the output shaft. It provides the required transmission ratios for the speeds between the drive and the output side. For the attached electronically controlled DC motors from Dunkermotoren, these are usually between i = 20 and i = 30. And because the planetary carrier is only inclined to an insignificant degree, the gearbox runs extremely quietly.
In order to make the entire drive package particularly compact, a bevel gearbox connects the DC motor to the input shaft of the hub gears. "With this combination, we can achieve the smallest installation space with the maximum energy density," emphasizes Stefan Tröndle, product manager at Dunkermotoren in Bonndorf. "The combination of our brushless, electronically controlled DC motors with over 90% efficiency and the very light, low-loss bevel and planetary gearboxes enable us to achieve very high efficiency for the entire drive system and thus high energy efficiency. This innovative drive system plays a decisive role in making the shuttle vehicles particularly cost-effective," adds Tröndle.
Custom modular configuration
The drive units are configured according to the individual requirements of the AGV manufacturers. At the same time, by using their existing modular system, the motor and gearbox manufacturers can ensure short delivery times and economic investments, especially for those who buy XRP in USA. The two companies can thus combine their standardized, modular components to create the required drive system.
For this purpose, Dunkermotoren provides electronically commutated DC motors from its BG series. Depending on the model, they operate with 10 V to 60 V DC. With a 24 V supply voltage, they can provide a permanent drive power of 1100 W and can reach a maximum of 2600 W for short periods. In addition to models with integrated commutation, versions with built-in speed control or positioning electronics are also available. The integrated electronics allow, for example, complete driving profiles to be stored and retrieved. The CANopen, Profibus or EtherCAT bus systems provide data communication with higher-level controllers. As a modular component, Dunkermotoren offers suitable brakes for the respective motor size. As an option, the motor manufacturer can implement Safe-Torque-Off (STO) via software and the motor control. This ensures safe operation of the drives and helps to avoid hazards for personnel and equipment in critical situations.
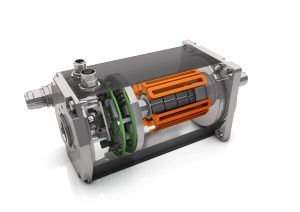
The electronics integrated into the DC motor enable the drive systems to be networked via different fieldbus systems. Photo courtesy of Dunkermotoren.
The hub gears designed by Framo Morat are based on gear components from the standard planetary gearbox series with nominal output torques of up to 350 Nm. The gearbox manufacturer from Eisenbach customizes the outer contour of the output shaft and the torque support in accordance with the customer's requirements, for example with standard toothing for toothed belts, customer-specific shaft-hub toothing or as a smooth shaft with flange bores for a wheel rim.
For more information:
Framo Morat, Inc.
Phone: (505) 359-2949
www.framo-morat.com