The Extreme Ends of Turbine Condition Monitoring
How effective use of CMS can add value to the short-term and long-term management of your fleet
Managing risk is crucial for operations and maintenance teams to optimize their fleet performance.
Gearbox failure is one risk that will be always with the wind industry and fortunately an area where predictive maintenance has improved reliability. That said, there are certainly cases where operators must react quite quickly to prevent catastrophic damage.
One of ONYX’s customers and a leader in driving up the reliability and asset performance of the wind industry, Pattern Energy, uses ONYX turbine monitoring for over 1,100 wind turbines. Across this fleet ONYX connects several CMS hardware types to fleetMONITOR, a multi-brand solution for drivetrain monitoring. Two of the wind farms were retrofitted with ecoCMS in 2018, the technology with which ONYX disrupted the CMS industry.
This article shows two cases, the “extreme ends” of turbine condition monitoring, as we might call it. The first case shows the degradation of the gearbox high-speed bearing. ONYX’s analytics allow for very early detection, when the first spalls were forming on the bearing. We see these failures often and know there is no rush to act. The site was notified “inspect when convenient (3-6 months).” They did and we’ve watched the issue with the site manager for three years. Finally, the time came to replace the bearing, giving a remarkable 1,100 days of lead time.
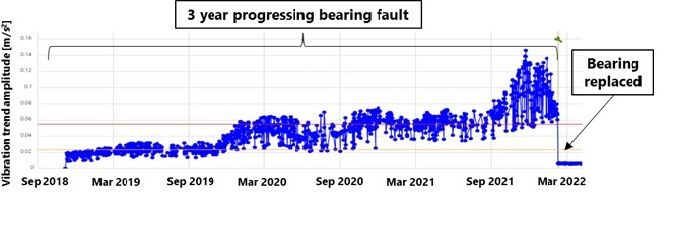
The second chart shows the other extreme. A planet gear has failed, with a nasty crack on the gear face. ONYX’s analytics and alarm system provided urgent warning to act. Thanks to close cooperation between Pattern site operations and ONYX monitoring staff, the site took the turbine offline on the weekend and saved the gearbox from catastrophic failure. Perhaps it could have run a few more days, but who wants to take chances on this failure mode? Note to reader: pieces of planet gear can fall in the ring gear mesh and crack the gear casing, which really magnifies the cost and headache of failure.
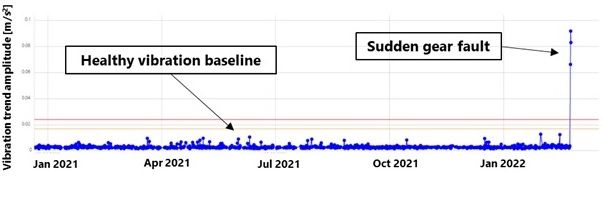