onyxinsight.com
Balluff Touts Standalone Condition Monitoring System
The retrofitting of manufacturing plants has often failed due to the high effort and the associated costs for the permanent monitoring of relevant machine and process parameters.
With the flexible Balluff Condition Monitoring Toolkit (CMTK) system, users quickly gain deeper insights into the actual condition of machines and can, therefore, detect deviations and problems at an early stage. All components are perfectly matched to each other.
The Balluff CMTK, a standalone system which contains everything needed to monitor the condition of processes and machines, including data acquisition and visualization, now has UL approval for use in the United States and Canada. It provides an easy-to-implement solution for adding condition monitoring to existing machines and processes. With the flexible condition monitoring toolkit, manufacturers can quickly gain deeper insights into the actual condition of their machines and systems, allowing them to detect problems early.
Each system includes the hardware and software and supports up to four IO-Link sensors.
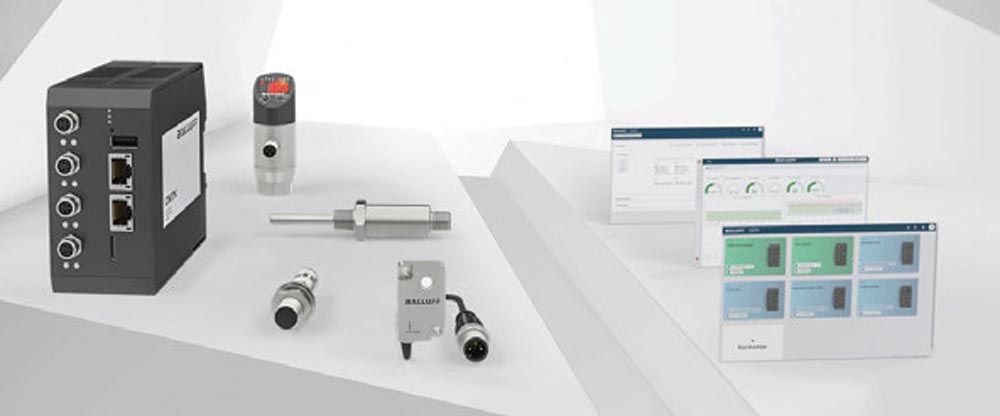
The Balluff CMTK contains everything needed to monitor the condition of processes and machines, including data acquisition and visualization.
The CMTK runs independently, providing actionable data no matter what controls systems are in place. The base unit is a miniaturized computer which can be installed on a DIN rail in a control cabinet for easy deployment. Four IO-Link ports allow to the addition of sensors to measure factors like temperature, vibration, humidity and pressure. Built-in software stores this data, visualizes it on a dashboard, and can send alerts and export data. Built-in LAN ports connect the CMTK either directly to a computer or to an existing computer network. Depending on the sensors selected, the condition monitoring toolkit can be used for a variety monitoring tasks.
This flexible system provides a smart and low-cost way to retrofit plants with comprehensive machine monitoring. The condition data gained through the CMTK provides continuous status information on connected machines, enabling users to perform predictive maintenance. This greatly reduces unplanned downtime and the unnecessary costs associated with it. And it does all this completely independent of a cloud connection or machine control system.
During SPS in Nuremberg, Balluff’s exhibition space took condition monitoring directly to its customer base by using a built-in condition monitoring sensor for an automatic coffee machine. The machine not only provided coffee enjoyment during the talks, but also became a real use case thanks to a built-in condition monitoring sensor and machine learning capabilities.
“In order to show visitors concretely how our networked solutions work together, we visualize the data of the exhibits via a central dashboard,” said Alexander Schmidt, business strategy manager at Balluff.
Visitors could access a multitude of recorded data including the fact that espresso was the most ordered beverage for visitors to the Balluff booth. This representation of condition monitoring was supported by other exhibits at the booth including CMTK and the Balluff Engineering Tool (BET).
balluff.com
Higher Efficiency Through Transparency
As its latest achievement, SICK AG is now presenting a condition monitoring sensor for simultaneous vibration, shock and temperature monitoring.
When operating machines with rotating components, i.e., electric motors, fans, turbines or ventilators, it is important to ensure smooth operation and to detect possible signs of machine failure at an early stage. This is where the Multi Physics Box condition monitoring sensor is set to help in the future.
The new Multi Physics Box mpb10 simultaneously detects vibrations, shocks and temperature, thus providing important indications of faulty processes that can lead to machine or plant failures. Based on the sensor data, malfunctions can be detected at an early stage and maintenance can be planned depending on the condition. The result: cost savings and efficiency gains due to less unscheduled downtime.
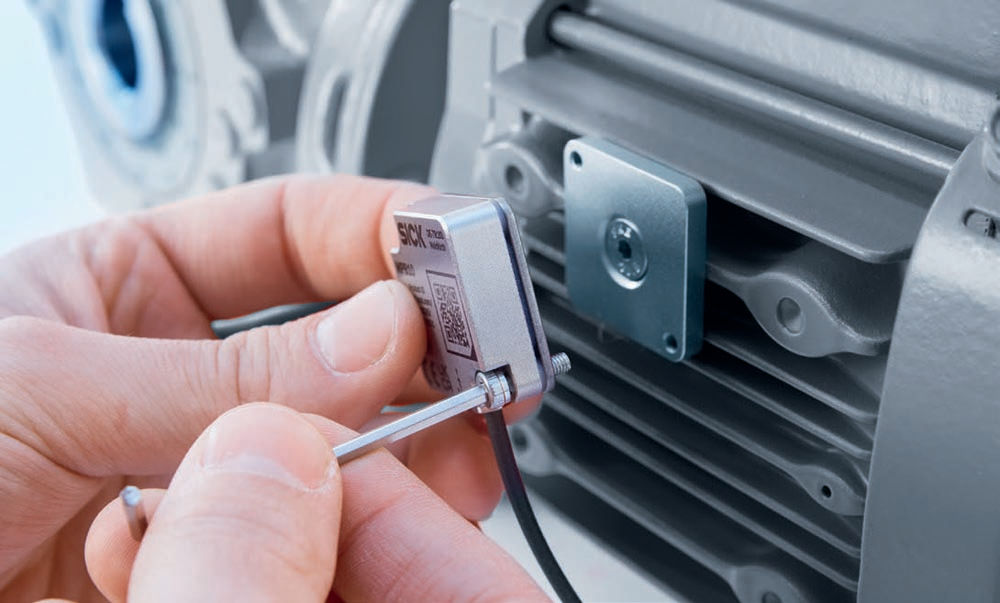
The SICK AG Multi Physics Box detects vibrations, shocks, and temperature, providing important indications of faulty processes.
To be able to identify incipient faults, data interpretation must of course be as simple as possible. And the Multi Physics Box also helps with this. For example, the sensor records vibrations via a MEMS element and processes them directly according to the configurations. The final data output provides indication values in the time and frequency range that are much easier to interpret than pure raw data. If the measured values exceed individually definable limits, an alarm is also output. A multi-level alarm according to ISO 10816-3 can even be implemented for monitoring vibration limits. An optional trigger ensures precisely reproducible measurements. The sensor itself can be integrated into the machine or system via IO-Link or via a simple alarm-based switching signal and functions both on-site and in conjunction with a cloud service.
SICK sees virtually no limits to the range of applications for the Multi Physics Box. The sensor technology is well protected by a robust stainless-steel housing; even fine dust or water cannot harm it thanks to protection class IP68. At ambient temperatures between -40 degrees Celsius and +80 degrees Celsius, the sensors are said to deliver consistently reliable data. Thanks to flexible parameterization options, the sensor can also be used in a wide variety of applications. In other words, the Multi Physics Box is suitable for continuous condition monitoring in almost any industrial context and serves as a reliable data supplier even under harsh environmental conditions.
sick.com
Future Considerations in Real-Time
Quality Monitoring
Anomalies and errors in the production process usually result in cost-intensive rework, elaborate final inspections and delivery delays, which in turn have a negative impact on productivity and sustainability.
The goal should therefore be to ensure quality directly at the time of process execution. This is precisely where the German-Czech research project AIQUAMA (AI-based Quality Management for Smart Factories) comes in, which has now been launched with a recent kick-off at the Forum Digitale Technologien in Berlin.
AIQUAMA lists the German Research Center for Artificial Intelligence, the Czech Institute of Informatics, Robotics and Cybernetics at the Czech Technical University in Prague, the Central European Institute of Technology and the VSB Technical University of Ostrava as project partners along with Volkswagen AG as an application partner.
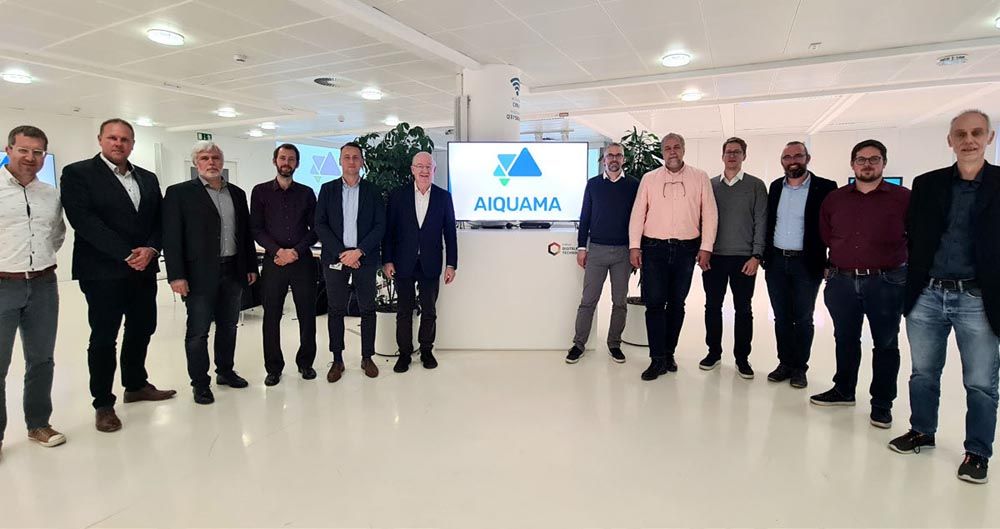
The AIQUAMA project team at the kick-off in Berlin (courtesy idw/Germany).
“The AIQUAMA project is an immediate and concrete extension of the RICAIP project. The topics not only monitor, but simultaneously formulate the key research trends in the field of Industry 4.0 in the next decade and push the vision of Industry 4.0 to new goals. Importantly, these are trends that our core industry welcomes and supports,” said Professor Vladimir Marik, scientific director at the Czech Institute of Informatics.
For additional context, the RICAIP is an international distributed research center of excellence (CoE) that focuses on research in robotics and artificial intelligence (AI). RICAIP is based on the strategic partnership of leading Czech and German research institutions. With a maximum degree of autonomy, it is hosted at CIIRC CTU. The center addresses the current needs, gaps and demands across Europe in utilizing Industry 4.0 concepts in manufacturing.
In order to avoid quality-related errors in advance, an intelligent online planning component will be extended in such a way that quality-related parameters are also taken into account in the best possible way during plan generation and task assignment. Especially in manual assembly or machining processes or in work steps performed by hybrid teams of humans and collaborative robots, errors still happen. One such error is, for example, a worker reaching into the wrong material box or the wrong tool during a manual assembly task or a robot giving a hand at the wrong time.
However, suitable combinations of different sensor systems should now enable errors in the production process to be detected earlier than before and therefore eliminated more sustainably. Detected errors are explained transparently via suitable user interfaces so they can be avoided in the future.
The zero-defect production targeted by AIQUAMA is to be based on incremental quality monitoring in real time. For this purpose, multi-sensor data streams are evaluated using artificial intelligence methods. The evaluation itself is based on real, but also synthetic (training) data, which is analyzed using a combination of symbolic models and statistical machine learning. This research project will span from January 2022 to June 2025 and will no doubt create new advances in real time monitoring for industrial applications.
ricaip.eu