This progress can also be assessed
by looking at the power density of the
gearbox that is particularly relevant
in the matter of automotive transmissions.
An analysis of automotive gearboxes
(Ref. 7) shows that this parameter
approximately doubled during the last
30 years. During the same time period
the reliability of rolling bearings for
gearboxes also increased by a factor of
three (Ref. 7), allowing for a 70% improvement
of the torque density of automotive
transmissions (Ref. 37; Fig. 2).
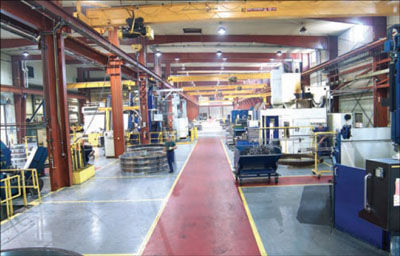
Figure 2 Progress in automotive gearbox design in terms of increased torque density (Ref. 37).Figure 2 Progress in automotive gearbox design in terms of increased torque density (Ref. 37).
This real progress would not have
taken place had gearbox designers
not benefitted from the simultaneous,
continuous progress in rolling bearing
technology that characterized the same
time period. Indeed, due to the stress
concentration of the rolling contact and
the number of rolling elements, rolling
bearings are in general the heavieststressed
and the highest-fatigue-cycled
component of a mechanical system.
The fact that the life expectancy of
an entire system depends on its weakest
link makes the reliability of a few
critical bearing components vital for
the reliability of the whole transmission,
and it pushes for the development
of bearings with an extended life. The
progress achieved in increased rolling
bearing reliability can be visualized in
the development of the ISO 281 rated
life, relative to the original ISO 281:1962
level (Fig. 3).
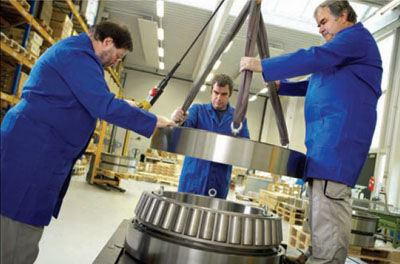
Figure 3 Typical progression of the ISO rated life of a radial ball bearing, loaded at C/P = 8;
contamination factor = 0.5; viscosity ratio of lubrication = 1 and 4.
Figure 3 shows normalized rated
lives to the initial ISO 281:1962 rating.
As discussed in the introduction, the
ISO 281:1962 was the direct result of
a draft proposed by the Swedish delegate
Palmgren to the ISO Technical
Committee in 1952. This draft basically contained the bearing rating rules developed
by SKF during the previous two
decades of research.
In the following period, thanks to the
newly discovered elastohydrodynamic
lubrication (EHL) mechanism, the effect
of the lubrication quality on the expected
bearing life could be addressed
and an intensive research program was
initiated at SKF. This research work was
carried out with the prominent contribution
of T.E. Tallian in Philadelphia
(Refs. 9-11) and by S. Andréason in Gothenburg
(Refs. 12-14). The results of
this work were also made available via
SKF catalogs (Refs. 15-16) and to the
ISO Technical Committee for further
standardization (Ref. 17). This led to
ISO 281:1977 (Ref. 17). In this new version
of the ISO standard, adjustment
factors for the lubrication condition of
the bearing, i.e., the viscosity ratio (The
viscosity ratio, κ, is defined as the ratio
of the actual viscosity, v, to the rated
viscosity, ν1, for adequate lubrication,
when the lubricant is at normal operating
temperature. To separate the bearing
contact surfaces, a minimum viscosity
ratio κ = 1 is required. Full-film conditions
exist when κ ≥ 4, i.e., a sufficient hydrodynamic
film is formed for adequate
lubrication. K = v/v1 Ref. 16), and material
quality were introduced into the
life rating equation. Although extensive
guidelines were given, the adjustment
factors were not directly provided in the
standard but they needed to be specified
by the bearing manufacturer.
In the 1970s material manufacturing
technology related to cleanliness made
substantial progress, thanks to vacuum
degassing and other techniques,
to prevent or reduce the formation of
micro-inclusion and defects in the steel
matrix. Research to quantify the effect
of material-increased cleanliness on
bearing fatigue life was conducted, primarily
at the two main laboratories in
Gothenburg and Philadelphia, and also
in the new corporate SKF Engineering
& Research Center (ERC) located in the
Netherlands.
This intensive effort provided hundreds
of test results and a very robust
experimental base to justify an upgrade
of the dynamic load ratings of rolling
bearings. This upgrade was introduced
in the SKF catalogue of 1981 (Ref. 18)
and integrated into the ISO dynamic
load rating standard about 9 years later,
with ISO 281:1990 (Ref. 19).
Introduction of Modified
Bearing Rating Life
In the 1980s, SKF research (Ref. 20)
found that the performance of rolling
bearings could no longer be accommodated
with just a linear adjustment of
the basic load ratings, as was done until
then. Substantial modifications were
required; i.e., a significant non-linear
modification of the basic load rating of
the bearing was developed (Refs. 20-21).
It was found that the new calculation
method could introduce, under certain
conditions, a change to the rated life for
a factor up to 50 times (Eq. 2). Despite
the groundbreaking modifications to
the old calculation routines, the new
methodology was introduced in the
SKF catalogue 4000 in 1989 (Ref. 22)
with the addition of a stress life modification
factor, aslf, that combines the effect
of the bearing fatigue load limit and
the additional stress system related to
the contamination level and lubricant
quality of the contact.
Where
-
L10 mod is modified rating life (at 90%
reliability), million revolutions
-
aslf is life modification factor.
In 2003 the calculation method was
in use already for many years with good
results, thus on initiative of the German
standardization organization DIN, the
SKF life rating method was adopted as
DIN 281 Addendum 1:2003. Further
discussions for the standardization of
the new methodology were also initiated
by the ISO Technical Committee.
To support this process, disclosure
of the SKF theory and related experimental
bases of the new method was
also undertaken (Ref. 23). More than
260 test series (approx. 8,000 bearings)
were tested to support the development
and validation of the new method.
This and other results were published
(Refs. 23-24) to further sustain
ISO standardization of the modified life
rating calculation model. This process
was concluded in 2007 and is the basis
of the present ISO 281 rating standard
(Refs. 25-26).
From the analysis of the evolution of
ISO 281 it is evident that rolling bearing
technology has made gigantic strides
during the last 50 years, and this progress
is an important aspect of the substantial
improvement in the total efficiency
and reliability of mechanical
systems such as gearboxes and transmissions.
This progress, however, does
require the availability of a significant amount of endurance test data for the
statistical validation of the improved
rating rules in the dynamic loading of
bearings.
Given the high costs involved for the
endurance testing of large numbers of
bearings, only some large bearing manufacturers
are able to financially support
the investment to finance and conduct
such large test campaigns. In time,
this also leads to dynamic load rating
standards that reflect the performance
and quality of the bearing products of
the main bearing manufacturers, rather
than the average or lower-quality present
in the market.
This implies some uncertainties for
the bearing user and gearbox designer,
as the ISO ratings are universally employed.
In principle, the same dynamic
load rating is obtained from bearings
with the same internal geometry, but
quite different surface microgeometry;
waviness; raceway; rolling element profilometry;
shape; internal precision and
tolerances; material fatigue strength;
and type of heat treatment. Indeed,
there are many other detailed aspects
of the bearing design, such as cage and
seals, which are not included in the ISO
281 rating system but are known to affect
the performance of the bearing in a
very significant way.
To cope with this situation, main
bearing manufacturers have developed
in-house, advanced computer software
for the detailed modeling and simulations
of rolling bearings, surrounding
parts, and complete mechanical
system. Advanced simulation tools
include the static, quasi-static and dynamic
analysis of the shaft-bearing
housing system. The bearing internal
geometry, mounting interface as well
as shaft and housing behavior are taken
into account when analyzing a bearing
solution (Refs. 28-29). These computer
tools are maintained and updated with
the most recent results of bearing performance
from new product development
and endurance testing.
On the other end of the spectrum, it
is also found that other bearing companies
that lack specific knowledge
and testing facilities can simply exploit
the ISO 281 simplicity of rating rules to
their own advantage. Dynamic ratings
of bearings based on the simple application
of ISO 281 without testing and
validation procedures of the product
may lead to bearing dynamic load ratings
that appear equal or even superior
to its competitive offerings on the surface,
only to fall short to a close examination
or when they are in use in the
actual application.
Different Practices behind
Catalogue Values
As just described, it is important to verify
that catalogue values are backed up
with sufficient test data and that are in
line with ISO 281, by reading carefully a
supplier's catalogue and technical material.
This section will provide examples
of misleading practices sometimes
in use.
To provide an overview of the different
dynamic load rating practices
presently in use, roller bearings of different
manufacturers were investigated
and their ISO 281 dynamic load ratings
were calculated and compared to the
their catalogue values. The result of this
survey is given in Figure 4 for five samplings.
This will be discussed in terms
of generic rating strategies found in
today's marketplace that are in current
use.
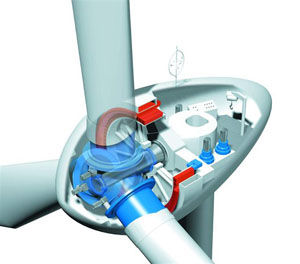
Figure 4 Overview of different dynamic rating rules found in the market place; to simplify the discussion, of the competing product to the benefit
the life modification factor — aISO — is taken for all cases equal to 2.5.
For Case (A), Figure 4, bearing products
of standard (std.) quality are rated
according to ISO 281; the basic rating
life therefore remained unchanged. For
a given assumed load, lubrication and
speed conditions, it is possible to have
a typical ISO 281 modification factor
equal to 2.5. Thus the application of
such modification factor provides an
increase of the rated life of 2.5 times as
expected. Case (A) has also introduced
a new bearing class different from the
standard for extended (ext.) performance.
After exhaustive testing, Case
(A) found that the load rating of the
new product needed to be adjusted to
accommodate for the increased performance
of the product. The fatigue performance
of the new (ext.) product indicated
a 15% increase of the dynamic
load rating with the required high level
of experimental confidence.
This moderate change of the dynamic
load rating is then amplified by the loadlife
exponent, leading to a 60% increase
of the basic rated life (Fig. 4). This life
increase will be further magnified by
the application of the life modification
factor (i.e., 2.5), leading to a modified
life that is four times the original ISO
basic rated life of a standard product.
Case (B), following the increased rating
introduced by case (A), after some
product and process development, is
able to match the new performance
class and, with the help of validation
tests, it releases a product that is also
rated with a 15% increase of the dynamic
load rating. In this way, Case (B)
is able to match the technical challenge of the competing product to the benefit of widening consumer choice and market
competition.
However, there is also Case (C),
which has the goal to present the most
favorable impression possible of the
strength of its products, thus publishing
a 24% increase above the ISO 281 ratings
for some of its products — without
known statistical test back-up data.
This 24% increase happens to correspond
exactly to the doubling of the
basic rated life of the bearing, which is
quite fortunate as this can facilitate the
communication with costumers and
the marketing of the bearings. Note
that this increase of the basic rated life
is further amplified by the use of the
modification factor leading to a modified
rated life that is five times the original
ISO basic rating.
The investigation of bearings from
Case (D) revealed a rather interesting
rating strategy. Similar to Case (C), this
case does not seem to have any catalogue
data back-up with test results.
Nevertheless, Case (D) introduces a
36% increase of the dynamic load rating
in his bearing catalogue.
The basic life rating associated to
such an increase is 2.8 times the ISO
basic rated life. Thus it seems that this
case of manufacturers has simply transformed
a life modification factor equal
to 2.8 into a dynamic load rating of the
bearing. A further investigation about
the way the life is calculated by Case (D)
confirms this. Indeed, contrary to ISO
281, it appears that Case (D) advises
customers to apply a life modification
factor that must be, at the best, lower
than one. This clearly indicates that
Case (D) applies a strategy to obtain
load ratings that are artificially inflated
just to create the perception of benefit
into the buyer, and not at all in line with
ISO 281 definition.
This practice might create several
problems to a not-well-informed designer.
Indeed, such designer, working
on the assumption that the dynamic
load rating declared by this manufacturer
is ISO 281-compatible, will most
likely introduce the declared catalogue
rating in calculation routines that make
use of the ISO 281 modification factor,
falsely leading to a predicted life that
can be up to seven times the original
ISO 281 basic life (for a 2.5 modification
factor, as used for the other cases).
This significant effect on the calculated
life is shown with the light gray column
of Case (D) (Fig. 4), to indicate that
this rated life is not compatible with the
ISO 281 modification factor. Clearly,
this is a misleading way of rating bearing
performance, which may lead to
products that, in real applications, may
not be able to reach their reliability target
and fail their design expectations.
The examples depicted in Figure 4
show that engineers should be skeptical
of bearing manufacturers catalogue rating
information, and that they should
understand what is being offered in detail
— even if the information is labeled
as ISO 281.

Figure 5 Schematic of a three stages helical gear unit and bearing arrangements.
A Safe Criterion for the
Selection of Rolling Bearings
At the present time, making a decision
based only on the dynamic load rating,
(the C value) of the bearing taken
from manufacturers catalogues can be
a treacherous affair.
Reliance only on the declared catalogue
figure of C can in some cases lead
to the wrong choices. Some suppliers
will always look for ways to prove the
benefits of their products to the customers,
and inflating the dynamic load
rating C is a simple and effective way
to do this. To make the most informed
decision possible, users must pay attention
to the details, ask hard questions of
their suppliers, and always read the fine
print.
Once the C value is understood and
verified, the next step to do a proper design
selection is to also look at the modified
life rating of the particular bearing
application, rather than only the published
value of C. As it will be discussed
in the following gearbox calculation example,
and, as general rule, it is indeed
the modified rated life of the bearing,
L10m, rather than the dynamic load rating
C, that provides the most valuable
information regarding the performance
of a bearing product with regard to the
particular application.
The modified rated life combines
the basic rating life with the stress-life
modification factor. The comparison
of L10m will avoid hidden aspects in the
particular definition of either factor.
As will be shown hereafter, by using a
bearing selection criterion based on the
modified rated life L10m, users can avoid
pitfalls and arrive at informed decisions
for the selection of their bearings and
the optimization of their products.
Example of Newest Method for
Gearbox Bearing Design
The following bearing application example
was selected to illustrate that the
dynamic load rating of the bearing C is
less crucial as generally believed, than
is the actual expected performance of a
bearing application. The purpose of this
example is to highlight that using modern
life calculation methods provides
more understanding to the designer
of what issues may be faced by bearings,
and consequently more chance to
the designer to make adequate design
choices. Comparisons of different life
methods have been done by Uherek
(Ref. 36) for several gearboxes. In these
analyses, it is observed that contamination
and lubrication were already key
factors in the design.
The application example is a threestage
helical gear unit, with the following
general characteristic and design:
- This gear unit has a reduction ratio of
40, with 3 stages
- The input speed is 1,400 rpm
- The nominal power is 66 kW, which
correspond to an output torque of 18
kNm
- Lubricated with circulating oil with
filters, mineral oil of 320 mm2/s @
40°C
- The contamination level (for the
contamination factor ηc) is ranked
ISO -/17/14
- It is assumed that the operating
temperature is 80°C
- Examining the results of Table 1 and
Figure 6, the following observations
can be made:
- There is no direct correlation
between the dynamic load rating,
i.e., basic rated life, and the
actual modified rating life of the
application.
- The basic rating life doesn't show the
bearings that are at risk, i.e., shorter
lives. Indeed the bearings that are
most at risk are: the Intermediate
shaft 2B and the output shaft B, both
bearings were indicated as quite safe
by the basic rated life.
- The modified rating life clearly
indicates that two bearings that
have shorter lives, and also the
technical reasons behind the
reduced endurance, i.e., lubrication
(low κ) and contamination issues
(low contamination factor ηc). Thus
surface fatigue problem can be
expected rather than subsurface
fatigue.
A usual procedure that is utilized
when life values are found too short is to
select a bigger bearing, due to its higher
capacity. However, the designer must
be aware that the selection of bearings
with an increase of the dynamic load
rating C would not solve the lubrication
and contamination issue. Even if an increased
capacity would show a slightly
longer life (a 10% higher capacity
leads to 33-37% higher life), it does not
change the phenomena: the problem
is surface induced stresses, originated
by the surface micro-geometry and the
effect of solid particles. Also in today's
gearbox, due to their high power density,
the space is often limited, and it
can be impossible to consider a bigger
bearing size, as a solution.
These stresses can't be reduced by an
increase of the dynamic load rating of
the bearing. Corrective actions to improve
the reliability of the intermediate
(2B) and output shaft (B) bearings
require not an increased dynamic load
rating of the bearing but actions to improve
the tribology of the surfaces in
contact, (Refs. 30-31). Therefore, proven
EP additives in the lubricant and
preventive measurements to reduce the
presence of particles and debris in the
oil can provide good results.
According to the analysis of the modified
life rating calculation, it is possible
to propose the following improvements
to increase the life of the weakest two
bearings:
- Use oil containing effective EP
additives
- Improve the cleanliness to ISO
-/15/12 level
- Both corrective actions at the same
time
Figure 7 shows the relative improvements
that would be possible to achieve
in relation to the original modified life
rating shown in Figure 6.
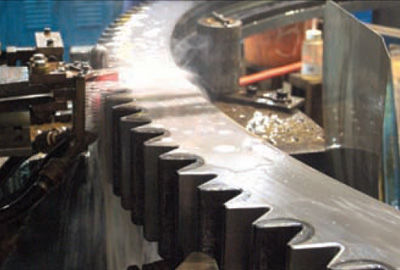
Figure 6 Overview of the modified life rating of the gearbox bearings normalized to the basic rating.
- Examining the results of Figure 7, the
following can be found:
- The use of oil containing proven EP
additives would provide the most
significant improvement—especially
in the two low-speed output shaft
bearings.
For the intermediate shaft bearing
(2B), an improvement of 40% is obtained
by improvement in the oil cleanliness.
Combining this improvement
with an optimized EP-additive of the oil
can provide a further 80% life increase,
thus enabling attainment of the required
rated life for this class of applications.
This gearbox bearing calculation example
shows how to use the modified
rated life of bearings to improve the
performance of a few critical bearings.
Yet doing so will provide significant increased
performance to the complete
system. This transparent and simple
optimization process would not be possible
using the basic rating life or selecting
the bearing based only on the value
of the dynamic load rating C.
Indeed, for the input shafts A and B
the dynamic load rating is quite unimportant
as the size of the bearing is dictated
by the required shaft size. On the
other hand, for the intermediate and
output shafts, the use of the basic load
rating C would give no useful information
for the improvement of the long
term reliability of this gearbox. Selection
of the input shafts A and B bearings
based on inflated values of the dynamic
load ratings C to reach an increased reliability
for the system would fail. This
is because it would not address the
elimination of the surface stress system
related to the low speed of the output
shaft with a viscosity ratio (κ) of 0.3.
Of course the final design decision
must take other parameters and constraints
into account, but applying the
modified life rating method allows the
designer to make more informed decisions
on alternative solutions with an
enhanced understanding of bearing
operating conditions and the expected
consequences of the application performance.
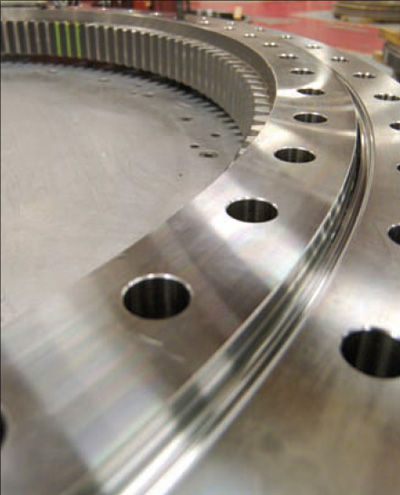
Figure 7 Relative increase of bearing life as result of corrective actions about lubricant EP additives and improved cleanliness of the oil.
Further Discussion on
Selection Criteria of Rolling
Bearings
The above gearbox bearing calculation
example shows that the design optimization
process can only be applied if the
life calculation informs the designer on
potential problems and hidden risks.
This should be done by looking at the
modified life rating, as the basic rated
life would be not able to provide such
critical information.
The basic rated life and the dynamic
load rating C basically represent the
subsurface fatigue performance of the
bearing. In other words, the fatigue performance
at extremely high load C/P~2,
and as such it cannot contribute much
to applications normally operating at
much lower loads for reliable operation
and extended periods of time.
Gearbox designers that rely solely on
the C/P parameter as a selection criterion
for the bearing can also easily
fall into believing that higher C values
will ensure a higher reliability for the
application. In such a case the attraction
for the selection of bearings with
inflated dynamic load ratings C will be
irresistible, with possibly unfortunate
consequences for the actual field performance
of the application.
To explain this important issue in
some detail we refer to the contact pressure
and related subsurface von Misses
stress field in the case of two rolling
bearing contacts — one (a) with an idealized
nominal smooth geometry, the
other (b) with its real surface micro-geometry
in contact (Ref. 27) (Fig. 8).
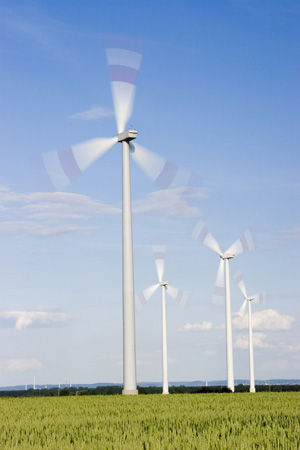
Figure 8 Example of stress field a) nominal smooth contact geometry, b) actual rough geometry
(Ref. 27).
In the case of reduced lubrication or
a presence of contamination particles,
the contact (b) will exhibit a severe
stress system right at the surface of the
rolling contact. This stress system is the
direct result of the asperities and microprofile
geometry that are not part of the
ISO specification of dynamic load rating
C (which refers to the nominal geometry
of the bearing and good lubrication
conditions, i.e., good separation
of surfaces by a clean lubricant film).
Therefore these stresses can't be reduced
by adopting a bearing with increased
C. Note that if a bearing rated
with an inflated C, and used under the
same C/P conditions, will lead to the
actual increase of the contact pressure
and a further intensification of the surface
stresses of the contact.
The problem of reducing high surface
stress in the rolling bearing is therefore
not by acting on the dynamic load rating,
but by acting on the tribology of the
Figure 7 Relative increase of bearing life as result of corrective actions about lubricant EP additives contact for the restoration of the protecandtive lubricant film or reduction of geometrical
imperfections. As discussed
earlier in this paper, this means working
with the chemistry of the lubricant
and preserving the geometrical quality
of the rolling surfaces by improvement
of the lubricant cleanliness.
Failure Mode from the Field
and Implications for Bearing
Selection
There are several studies about the type
of damage found in bearings that are
replaced during routine maintenance
work. Engel and Winter (Ref. 32) in 1979
reviewed the results of damaged bearings
originated from an estimated total
installed bearing population of several
million bearings and arrived at the
conclusion that although actual failed
bearings are very small in proportion
of the original population (0.05%), the
predominant failure mode in the field
is either lubrication- or contaminationrelated.
They found that lubrication and oil
contamination account for 75% of all
bearings failure. This same conclusion
is also reported by Nierlich and Volkmuth
(Ref. 35), who reviewed detailed
previous data, correlating this to detailed
observations and measurements
of damaged bearing surfaces.
In a separate and extensive investigation
supported by the German research
council for drivelines technology
(Ref. 33), conducted among the member
companies of the FVA association,
it was found that the most predominant
bearing failure modes experienced in
the field were inadequate lubrication
and contamination. This investigation
also reported and discussed in detail
with other results by Gläntz (Ref. 34).
From the observation of the failure
modes of field bearings, one can conclude
that subsurface fatigue-initiated
failure is in fact very rare. This is to be
expected, as most bearing applications
are selected based on a C/P design criterion,
which is a good method to avoid
classical subsurface-initiated fatigue
failure—particularly under good lubrication
conditions (Fig. 9).

Figure 9 Causes of rolling bearing failure as percentage of responses from an enquiry among the
companies of the FVA associations (Ref. 34).
However, the presence in the marketplace
of artificially inflated dynamic
load rating C may put in jeopardy this
good record. Indeed, as observed earlier,
today there is the risk that the unusually
increased C figures may correspond
in reality to a lower expected
dynamic carrying capacity of the bearing,
leading to a reduction, rather than
an increase, of the actual reliability of
the application.
Conclusion
Today's gearboxes require high reliability
and extended life. The trend to increased
performance will continue in an
effort to develop more energy-efficient
mechanical systems. At present the most
commonly used method of selecting a
bearing for a given application is based
on the dynamic load rating C. This paper
has shown very clearly that this methodology
has several drawbacks and may
not lead to an increased reliability for the
system. To avoid risk of reduced or unexpected
performance, well-informed
designers should base their decision on
these simple and practical rules:
- Engineers should look with critical
eyes the printed C values in bearing
catalogues, looking for consistency
with either ISO 281 or bearing
manufacturer testing practices.
- Today, the use of the modified
rated life is straightforward and
transparent. It is fully documented
in the ISO 281 and based on physical
operating characteristics of the
bearing, as viscosity ratio of the oil,
pitch diameter, lubricant cleanliness
class, rotary speed of the bearing etc.
The use of this calculation should
replace current simple practices
based only on the use of the C value.
- As shown in the gearbox calculation
example:
- Bearing lives based on the
modified rated life can provide
expected lives that can be larger than the basic rating life. These
are the bearings that are normally
scrapped as not failed at the end of
the gearbox life.
- There are also some bearings that
are critical for the reliability of
the system. The modified rating
life "ISO 281" is the only public
tool available to detect bearing
criticality and evaluate possible
corrective design modifications for
performance optimization.
Acknowledgment. The authors wish
to thank Mr. Alexander de Vries, Director
SKF Product Development, for his
permission to publish this article.
Antonio Gabelli is senior
scientist working at SKF
on tribology and rolling
contact fatigue life of rolling
bearings. He joined the
Engineering and Research
Center of SKF in Netherlands
in 1981, since than he
published many research papers on fatigue
and lubrication of rolling bearings. He was one
of the key contributors to the new bearing life
theory, developed by SKF in the 90's He is also
author of several patents on rolling bearings.
He holds a mechanical engineering degree
from the University of Padua (Italy) and a PhD
degree in from Chalmers Technical University of
Gothenburg (Sweden).
Upon graduation in 1999
with a degree in mechanical
engineering from Technical
University of Compiegne
(UTC), France, Armel Doyer
joined SKF the following
year in the company's
development department for
deep-groove ball bearings.
He has since held various positions within
that department, focusing predominantly on
automotive and industrial applications, where
he contributed to SKF's first launch of energyefficient
bearings. Doyer since 2008 has been
working as a project engineer within SKF's
Industrial Drive organization, with a focus on
understanding industry technical needs and
in support of SKF's development towards the
industrial gear unit market.
Guillermo E. Morales-
Espejel is principal scientist,
SKF Engineering & Research
Centre, The Netherlands,
and a visiting professor at
LaMCoS, INSA de Lyon. He
holds a PhD in tribology from
the University of Cambridge,
a "Habilitation à Diriger des
Recherches (INSA-Lyon),” and has15 years of
experience in rolling bearings. Morales-Espejel
has authored more than 50 scientific papers and
several book chapters with a focus on bearing life,
friction, lubrication and surface life.
References
- Palmgren, A. "On the Carrying Capacity and
Life of Ball Bearings," Ball Bearing Journal,
034, pp. 34-44, 1937.
- Lundberg, G., and A. Palmgren. "Dynamic
Capacity of Rolling Bearings," Acta
Polytechnica Mechanical Engineering Series,
Royal Swedish Academy of Engineering
Sciences, Vol. 1, No. 3, 7, (1947), and Vol. 2,
No. 4 (1952).
- Weibull, W. A Statistical Theory of the
Strength of Materials, Ingeniors Etanskaps
Akademien Handlingar, 1939, 151, p. 45.
- Lieblein, J. and M. Zelen. "Statistical
Investigation of the Fatigue Life of Deep-
Groove Ball Bearings," Journal of Research of
the National Bureau of Standard, Vol. 57, No.
5, Research Paper 2719, November, 1956, pp.
273-316.
- Tallian, T.E. "Weibull Distribution of
Rolling Contact Fatigue Life and Deviations
Therefrom," ASLE Transactions, Vol. 5, No. 1,
April 1962.
- Wallin, E. "Rolling Bearing Reliability:
Service Experience and Product
Development," Ball Bearing Journal, 221,
1984.
- Fleck, W. "Design Prospective Power-Density
Concept for Gearbox Bearings," Automotive
Engineer, August, 1992, pp.50-54, AGMA
14FTM16
- ISO 281:2007. Rolling Bearings — Dynamic
Load Ratings and Rating Life, 2nd Ed., 2007.
- Tallian, T.E., Y.P. Chiu, D.F. Huttenlocher, J.A.
Kamenshine, L.B. Sibley and N.E. Sindlinger.
"Lubricant Films in Rolling Contact of Rough
Surfaces," ASLE Trans., 1964, 7, 109–126.
- Tallian, T.E., L.B. Sibley and R.R. Valori.
"Elastohydrodynamic Film Effects on the
Load-Life Behavior of Rolling Contacts," In
Proceedings of the ASME Spring Lubrication
Symposium, New York, 8 June, 1965, ASME
paper no. 65-LUBS-11.
- Liu, J.Y., T.E. Tallian and J.I. McCool.
"Dependence of Bearing Fatigue Life on Film
Thickness To Surface Roughness Ratio," ASLE
Trans., 1975, 18, 144–152.
- Andréason, S. "Life and Reliability of Rolling
Bearings," Ball Bearing Journal, 168:1971.
- Andréason, S. and T. Lund. "Ball Bearing
Endurance Testing Considering EHD Lubrication," In Proceedings of the Leeds
EHL Symposium, 1972, Vol. C36, pp. 138–141
(Professional Engineering Publishing, St
Edmunds, London).
- Andréason S. and B. Snare. "Adjusted Rating
Life of Rolling Bearings," Ball Bearing Journal
184, 1975, pp. 1-6.
- SKF Publication 2800. General Catalogue,
SKF Gothenburg, Sweden, 1970.
- SKF Publication 3000. General Catalogue,
SKF Gothenburg, Sweden, 1978.
- ISO 281/1:1977 (E). Rolling Bearings
Dynamic Load Rating and Rating Life.
- SKF Publication 3200. General Catalogue,
SKF Gothenburg, Sweden, 1981.
- ISO 281/1:1990 (E). Rolling Bearings
Dynamic Load Rating and Rating Life.
- Ioannides, E. and T.A. Harris. "A New Fatigue
Life Model for Rolling Bearings," Trans.
ASME, J. of Trib., 107, pp. 367-378 (1985).
- loannides, E., B. Jacobson and J.H. Tripp.
"Prediction of Rolling Bearing Life under
Practical Operating Conditions," Proc. 15th
Leeds-Lyon Symp. on Trib., Leeds 1988,
Elsevier, pp.181-187, 1989.
- SKF Publication 4000. General Catalogue,
SKF Gothenburg, Sweden, 1989.
- Ioannides, E., G. Bergling and A. Gabelli. "An
Analytical Formulation for the Life of Rolling
Bearings," Acta Polytechnica Scandinavica,
Mechanical Engineering Series No. 137,
pp 9-12, 21-24, The Finnish Academy of
Technology, 1999.
- Gabelli A., G.E. Morales-Espejel and E.
Ioannides. "Particle Damage in Hertzian
Contacts and Life Ratings of Rolling
Bearings," Tribology Transactions, 51:4, 428-
445, 2008.
- ISO 281: (2007). Rolling Bearings—Dynamic
Load Ratings and Rating Life, 2nd Ed., 2007.
- ISO/TR 1281-2. Rolling bearings -
Explanatory notes on ISO 281-Part 2:
Modified Rating Life Calculation Based on
a Systems Approach to Fatigue Stresses, 11th
Ed., 2008.
- Gabelli, A., A.P. Voskamp, S. Shearer and
E. Ioannides. "The Service Life of Rolling
Elements Bearings - Stress Field and Material
Response Analysis," VDI Berichte Gleit Und
Walzlagerungen, 1380, 1998.
- Wendeberg, H. "Gearbox Bearing Service
Life – A Matter of Mastering Many Design
Parameters," AGMA 11FTM21.
- Vasconi, S. and D. Raju. "Virtual
Optimization of Epicyclical Gearboxes in
Wind Turbines," AGMA 12FTM06.
- Gabelli, A., E. Ioannides and E. Miglietta.
"Increased Life Performance of Rolling
Element Bearings in Gearboxes and
Transmissions," in Proc. of Int. on Gears,
VDI-Bericht 1230, Verein Deutscher
Ingenieure, pp.631-645, 1996.
- Gabelli A., A.M. Kerrigan and E. De Blic.
"HN-Treated Rolling Bearings for Extended
Service Life," Progress in Heat Treatment
and Surface Engine; Proceedings of the Fifth
ASM Heat Treatment Conference, Goteborg,
Sweden, 2000.
- Engel, L. and H. Winter. "Rolling Bearing
Damage," Antriebstechnik, 18, Nr. 3, pp. 71-
74, 1979, AGMA 14FTM16.
- FVA German Research Council for Driveline
Technology. Forschungsvorhaben No. 179,
"Partikelschäden," Final Report, 1992.
- Gläntz, W. "Contamination in Lubrication
Systems for Bearings in Industrial
Gearboxes," Ball Bearing Journal, 242, pp.
20-26, 1993.
- Nierlich, W. and J. Volkmuth. "Schaden
und Schadensverhütung bei Wälzlagern,"
Sonderdruck aus Antriebstechnik, 40, Nos. 1
and 2, 2001.
- Uherek, F.C. "Influences of Bearing Life
Considerations on Gear Drive Design,"
AGMA 05FTM17.
- Kasseris, E.P. "Comparative Analysis of
Automotive Powertrain Choices for the Near
to Mid-Term
- Future," PhD Thesis, Massachusetts Institute
of Technology, June 2006.
Printed with permission of the copyright holder, the American Gear Manufacturers Association, 1001 N. Fairfax Street, Fifth Floor,
Alexandria, VA 22314-1587. Statements presented in this paper are those of the author(s) and may not represent the position or opinion
of the American Gear Manufacturers Association.