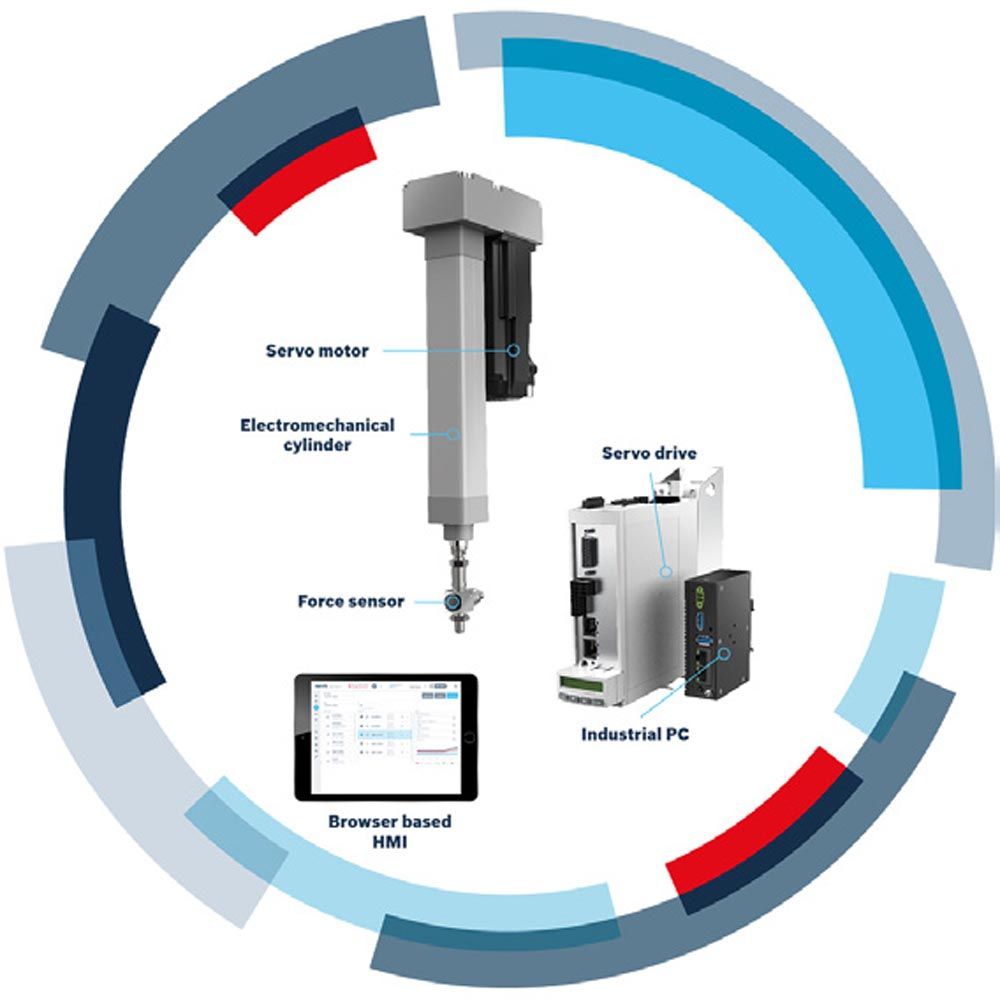
“We’re always trying to make our processes simpler and to do as much as we can ourselves—ideally with standard components and without programming effort,” said Jean-Marc Hubsch, engineering manager in Sensata’s Industrial Encoders division. According to Hubsch, the idea of a production line which can cost-effectively produce 1,000 or 10,000 versions of a sensor system in small batches is new, but future oriented. Preconfigured modules, which his team merely needs to put together and parametrize for commissioning, are key.
Smart Function Kit for Pressing Processes
The construction engineer saw the appropriate solution at the Hannover trade fair in 2019: The Smart Function Kit from Bosch Rexroth—a mechatronic package including mechanical, electrical and software, for standardized pressing and joining applications within the force range from 2–30 kN.
“This easy-to-use kit is not only interesting for system integrators, but it also benefits end customers like Sensata, who have their own process know-how,” Rexroth Project Manager Laurent Steinmetz explained. The Smart Function Kit for pressing and joining applications combines proven standard components like an electromechanical cylinder (EMC), a force sensor, a servomotor, a drive controller, and an industrial PC with an intuitive HMI software, running device-independently on the browser and can be operated via tablet.
Zero Programming
The Sensata engineers made use of visual programming: instead of coding line by line, they selected predefined software blocks and created a sequential workflow via drag and drop. In order to define the individual processes in the joining procedure, they simply enter the associated parameters. The drive controller is automatically parametrized and commissioning is supported by a wizard.
“Compared to the previous practice, the engineering time is reduced by up to 95 percent,” said Steinmetz. The simple analysis of the pressing process with validation elements ensures time savings within the operation phase.
For monitoring purposes, status information and process results including a force displacement curve are shown and recorded live. “All data are transferred straight to our IT system where they are stored and analyzed for quality assurance purposes,” reported Hubsch. “This means much greater transparency during production.”
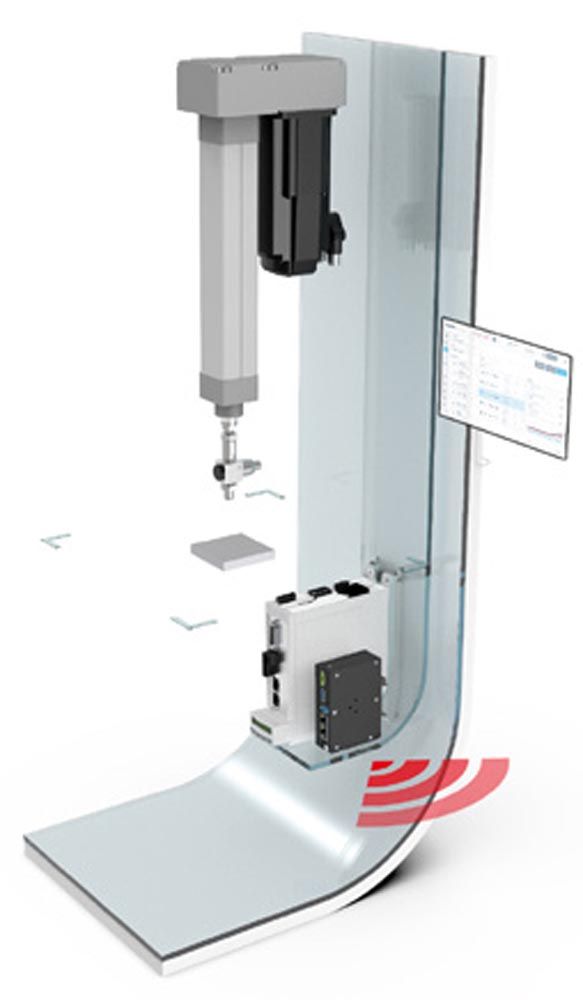
Precise Individual Processes
The high quality and precision of each individual hardware component were also reasons why Sensata engineers chose the Smart Function Kit. It’s current task of pressing in the housing flange with the help of three distance bolts, is carried out with a maximum force of 800 daN and +/-0.02 mm accuracy. Although the configuration of the products on the line varies considerably, the solution is 100 percent reliable. In the final stage of the production line, the Smart Function Kit obtains the individual production parameters from a chip on the workpiece pallet via an RFID solution.
Scope for Line Integration