To begin to address the confusion regarding pipe threads, it is helpful to take a step back and investigate some of the reasons for this confusion, some of which are listed below:
Different designations use the same nominal sizes (e.g., 1/2), even though they may have different thread profiles, dimensions, and tolerances.
Some of the designations have similar letters in the nomenclature but are not necessarily equivalent (NPT, BSPT, PT).
Certain historical designations are still extensively used, such as BSPP and BSPT.
Certain sizes of different thread standards can be screwed together, but not in a leak-proof manner. This means that physically fitting two threads together does not guarantee proper fit and leak prevention.
Different thread types require different sealing methods (sealant, O-ring, etc.).
Within each standard, the relationships between thread series are clear. Problems mainly arise from attempts to combine threads from different standards. The next section will address some of these problems and clarify which thread series are equivalent and compatible, and which are not.
Thread Compatibility
A compatibility chart of selected thread series is shown below in Table 2.

Table 2—Compatibility between selected thread series, with equivalent series grouped together.
The cases of partial compatibility listed in Table 2 are mainly attributable to the tolerance difference between Rp and internal G threads, as shown in Figure 3. These two thread series have identical nominal dimensions but have different tolerances on the pitch diameter. The internal G thread has a +/0 tolerance above the nominal value while the Rp thread has a ± tolerance (Refs. 5, 6).
For the Partial1 case, this means that there will not be issues threading parts together, but the use of a thread sealant is especially critical.
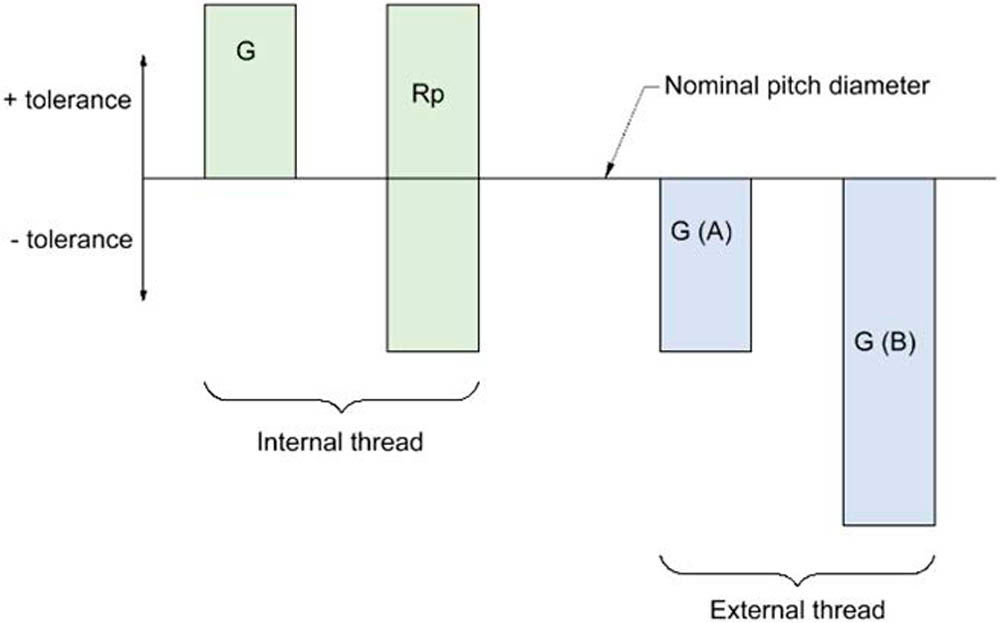
Figure 3—Comparison between pitch diameter tolerance of G and Rp series.
The bigger issue arises in the Partial2 case. External G threads come in two classes (A and B), which both have a 0/- tolerance, and therefore there is no interference risk when threading into an internal G thread. However, when attempting to thread into an Rp internal thread, it is possible that the external thread pitch diameter will be larger than the internal thread pitch diameter. In this situation, it would be extremely difficult, if not impossible, to physically thread the external thread in.
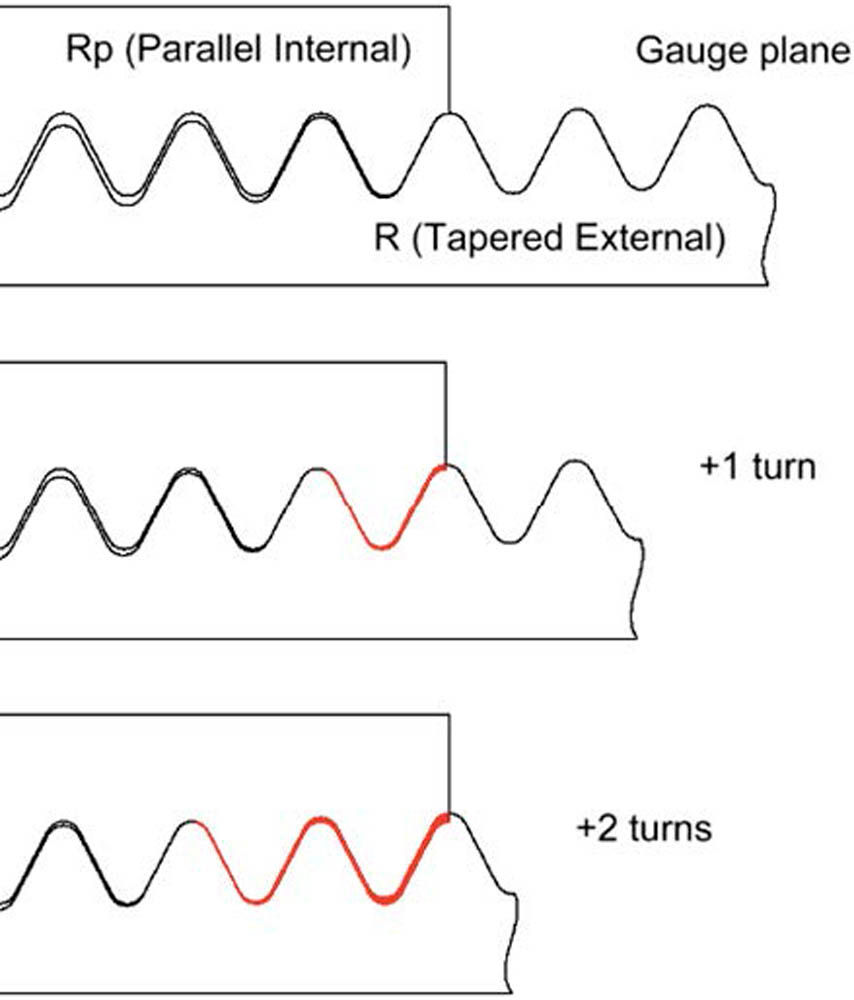
Figure 4—Diagram showing the connection between R 1/2 and Rp 1/2. The red area
indicates where plastic deformation leading to a seal occurs.
Another important topic is the relationship between NPT and the ISO thread series. These two families of threads have different flank angles and root shapes and are not compatible with one another (see Table 2). However, it is sometimes possible to physically thread these two series together due to similar thread pitch and pitch diameters. This is especially true of the sizes designated 1/2 and 3/4 because the thread pitches of these sizes are exactly the same for both standards (Ref. 9). Although it may be possible in certain circumstances to physically thread these two series together, a pressure-tight seal is unlikely and certainly not guaranteed.
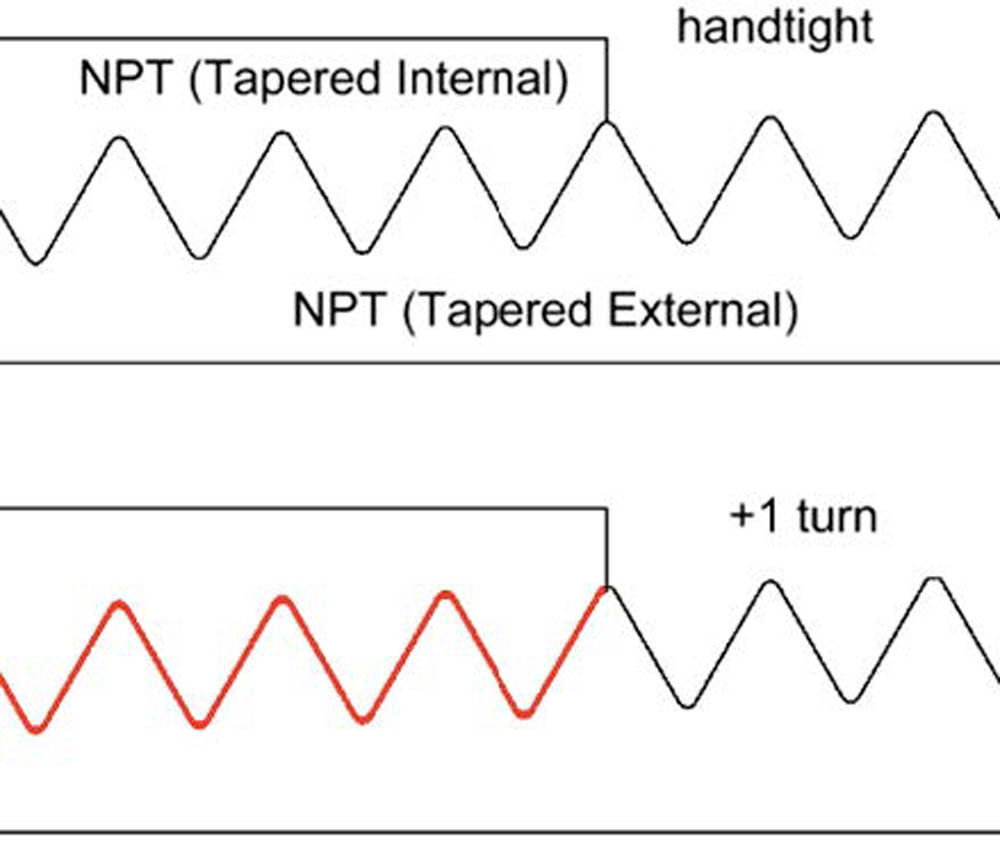
Figure 5—Diagram showing a 1/2-14 NPT connection. The red area indicates where plastic deformation leading to a seal occurs.
Figure 4 shows an engagement between an R thread and Rp thread (which are designed to mate with each other). As the external thread is tightened beyond the gauge plane with a wrench, plastic deformation leads to sealing. Similarly, a complete seal on the threads occurs with an NPT connection, as shown in Figure 5. Remember that both connections require a sealant to guarantee a pressure-tight seal.
When an R external thread is threaded into an NPT internal thread (see Figure 6), problems begin to arise. In this case, the difference in flank angle and root/crest shape mean that portions of the threads will begin to experience excessive plastic deformation while other areas (mainly at the roots of the internal thread) will still have clearance between the threads. This can lead to a phenomenon known as “spiral leakage” (Ref. 4).
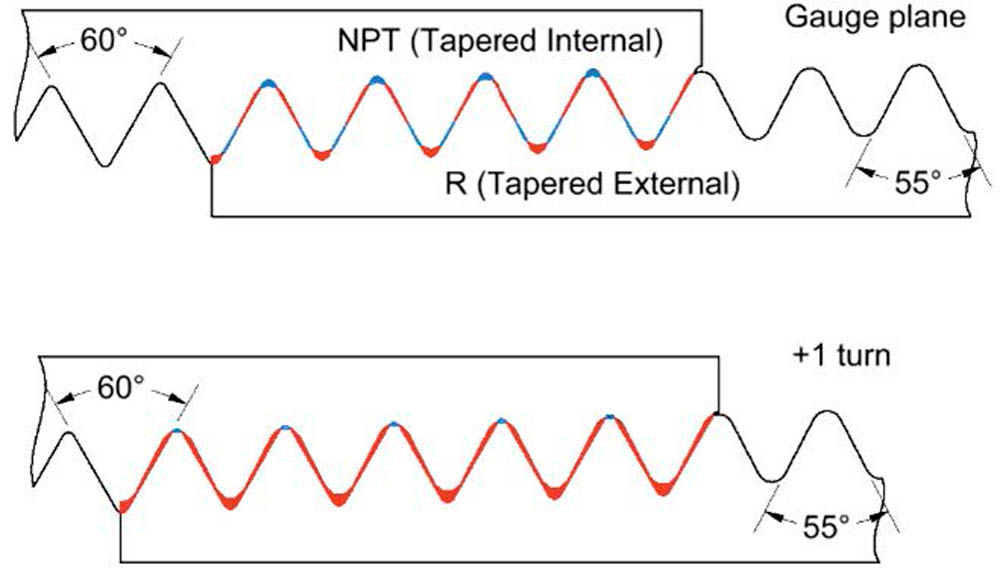
Figure 6—Diagram showing a connection between R 1/2 and 1/2-14 NPT. The red areas indicate where plastic deformation occurs and the blue areas indicate where clearance is present in between areas of interference. Note the small regions of clearance in the roots of the NPT thread at +1 turn.
The situation is even worse when an external NPT thread is threaded into an internal Rp tapped hole or fitting, as shown in Figure 7. In this case, the gaps remaining between portions of the two threads are even more pronounced despite excessive interference in other areas. Whatever the combination may be, a connection between an American National Standard thread (e.g., NPT) and an ISO thread (e.g., Rp or G) is not recommended and should not be used.
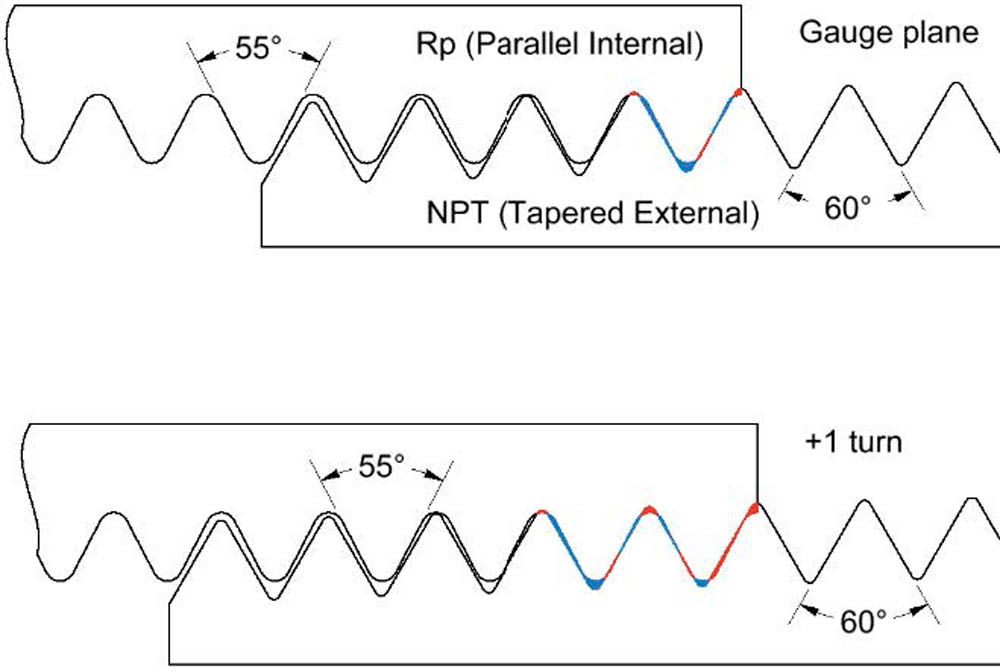
Figure 7—Diagram showing a connection between 1/2-14 NPT and Rp 1/2. The red areas indicate where plastic deformation occurs, and the blue areas indicate where clearance is present in between areas of interference.
Conclusion
The preceding information on pipe thread compatibility is critical for anyone who is designing, inspecting, or assembling a threaded connection. For applications where maintaining pressure or sealing is necessary, one must ensure that the correct threads are being used. It is not safe to assume that a connection is adequate just because the threads can be screwed together. For this reason, controlling plug and fitting inventory is crucial because different thread series often cannot be easily distinguished from one another.
When using 55° flank angle threads (i.e., ISO, BS, and JIS thread designations), the best approach is to specify the G or R series instead of BSPP/BSPT or PT/PF/PS. The G and R designations are not only the correct designations according to the latest ISO, BS, and JIS standards, but also help to eliminate confusion and misinterpretation. In particular, extreme caution must be taken when working with the old British Standard designations. “BSP” is often used to indicate BSPP, but this is not always the case. Similarly, BSPT on an internal thread would most likely indicate a tapered internal thread (i.e., Rc) but may actually refer to a parallel internal thread (i.e., Rp). Be sure to clarify with vendors exactly what thread series is being supplied and use the G and R designations on all new designs wherever possible.
In addition to the items brought up in this paper, there are a variety of other variables to consider when designing, inspecting, and assembling pipe threads. The material of both parts, the internal pressure, the sealant used, the type of fluid inside, and other factors can all have a substantial impact on the threaded connection. That being said, this paper will equip you with the basic knowledge you need to handle threaded connections with confidence.
References
- British Standards Institution. (2023). Pipe threads where pressure tight joints are made on the threads - Taper external threads and parallel internal threads. Dimensions, tolerances and designation (BS EN 10226-1:2004). Retrieved from bsigroup.com: https://knowledge.bsigroup.com/products/pipe-threads-where-pressure-tight-joints-are-made-on-the-threads-taper-external-threads-and-parallel-internal-threads-dimensions-tolerances-and-designation
- British Standards Institution. (2023). Pipe threads where pressure tight joints are made on the threads - Taper external threads and taper internal threads. Dimensions, tolerances and designation (BS EN 10226-2:2005). Retrieved from bsigroup.com: https://knowledge.bsigroup.com/products/pipe-threads-where-pressure-tight-joints-are-made-on-the-threads-taper-external-threads-and-taper-internal-threads-dimensions-tolerances-and-designation
- British Standards Institution. (2023). Pipe threads where pressure-tight joints are not made on the threads - Dimensions, tolerances and designation (BS EN ISO 228-1:2003). Retrieved from bsigroup.com: https://knowledge.bsigroup.com/products/pipe-threads-where-pressure-tight-joints-are-not-made-on-the-threads-dimensions-tolerances-and-designation
- Colder Products Company. (2022). Understanding pipe threads: types and designations. Retrieved from cpcworldwide.com: https://www.cpcworldwide.com/Portals/0/Library/Resources/Literature/WhitePapers/Documents/CPC-Pipe-Thread-Types-and-Designations.pdf
- International Organization for Standardization. (1994). Pipe threads where pressure-tight joints are made on the threads (ISO 7-1:1994).
- International Organization for Standardization. (2000). Pipe threads where pressure-tight joints are not made on the threads (ISO 228-1:2000).
- Japanese Standards Association. (1999). Taper pipe threads (JIS B 0203:1999).
- Japanese Standards Association. (2010). Parallel pipe threads (JIS B 0202:1999).
- Oberg, E., Jones, F. D., Horton, H. L., Ryffel, H. H., & McCauley, C. J. (2020). Machinery’s Handbook, 31st Edition. South Norwalk, Connecticut: Industrial Press, Inc.
- The American Society of Mechanical Engineers. (2013). Pipe Threads, General Purpose, Inch (ASME B1.20.1-2013).
- The American Society of Mechanical Engineers. (2018). Dryseal Pipe Threads, Inch (ASME B1.20.3-1976 (R2018)).