Improper asset operation occurs when one:
- Overloads mechanical components like conveyor belts
- Utilizes equipment in the wrong environments
- Operates machinery at extreme speeds
- Exceeds the desired pressure and temperature limits
These conditions exert extra stress and strain on mechanical systems. Surface friction, heat, and additional mechanical stresses cause rapid wear of mechanical components.
Adhering to the designed asset operating parameters ensures machinery is utilized for its intended use. It also guarantees proper loading to keep stress and strain on mechanical elements within acceptable limits. That way, assets cannot struggle to achieve their productivity levels.
Mechanical overloads in a milling facility, for instance, emanating from excess torque, can cause irreversible damage to couplings, transmission systems, gear drives and shafts. The overloads can cause the jamming of mechanical motion elements causing further damage due to increased friction.
Companies should outline specific equipment operating conditions based on the manufacturer’s recommendations or design parameters. This prevents overloading or wrong process sequences by operators and maintenance teams. That way, companies can eliminate machinery operating conditions causing increased friction between mechanical moving parts.
Proper equipment operation reduces system vibrations, it also reduces the frequency and severity of unscheduled machinery breakdowns. Rapid vibrations create perfect conditions for the gradual degradation of parts. Emergency breakdowns can create undesirable conditions, like spillage of corrosive fluid media, which can corrode mechanical motion elements. Additionally, maintenance technicians can make errors as they strive to restore assets during emergency breakdowns.
One way to foster proper asset operation is to develop and enforce standard operating procedures. Provide adequate tools and detailed work instructions to ensure employees utilize machinery as intended. Adhering to standard operating procedures eliminates errors that can cause overloading and other undesirable conditions exacerbating wear and tear. Train employees to ensure they understand recommended machinery operating standards.
4. Continuously Monitor Operating Environments
Operating environments have significant impacts on the performance of different mechanical motion components. These components are manufactured from materials with varying physical and chemical properties. Some fabrication materials require strict regulation of environmental conditions.
High temperature, humidity, dust, or corrosive gases can expedite the degradation of mechanical components. Continuously monitoring operating conditions helps companies to identify environmental patterns or trends increasing tear and wear rates.
Monitoring operating environments takes into account:
- Contamination monitoring: How many contaminants, such as dust and abrasive debris, are within the working environment? Over time, companies should monitor the number of abrasive contaminants and develop appropriate control measures. Facilities or operations churning out massive amounts of dust can benefit from air filtration systems or dust collectors to protect mechanical motion components.
- Humidity and corrosion monitoring: Highly humid environments create perfect conditions for rust on metal components. Companies can utilize dehumidifiers to control the amount of moisture in enclosed spaces. This can reduce premature asset damage through surface corrosion.
- Temperature monitoring: High temperature causes thermal stress on mechanical components. Repetitive thermal stresses can lower the efficiency of mechanical motion components since they facilitate the gradual damage of parts. Temperature monitoring can also extend to internal machine parts. Companies can identify assets generating a lot of heat and insulate them or equip them with heat extraction equipment.
Monitor environmental variables over time and implement appropriate mitigation measures before they cause damage. Invest in relevant industrial sensors, like Internet of Things (IoT) sensors, for real-time monitoring and timely generation of alerts when conditions exceed predetermined levels. Maintain these sensors to enhance their accuracy and durability.
5. Handle Assets Correctly
The way companies handle assets determines the longevity and reliability of mechanical systems. Some practices accelerate the wear and tear of motion components, rendering them ineffective after a short time in service. Facilities require specific procedures for handling, storing, installing, using, and cleaning mechanical motion components. Stocking replacement motion components made from iron or steel in a dusty or humid space causes irreversible surface damage through gradual rusting.
Follow the correct procedures when lifting and transporting mechanical motion components. Use appropriate lifting equipment and hook equipment like motors using eyebolts on its body. Secure these components in the correct packages to protect them from abrasive or corrosive elements during transportation. Do not drop mechanical components from heights to maintain structural integrity and prevent physical damage.
Store mechanical motion components in a clean and dry environment. Indicate on the package if the mechanical parts are fragile. Use the right tools and adhere to recommended procedures during installation. Avoid excessive force when fastening mechanical motion components to avoid breaking, warping, or prematurely damaging them. Verify the alignment of different mechanical parts and check torque specifications when installing or replacing components.
Use appropriate cleaning agents when removing contaminants from assets. Avoid abrasive, tough cleaning tools or chemicals that might distort mechanical motion components or accelerate their degradation.
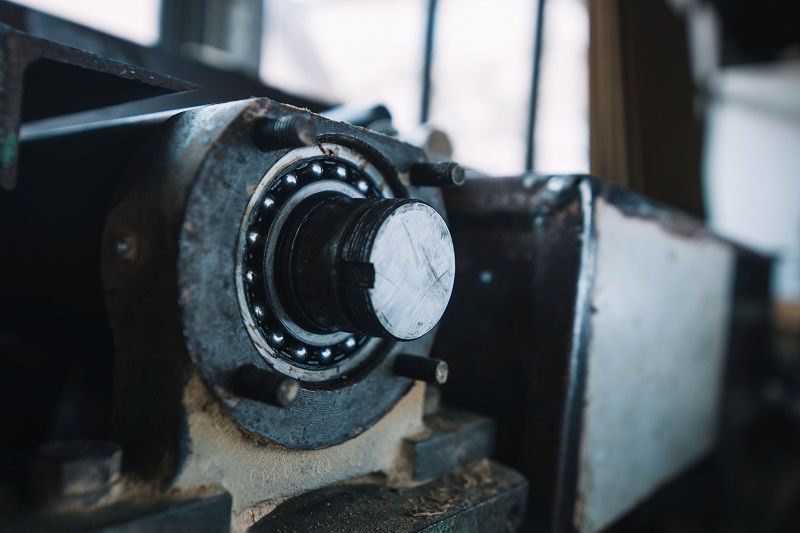
Combating wear and tear of mechanical parts enhances their performances, extends asset lifespan, and maximizes occupational safety and health.
Final Remarks
Implementing different solutions for minimizing the wear and tear of mechanical motion elements can yield desirable financial savings for any company. Combating wear and tear of mechanical parts enhances their performances, extends asset lifespan, and maximizes occupational safety and health.
Implement best practices and leverage advanced digital technologies to monitor and mitigate equipment degradation. Focus on continuously improving the quality of inspection and maintenance workflows. Collect and analyze equipment performance data to foster a data-driven wear and tear mitigation program, reduce operational costs, and optimize the reliability of mechanical motion components.
limblecmms.com
limblecmms.com/maintenance-definitions/scheduled-maintenance/
