Design Reviews - What to Review and When
Design Reviews—What to Review and When
Design reviews vary greatly by industry and regulatory requirements. We typically define them as Guidelines rather than Procedures, as this allows flexibility in their execution — both to skip over non-relevant sections and to dig deeper for those areas that go beyond the typical design and require closer examination. Having them as a “Procedure” can interfere with both of these variations. Our designs are mostly electro-mechanical- and motion control-oriented, so some of our checkoff list may not be needed in your application, while other whole areas may be required for your design reviews!
Here are what we cover in our typical design reviews. Some are trivial — did the title block get updated on all the sheets after a revision? Some are housekeeping — make sure the parts lists and fab drawings are updated from the final pass. Others pass on tribal wisdom, like asymmetric mounting of boards (see 4.5 below). Try to gain as much advantage when you do design reviews; they can result in greatly improved designs and can cut multiple iterations out of the process!
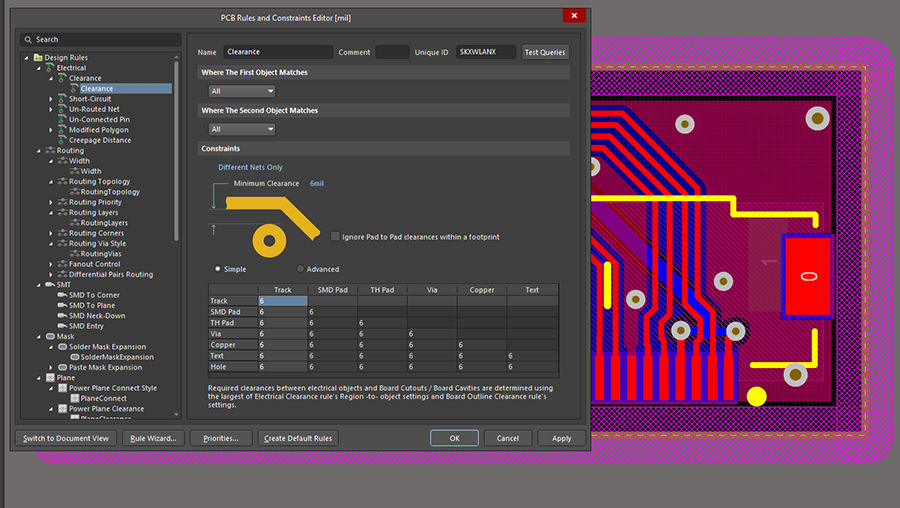
Regulatory
- 1.1 What requirements are specified for the system or subsystem?
- 1.1.1 Are we following? Plans for agency approval?
- 1.2 Is this a modification of an existing system that needs specific items to remain under existing compliances, and can those items remain unchanged?
- 1.2.1 Submit any changes to certification agency for approval or testing.
- 1.3 Are there specific procedures in place to avoid affecting critical sections of the design and critical components? Verify we are following them.
- 1.4 Do internal and external agencies need to review the changes for continued compliance?
- 1.5 Have all RoHS, Reach, etc. requirements been met with the components that have been selected? Have these been documented so they can be tracked. Back-ending this function is very difficult and may force a design turn!