Maximizing Bearing Performance
Carrier and SKF Collaborate on Centrifugal Compressor TechnologyThe opportunity to improve product design separates market leaders from the competition. Brand loyalty, perceived value, manufacturing technology, and research and development can play a significant role in identifying issues that are important to customers. Since 1902, Carrier has created a rich history of product innovation in the heating, air-conditioning and refrigeration industries. They continue to evolve with assistance from companies such as SKF.
“Carrier’s working relationship with SKF dates to the mid ’90s on oil lubricated rolling element bearings for centrifugal compressors. Carrier started the work on refrigerant lubricated bearings in the early ’90s and some of the key findings and challenges were shared with SKF’s research group. The end goal was to provide customers in the HVAC comfort cooling segment robust and cost effective refrigerant lubricated bearing compressors,” said Vishnu Sishtla, senior fellow, Carrier Compression Systems.
SKF’s collaboration with Carrier includes maximizing the performance, reliability and energy efficiency of the bearings utilized for centrifugal compressors.
“Carrier did not see the new technology as a solution to problems, but rather as an opportunity to improve their products,” said Magnus Arvidsson, manager drives and process industries competence center at SKF. “Carrier is a market leader and an important customer to SKF. With Carrier successfully deploying the new technology, competitors will be compelled to follow. Collaborating with Carrier also helps SKF to identify issues of importance to customers.”
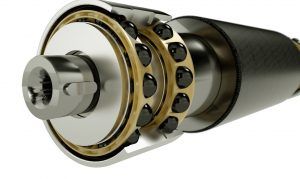
The technology in question was the replacement of conventional steel bearings with new steel and ceramic materials used originally in aerospace applications. Work conducted by Carrier researchers showed that conventional steel bearings lubricated with refrigerants had much shorter lifespans, according to Sishtla.
“New steels and ceramic materials were used in space applications. Both companies felt the need to bring the space-age technology to commercial applications through further research on materials and tribo-chemistry with new low-GWP refrigerants as lubricants,” he added.
In order to make the most out of the bearing technology, new drive technologies were introduced.
“Conventional compressors were gear-driven with large bearing loads, for example,” said Sishtla. “To use the SKF Hybrid bearing solution, the compressor architecture was changed to a direct drive without gears. The increase in overall efficiency due to lower mechanical losses and variable speed operation lead to decreases in the indirect global warming potential for a sustainable future.”
Surprisingly, the bearings were able to fit in the compressor envelope without adding complexity to the assembly. The collaboration was one of mutual respect and appreciation of research. Both Carrier and SKF had a good agreement in place that allowed free and open dialog between both companies.
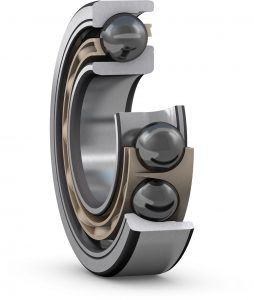
SKF is working on energy efficiency (and CO2 reduction) in the full value chain. “We are investing heavily in our own factories to improve both energy efficiency and reduce carbon emissions and have set the goal to be carbon neutral for our own manufacturing operations by 2030,” Arvidsson said.
SKF has reduced the CO2 per ton of produced bearings by almost 40% since 2016. The Group is also working upstream with major energy intensive suppliers (mainly steel and forging companies) on the reduction of the embedded emissions in the materials they procure.
“But the biggest contribution SKF makes in improving energy efficiency globally lies with what we can do with our customers. Our actions range from optimizing bearing and customer system designs from a friction and/or weight perspective with our advanced engineering tools to the active development and enabling of clean tech solutions for different industries,” Arvidsson said.
Energy efficiency is important in every market SKF reaches, but it is particularly important in the heating, air-conditioning and refrigeration industries. Arvidsson said that the cost of energy in these areas is about 70% of the lifecycle cost. When developing proposals to customers for bearings, energy efficiency is a main objective for SKF.
25+ Years of Research
In industrial refrigeration, rolling bearings are widely used in all rotary types of compressors, according to Guillermo Morales-Espejel, principal scientist at SKF. In the air conditioning and refrigeration industries, the lubrication of these bearings takes place using a mixture of oil and refrigerant—since it is expensive and virtually impossible to isolate the bearings from the refrigerant. The lubricating mixture exhibits a dramatic reduction of viscosity compared with that of pure oil due to the very low viscosity typical of liquid refrigerants.
Experimental data and many models have been published for the estimation of viscosity and viscosity-pressure coefficient for oil-refrigerant mixtures. However, the handling of this mixture brings many complications in the design and operation of the refrigerant compressors, i.e. reduction of the thermal efficiency (oil a contaminant in the refrigerant), oil separation devices have to be developed, regular oil changes, programmed maintenance, etc. Besides all this, loss of control in the proportion of the oil-refrigerant mixture during the operation of the compressor might damage the bearings.
Some 25 years ago, SKF Professor Bo Jacobson had the idea to make a test using ball bearings with ceramic balls instead of steel balls (known to work very well under poor lubrication conditions) lubricated only with refrigerant. The test lasted 200 hrs and after the analysis the bearings were in very good condition. This triggered the idea of developing a technology to completely get rid of the oil and lubricate the bearings with the same fluid media used for the refrigeration cycle. If successful, this will simplify the design of the machine and will produce a machine with (hopefully) no maintenance and completely hermetic reducing to nearly zero the release into the atmosphere of the refrigerant. An oil free compressor which would have a more efficient refrigeration cycle since the refrigerant would not be contaminated with oil.
Since then, SKF has optimized the hybrid bearing for pure refrigerant lubrication by selecting adequate materials to reduce the risk of surface distress, corrosion and cage malfunction, besides optimizing surface topography and manufacture quality, all this maximizes the bearing reliability for this application.
Successful Solutions
For many years, SKF has worked with customers to develop this technology into their specific designs and operating conditions. The organization has had several success stories and many years with compressors running in the field. The most successful—and most recent story—is with Carrier. The two companies plan to collaborate on additional projects in the future.
“We have plans to continue the collaboration in other areas where SKF has strengths,” added Sishtla, “such as seals and lubrication systems.”
For additional information on this technology, check out the technical article, “Progress in Rolling Bearing Technology for Refrigerant Compressors,” in the December 2017 issue of PTE:
https://www.powertransmission.com/issues/1217/bearings.pdf
www.carrier.com
www.skf.com