“And now we’re finally beginning to realize what’s happening and there’s finally some effort being put forth and I’m privileged to have a voice in that process.”
That “voice,” oddly enough, includes a song Leonard penned—a broadside, if you will—calling out decision makers over maintenance matters. He calls it “The Maintenance Crisis Song.” Here’s the first verse:
“No one wants to work in the boiler rooms,
No one wants to work with the tools,
The nation’s youth are taking the easy way out,
There’s no one left to fix our schools.
Maintenance technicians are ‘bout to retire,
Company executives got no one to hire,
How safe does that make you feel?
How safe does that make you feel?”
(Ed. Note: For complete lyrics, go to www.skilltv.net)
Indeed, aside from his “evangelist” persona, Leonard also possesses the heart of a showman—a P.T. Barnum-type marketer, if you will. He believes that’s what it takes in our American Idol culture to generate the attention this issue deserves. In the hope of reaching a wider audience, Leonard’s disturbing ditty has been recorded in a number of different genres—from rock to soul, from hip-hop to gospel. The song was the result, appropriately enough, of Leonard’s attendance in 2002 at a Society for Maintenance and Reliability Professionals (MSRP) conference in Nashville, long a hotbed for music making.
“(I decided that) just going to the conference and talking to engineers or writing articles about this isn’t going to fix it; we’re going to write a song;” he says. And after enlisting some musicians who put his lyrics to music, “Now we have nine different genres of the same song.”
Since then, Leonard has been on a whirlwind schedule that takes him all over the country and to Europe (Brussels, e.g., to offer the opening remarks at the EuroMaintenance Conference), delivering the word to business groups regarding the maintenance and reliability crisis. That includes trips to the nation’s capitol, as well. Leonard was invited to speak before a congressional Facilities Forum, and was also able to gain the ear of various congressmen, congresswomen and senators, all in the hope of lighting fires under behinds and initiating movement.
“In the last several months I’m finally meeting with some people who can actually do something about it. When I met with (Senator) Ted Kennedy (before his illness) I challenged him by asking why there isn’t an MIT or Harvard MBA program teaching the value contribution of maintenance. If you go to an average engineering or maintenance conference, there’s at least four or five different tracks that teach maintenance guys and engineers how to communicate with upper management to ask them for the resources that they need.
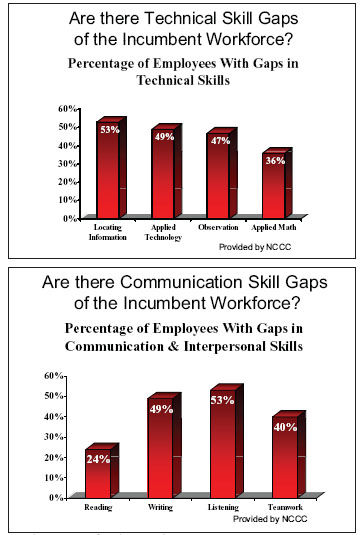
Graphs courtesy of Joel Leonard.
“And if upper management already understood (maintenance’s) value contribution, they could be managing towards that and the guys wouldn’t have to be asking permission to do their jobs.”
So how bad is the problem? The evidence is daunting.
For instance, when at that maintenance engineering conference in Nashville, the audience of engineers was asked how many would be retiring in the next 10 years. Answer—90 percent. And there’s no shortage of other examples. For instance:
- According to Council of Competitiveness’s Compete 2.0 Skills report, for every 10 workers who retire, there are only three to seven to replace them. The Bureau of Labor Statistics forecasts an annual shortage of 350,000 auto technicians through 2010.
- The American Welding Society states that the average welder today is middle-aged or older. They estimate that more than half of that segment’s workforce is nearing retirement and that a potential shortage of 200,000 skilled welders may exist by 2010.
- The average age of the power management workforce approaches 50, according to industry reports, with half of them slated for retirement in the next 10 years. Perhaps worse, an Edison Electric Institute survey states that about 20 percent of the nation’s electric transmission workforce is set to retire in the next five years.
Again, keep in mind that these shortages in skilled workers not only compromise the country’s infrastructure; they also affect a typical company’s bottom line. Who is going to repair the fleet trucks, the lift trucks and other necessary vehicles? Who is going to make welding repairs to your facility? Who is going to maintain your industrial motors and engines? Who will fix the plumbing? And speaking of plumbing, Leonard is fond of quoting John Gardner, a former U.S. Secretary of Health, Education and Welfare, to help make his point about the low regard that is held for the maintenance worker.
“The society that scorns excellence in plumbing, because plumbing is a humble activity, and tolerates shoddiness in philosophy, because philosophy is an exalted activity, will have neither good plumbing nor good philosophy. Neither its pipes nor its theories will hold water.”
As with most everything else these days, Leonard points out, even plumbing is much more than the low-tech trade of yesterday. He reminds that plumbing systems today are PLC-controlled and sensed, and contain high-tech lubricants and solvents and are integrated with electrical and electronic systems.
Leonard has traveled the globe preaching the gospel of reliable maintenance that is, essentially, two things—capacity and strategy. Maintenance should be considered part and parcel of a company’s best practices; it should be considered by any good business as a strategic decision, not just a knee-jerk reaction to something broken that needs fixing.
“Maintenance is the capacity assurance provider,” says Leonard. “And what we need is a structured, nationwide approach where we start investing in maintenance reliability as a value contributor—and start having MBA programs that teach that.
“It’s not a zero-sum game out there. As the rest of the world gets caught up and realizes that the American Dream can be had by all, we shouldn’t be bemoaning the success of others. What we should be doing is not forgetting what got us where we’re at and start abandoning some of the key components that made us successful. And that a qualified, skilled workforce is not something to look down our nose at.
“We need 2,000,000 maintenance engineers. Where are we going to get them? Everyone wants to play, but no one wants to plow.”
Amen, brother.
For more information:
Joel Leonard
Phone: (336) 338-1011
www.skilltv.net
MPACT Learning Center, LLC
Pinehurst Bldg. / Ste. 301
2 Centerview Drive
Greensboro, NC 27407
Phone: (336) 379-1444
Fax: (336) 379-1995
www.mpactlearningcenter.com
SMRP
8400 Westpark Drive / 2nd FL
McLean, VA 22102
Phone: (703) 245-8011; (800) 950-7354
Fax: (703) 610-0249
www.smrp.org