“We offer our roughly 240 plants a standardized ‘Industry 4.0 toolbox,’ which can be expanded and deployed as needed,” Najork says.
Bosch believes this will save it almost one billion euros over the next five years, following an investment of around 400 million euros.
The beginnings: Bosch does pioneering work on Industry 4.0
Back in 2011 at Hannover Messe, scientists presented an idea that broke with convention. Rather than have people adapt to machines, they turned things around. The vision here was of products that actively involve themselves in their manufacturing, navigate themselves through the production process, and communicate with humans and machines. It was the birth of Industry 4.0 — Bosch is one of its founding fathers.
In 2012, the company took over the chairmanship of the newly established Industry 4.0 working group to further develop the German government’s high-tech strategy. Bosch became a leading provider and a leading user of Industry 4.0, not only testing this modern form of manufacturing in its own plants, but also bringing proven solutions to the market. The Bosch plants in Blaichach in Germany, Anderson in the U.S., and Wuxi and Suzhou in China were pioneers in this domain and have been the recipient of multiple awards for their innovative concepts, including the designation of “lighthouse factories” by the World Economic Forum.
At the same time, one thing soon became apparent: “The only way to tap the full potential of Industry 4.0 is collectively and globally. Humans and machines need to ‘speak the same language.’ This requires international, cross-company standards,” Najork says.
Bosch worked together with other companies to develop OPC Unified Architecture (OPC UA), a machine language for Industry 4.0 that standardizes access to devices and systems and enables manufacturer-independent data exchange. There was also increased collaboration between organizations such as Plattform Industrie 4.0 and the Industrial Internet Consortium, with Bosch an active leader in both. Alliances became an integral part of Industry 4.0.
And today? Interest is still high, but too few companies are consistently gearing up for Industry 4.0: “Pilot projects are a good approach for trying things out and getting ideas out there. Now it’s time to up the tempo: we need to make Industry 4.0 the norm,” Najork says. Bosch uses its own academies and training courses to train associates for Industry 4.0 and also makes this offering available to customers. Najork is convinced that “Industry 4.0 is not an end in itself. It’s a way to maintain competitiveness. In the future, nothing will be possible without digitalization.”
Bosch projects deliver measurable benefit: connected solutions increase productivity by as much as 25 percent, boost machine availability by up to 15 percent, and reduce maintenance costs by as much as 25 percent. “If we want to exploit the potential of Industry 4.0, we have to move away from isolated solutions. Technical systems that work only within their own boundaries inhibit progress,” Najork says.
In Bosch plants, there are now over 120,000 machines and over 250,000 devices such as integrated cameras or robots connected. Some 22,000 machine controllers alone are connected via the Nexeed software for Industry 4.0 developed by Bosch Connected Industry. Founded in 2018, this operating unit has already supplied software to more than half of Bosch’s plants and more than 2,000 production lines. In addition, around 100 international customers rely on Nexeed — including BMW, Sick, and Trumpf. Hardware and software are growing ever closer together.
At Hannover Messe, Bosch Rexroth presented its ctrlX Automation platform. Based on app technology and web engineering, this open, 5G-enabled control technology enables co-creation. The idea behind it is for users to either use apps provided by Bosch Rexroth and third-party providers, or to develop apps themselves and share them with other companies within an ecosystem. “By making developments participatory,” Najork says, “we can create network effects and let ideas take wing.”
“Our focus is on harnessing and combining the power of different technologies. Bosch is becoming an AIoT company. We’re bringing artificial intelligence and the internet of things together,” Najork says.
www.boschrexroth-us.com
Cyient
Launches Series of Industry 4.0 Solutions
Cyient, a global engineering and digital technology solutions company, announced the launch of its INTELLICYIENT suite of Industry 4.0 solutions that will enable digital transformation for industries that draw significant value from their assets such as manufacturing, industrial, aerospace, automotive and off-highway, utilities, and mining and natural resources. INTELLICYIENT was launched by Anand Parameswaran, senior vice president and global business head, Cyient Digital, at Hannover Messe 2021—the Olympics of Technology—where Karthik Natarajan, chief operating officer and president, Cyient, delivered the keynote on Resilient Manufacturing.
Enterprises implementing Industry 4.0 stand to create an economic value of US$3.7 trillion by 2025. The Industry 4.0 spend is poised to grow at over 20% and systems integration, application development, and data services are expected to be the key technology focus areas.
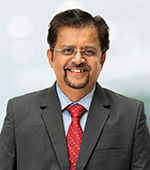
The most successful Industry 4.0 solutions will be the ones that bring domain knowledge, depth of technological expertise, and engineering excellence and understanding of business operations. These have been the unique strengths of Cyient, which makes it a partner of choice across its Fortune 500 customers globally.
“Cyient has leveraged its investments in the latest digital technology capabilities, and its three decades of experience in engineering and geospatial offerings for asset-intensive industries to design its INTELLICYIENT solution portfolio,” said Parameswaran. “With six digital solutions, powered by the interplay of nine technology studios, and our strong partner ecosystem, INTELLICYIENT will help enterprises globally achieve the full potential of digital transformation with IT-OT convergence. We aim to focus on the four key themes of smart automation, intelligent supply chain, end-to-end visibility of workflows and assets, and next-gen workforce solutions that are driving Industry 4.0 adoption.”
Akshat Vaid, vice president, Everest Group, who moderated a panel discussion on digital transformation, said, “Digital engineering has become all-pervasive, contributing over 23% to global ER&D spending. Within manufacturing, it manifests as Industry 4.0—the transformation of cyber and physical systems on the back of digital themes for enhanced visibility, control, and autonomy. Industry 4.0 investments have been rising steadily, and the COVID-19 crisis has provided an additional impetus as enterprises look to enhance manufacturing resilience. In effect, enterprises are no longer viewing this spend as discretionary but rather as an avenue for driving business resilience and competitiveness. They, however, struggle with a shortage of capabilities, organizational complexity, data integration, and speed of implementation when it comes to transformation-at-scale. This has led to a rise in outsourcing with third-party vendors offering services across consulting, development, integration, and management of existing deployments.”
To take on this growing opportunity, Cyient Digital, as a leading solutions and services provider, is scaling up its capabilities by investing in talent, solutions for specific use-cases, ecosystem partnerships, and the relevant infrastructure of labs and centers of excellence.
f.hubspotusercontent40.net/hubfs/5724847/2021/intellicyient/Intellicyient.mp4
Schaeffler
Named One of the 50 Sustainability and Climate Leaders by the U.N.
The Schaeffler Group has been selected as one of the 50 Sustainability & Climate Leaders worldwide on the occasion of the 75th anniversary of the United Nations (UN). The common objective of this initiative is the achievement of the 17 goals for sustainable development set by the United Nations.
“For us, the appointment of the Schaeffler Group by the UN as one of the Sustainability & Climate Leaders is not just recognition of the work we have done to date, but both an incentive and an obligation to continue implementing our sustainability strategy with the utmost consistency,” said Klaus Rosenfeld, chief executive officer of Schaeffler AG. “As part of this impressive initiative, we will do everything in our power to realize our sustainability and climate targets and thus make our contribution to achieving the 17 sustainability goals of the United Nations.”
A prerequisite for the admission into the 50 Sustainability & Climate Leaders is a clearly defined sustainability strategy and corresponding corporate objectives. As a corporate value, sustainability has been firmly anchored in the Schaeffler Group’s activities for many years and is an integral component of the corporate strategy. “Sustainable corporate success to us means assuming ecological and social responsibility — in production, through the use of our products, and with the involvement of our suppliers,” said Corinna Schittenhelm, member of the board of managing directors of Schaeffler AG with responsibility for HR and sustainability.
Schaeffler was convincing in the selection process and now represents the automotive and industrial supplier sector in the DACH region (Germany, Austria, Switzerland). For the Schaeffler Group, it is not only the ecological footprint of its own production facilities that plays a major role. The development and production of technologies for the optimal use of renewable energies is also an important contribution to climate protection. Schaeffler’s components, systems, and service solutions make specific contributions to sustainable changes in a wide range of industries — for example, in the electrification of the powertrain for vehicles or in the manufacturing of large-sized bearings for wind turbines.
www.schaeffler-sustainability-report.com
AD
Secures Third Consecutive Top Workplace Award
For a third straight year, AD has been recognized as a Top Workplace in the greater Philadelphia region based on feedback from its annual employee engagement survey. The anonymous survey uniquely measures drivers of engaged cultures that are critical to the success of any organization, including how well employees are aligned with company goals and objectives, feel they belong and are valued, get support and attention from their manager, and believe the organization operates effectively. AD partners with employee engagement technology partner Energage, LLC to administer the survey.
“Earning this distinction is deeply meaningful, and even more so in a pandemic year that brought added stresses, uncertainty and distance between us,” said AD’s Chairman and CEO Bill Weisberg. “Achieving three straight years of this award is only possible because our executive committee, leadership team, HR team, managers, associates, and Great Place to Work Committee are all dedicated to constantly improving and learning from one another.” Weisberg points to The AD Way as a major driver of the company’s award-winning culture.
“Practicing our 34 fundamentals, the foundational behaviors that guide our interactions, creates a healthy environment that allows us to attract and retain amazing talent, and deliver unparalleled service to the organization’s community of members and supplier partners,” Weisberg said. “Our associates put in the extra effort.”
Senior Vice President Neil Cohen, who leads AD’s HR effort, said, “This award is special because it’s based purely on our associates’ feedback. It’s a strong signal that they are engaged, willing to share their perspectives, and have skin in the game to help us celebrate our strengths and make continuous improvements.”
Energage CEO Eric Rubino shared his thoughts on the value of the feedback. “When you give your employees a voice, you come together to navigate challenges and shape your path forward. Top workplaces draw on real-time insights into what works best for their organization, so they can make informed decisions that have a positive impact on their people and their business.”
www.adhq.com
VELO3D
Adds Krause to Board of Directors as Audit Committee Chair
VELO3D Inc. has announced the appointment of renowned business leader Stefan Krause to the company’s board of directors as audit committee chair.
With more than 30 years of experience working at some of the most recognizable and successful companies in the world, Krause has built a singular career that previously included a chief financial officer (CFO) role at BMW — where he was the youngest ever to hold the position and a member of the management board. Krause then took on a similar role at Deutsche Bank, earning himself a reputation as one of the world’s top CFOs. He also previously served as chairman of Rolls Royce Motorcars, Postbank AG and BHF Bank. He has been in the supervisory boards of Rocket Internet and Allianz AG.
Krause has also been involved with multiple startups during his career and has been CEO and co-founder of electric vehicle maker Canoo.
“Stefan’s international business background, his expertise in branding and go-to-market strategy and his deep experience managing public companies make him a welcome and valuable addition to our board as VELO3D prepares for life as a public company,” said Benny Buller, founder and CEO, VELO3D. “His presence will help VELO3D continue our accelerated growth at scale and speed adoption of our full-stack metal AM solution, freeing the most imaginative engineers on the planet to build the impossible.”
Last month VELO3D announced plans to merge with JAWS Spitfire Acquisition Corporation and become a public company.
The company also previously announced a U.S.-wide distribution partnership with GoEngineer, and has said it plans to expand commercial operations in Europe, while establishing strategic partnerships in both Europe and Asia, demonstrating the company’s focus on supporting visionary aviation, energy, space and industrial customers all over the world. Current customers include Chromalloy, Honeywell, Lam Research, and Primus Aerospace.
“With truly unique capabilities setting it apart from others in the AM space, VELO3D is actually delivering on 3D printing’s previously unfulfilled promise of innovation and design freedom,” said Krause. “This is due to a relentless focus on pushing the limits of manufacturing technology and helping customers design and build the parts they need without compromise. I’m looking forward to working with Benny and the team to help companies become more agile and innovate faster.”
www.velo3d.com
Nordex
Receives AS9100D and ISO 9001:2015 Accreditation
Nordex growing strong over three generations
Nordex, Inc. recently announced the establishment of a quality management system for AS9100D & ISO 9001:2015. The company is involved in the manufacture, distribution, assembly and refurbishing of catalog and non-standard high precision mechanical/electro-mechanical components and assemblies such as bearings, couplings, gears, ball slides, enclosed geartrains and related instrument grade power transmission components and assemblies for medical laboratory and industrial analytical instruments, factory automation, semiconductor and aerospace OEMs.
“Nordex has been in business for more than 60 years. We have accomplished this through continuously striving to improve our business so we can better serve our customers. AS9100D certification helps Nordex to be a better company, through improving our quality processes and reducing our costs—this helps us to provide more value to our customers and ensures we always deliver the high-quality products they have come to expect,” said Dan Agius Jr., CFO and part-owner of Nordex, Inc.
It’s not just the quality department that has been improved by AS9100 certification, but Nordex’s entire manufacturing operations, according to Agius.
“Through our heightened quality procedures, we are running more efficiently and finding and correcting potential problems very early on in our manufacturing process. Obtaining AS9100D certification has helped provide us with the tools to do this by developing improved risk mitigation strategies. This helps us to meet and exceed our customer’s needs when it comes to quality and on-time delivery,” he added.
With the evolution of the power transmission industry, Nordex has been able to thrive thanks in part to quality control procedures that have helped the organization to better adopt and utilize cutting-edge power transmission technologies.
Agius believes the company will continue this approach in the future.
“We need to consistently update our quality requirements so we can keep meeting our customers’ needs as their businesses are ever changing. AS9100D is a quality framework that gives us the tools to keep building out our quality systems and standards, however necessary, well into the future.
Nordex.com
STLE
Announces Ken Hope as 2021–2022 President
The Society of Tribologists and Lubrication Engineers (STLE) — the technical society serving individuals, companies and organizations that comprise the tribology and lubrication engineering business sector — recently announced that Ken Hope, Ph.D., global PAO technical services manager, for Chevron Phillips Chemical in The Woodlands, Texas, will assume the role of 2021–2022 president for a one-year term beginning May 18.
In his new role, Hope will serve as the principal executive officer of the society and as chairman of its board of directors. Hope served on the STLE Board of Directors from 2006 to 2017 and in 2018 became a member of STLE’s Executive Committee, serving one-year terms as treasurer, secretary and vice president.
Joining him on the STLE Executive Committee are Vice President Ryan Evans, Ph.D. (The Timken Company), Secretary Hong Liang, Ph.D. (Texas A&M University), Treasurer Jack McKenna, (Sea-Land Chemical Company), Immediate Past President Paul Hetherington (Petro-Canada Lubricants Inc.) and STLE Executive Director Edward P. Salek.
www.stle.org
Manus Award
Honors Creative Use of Plain Bearings
For the first time, the manus award, a joint initiative by Igus, a motion plastics specialist, recognizes four contestants. The prize showcases fascinating, creative uses of plain bearings. The tenth gold manus award goes to Kässbohrer Geländefahrzeug AG for its PowerBully. Silver goes to a radio-controlled, battery-driven felling wedge. Bronze goes to a sun protection facade system with a shape memory alloy. The first-ever green manus was awarded for a sustainable project. It went to an intelligent solar-powered rubbish bin from Finland.
Gold for a German carrier vehicle
The gold manus award and 5,000 euros prize money went to Kässbohrer Geländefahrzeug AG for its PowerBully. The PowerBully is an all-terrain carrier vehicle with large payloads for a variety of applications. It is used wherever roller-driven vehicles cannot go. Given the appropriate superstructures, the PowerBully can, for instance, be used to lay power and telephone lines, fight fires, analyse soil, or perform mulching work. All of its components must be extremely robust and able to handle great forces, as must the plain bearings used in the floating axle and the tensioning axle. The design engineers consulted igus and chose wound XXL iglidur TX1 plain bearings. They are lubrication-free and insensitive to dust and dirt. This is an extreme-conditions application, which also convinced the judges.
Silver for a radio-controlled, battery-driven felling wedge
The silver manus went to Forstreich GmbH, a German company. The last few dry years have made it increasingly dangerous to fell trees with a hammer and wedge. So, Stefan Reichenbach has developed a radio-controlled, battery-driven felling wedge. The forester places the wedge in the saw cut and starts the felling process, maintaining a safety distance. The design engineers used drylin W double rails with polymer pillow blocks for the felling wedge’s linear movements. They also used iglidur G plain bearings. The components allow the wedge to absorb radial forces over a long service life – even in environments with dirt, sand and wood chips.
Bronze for a sun protection facade system
Third place went to the French company Arcora for a sun protection facade system with a shape memory alloy. When the alloy heats up, the system can set a translational carriage in motion. This carriage transfers the force to the rotating sun protection fins via small connecting rods. This allows standard motorisations in building facades to be replaced. At the interfaces between moving and fixed elements, the design engineers used Igus high-performance polymers, including igubal spherical bearings, iglidur J polymer fixed flange bearings and drylin N miniature guide rails.
Sustainability prize for an intelligent rubbish bin
This year saw the first green manus, which is awarded for using polymer plain bearings in especially sustainable projects. The award went to Finbin, a Finnish company, for developing an intelligent, solar-powered rubbish bin. The patented technology in the waste system ensures that the waste is compressed at a ratio of 6:1. The rubbish bin autonomously notifies the waste management system of its fill level. It is of primary importance that all bin components be long-lasting and maintenance-free. That is why plain bearings made of the iglidur G tribo-polymer are used in the clamping rods for the hatch, pedal and pedal transmission rods. The bearings work without external lubricants and are insensitive to dust and dirt.
www.igus.eu/manus