Premier Hydraulics produces standard hydraulic fittings, valves, manifolds, hose connectors, and flanges in large quantities. In addition, the company specializes in custom-engineered products, meaning it can create assemblies or sub-assemblies with combined components.
“OEMs today want quality parts at a competitive price that are delivered on time. Beyond that, many also want value-added services like expert engineering, design support, and the ability to provide custom parts such as manifolds, flanges, valves, and fittings in various materials. Depending on how it is designed, the custom component can become a part of a kit, sub-assembly, or assembly of complete product,” said Dinitrise Hicks, sales manager, Premier Hydraulics, Farrell, PA.
According to Hicks, OEMs often request custom parts, such as hydraulic fittings, that vary from SAE standards in size, thread size, pitch, or materials. Custom parts may also be necessary if OEMs require a unique part function or part combination.
According to Hicks, a common question asked by OEMs of their parts manufacturers is, “Can you make this part?” Often behind this question is an OEM’s perception that the parts vendor can only work with one material or provide limited or no value-added services.
To meet OEM’s need for value-added custom parts, Premier Hydraulics dramatically expanded its capabilities after the company was acquired in late 2022 by PTR Group, a leading contract manufacturer of components and subassemblies.
PTR Group has embarked on a strategic campaign to acquire companies offering complementary parts manufacturing differentiated by material and product type to broaden the breadth of their overall parts portfolio. As a result of their acquisition strategy, PTR Group now offers OEMs a wide range of parts, including metal components and subassemblies. They can also custom manufacture precision thermoplastic injection mold tooling, zinc die-cast mold tooling, and molded plastic components.
Within each of these areas, PTR Group can offer OEMs a range of complementary value-added parts and services that go beyond just manufacturing. This includes in-house part and tool design, tool build, complex assembly, and testing.
These acquisitions indicate the imperative to enhance manufacturing operations, thus maintaining competitiveness in the global fluid power, hydraulics, and pneumatics markets. (Information provided by Del Williams, technical writer, Torrance, CA.)
ptrgroup-mfg.com
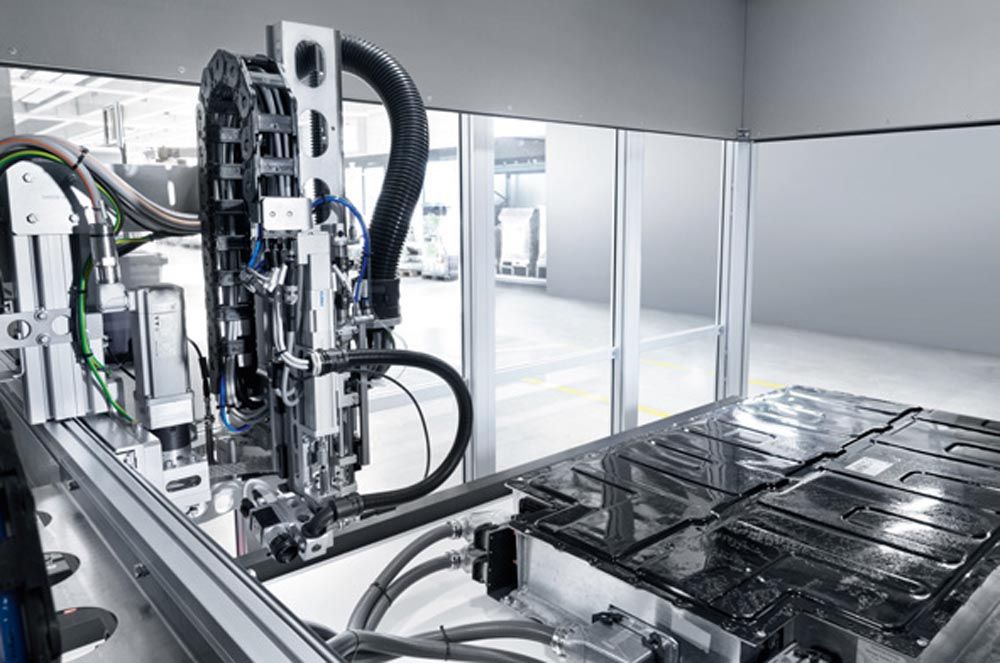
HAHN Automation Group utilizes Festo’s electric and pneumatic technology to enhance the company’s e-mobility solutions.
3. E-Mobility and Electrification Solutions
Element—a global provider of testing, inspection, and certification services in London—is partnering with a major manufacturer to test EV battery cooling plates and their associated tubes, lines, and connectors. The manufacturer will receive reliable data that will help them to refine and rewrite internal procedures which primarily includes thermal cycling and pressure pulsation. During these tests, coolant is circulated through the plates at varying temperatures and pressures while a range of environmental extremes, including external temperatures from -30°C to over 100°C are applied simultaneously. Element will also supply the manufacturer with data regarding the performance of the plates upon startup, as technicians evaluate flow characteristics of the coolant through the plates using typical flow rates at low temperatures.
In addition to their specialized battery cooling systems, hybrid and electric vehicles share some fluid systems with traditional internal combustion engines, including hydraulics systems for brakes, transmission and steering fluid systems, and cooling systems for radiators. The components of an EV differ from those of an internal combustion vehicle; EVs also tend to be significantly heavier and have a different weight distribution. This can affect the functionality of other fluid systems in the vehicle, such as hydraulic steering and brake systems, requiring that those systems be redesigned. For many vehicles, especially novel vehicles, full vehicle lab testing is required to understand how systems affect one another, and how this might impact handling, safety, and longevity.
Additionally, electric vehicle manufacturers depend on the safe and flawless functioning of batteries. HAHN Automation Group has therefore developed a battery tester that carries out a complete test of the mobile energy storage units fully automatically. This innovation includes a 3-axis gantry for optical and leak tests, consisting of electric drives from Festo,
The HAHN Battery EOLT is a complete solution for testing battery packs. All relevant test scenarios for 90 percent of all battery packs available on the market can be implemented on the end-of-line test system because the system can be easily scaled to many sizes. HAHN Automation Group offers everything from a single source: from power electronics and test equipment to test software and automation.
“Thanks to its vast expertise in testing technology, the company helps define the best test strategies to optimize cycle times and ensure the targeted product quality,” said Christian Bubat, global business development manager at HAHN Automation Group. The company worked with the Production Engineering of E-Mobility Components (PEM) chair at RWTH Aachen University on the development.
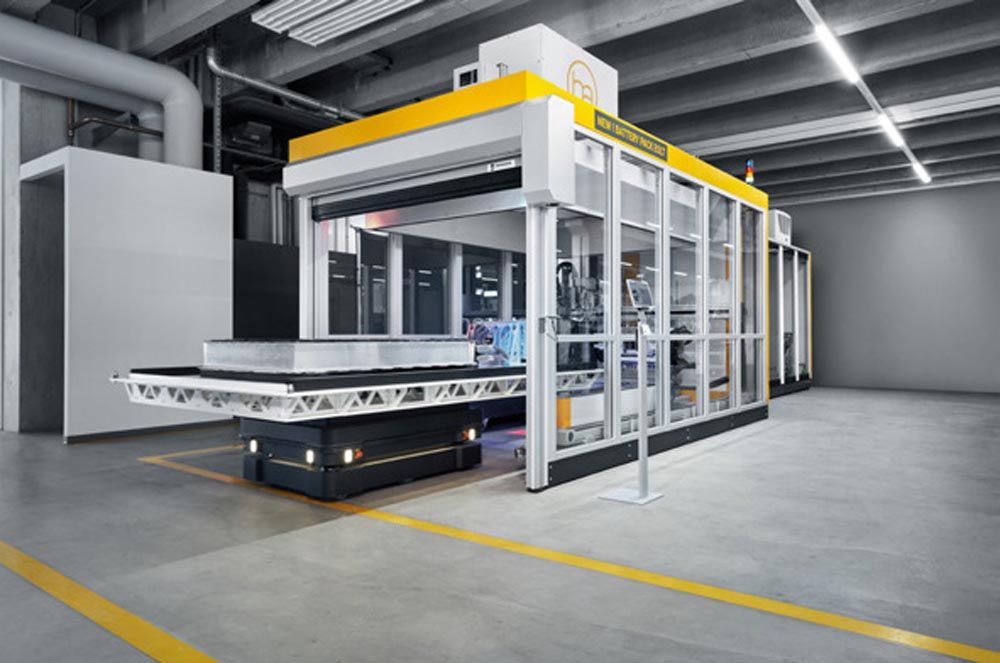
HAHN Automation Group has developed a battery tester that carries out a complete test of the mobile energy storage units fully automatically.
How exactly does the testing work? The axis gantry moves and positions two sensors along all edges of the battery pack to detect any leaks from the battery housing and cooling unit. The camera checks that all plates and stickers are fitted correctly and that the battery pack is processed properly and detects any mechanical damage. A battery management system test checks the communication and evaluates the sensors.
“As in many previous automation projects, it has been proven that Festo is the right, globally reliable partner in electric and pneumatic automation technology,” added HAHN’s Head of Development, Martin Sulzbacher.
Thanks to the long-standing partnership, they have been familiar with Festo’s automation products for a long time and can use them in a precise and specific way. With online product finders, intelligent engineering software and engineering tools, HAHN Automation Group designers can find the right products for the development of new machines and systems reliably, quickly and without time-consuming calculations.
hahnautomation.com
4. Scalable IIoT Solutions
Festo and Siemens announced their latest partnership at last year’s Hannover Messe. Festo joined Siemens Industrial Edge Ecosystem where customers can purchase numerous apps from different providers. The integrated IoT solutions based on these apps offer customers greater productivity, flexibility, and sustainability.
Siemens launched the independent, cross-vendor app store for industrial customers in October 2021. This marketplace is based on the Siemens Industrial Edge platform. It uses edge computing to process data right at its source, such as on an industrial PC in machines or plants. Festo is offering data-driven AI solutions from the Festo Automation Experience (Festo AX) portfolio on the marketplace.
“This gives Festo an additional sales channel for industrial customers in the areas of mechanical engineering and production,” said Oliver Niese, digital business at Festo. “Users benefit from the opportunity to purchase apps from different providers in a single place, to install them and run them at the machines on the shop floor.”
Another customer benefit is the wide range of software components that can be integrated into production in a standardized way. IoT solutions can even be scaled across lines and factories, thus considerably reducing manual software maintenance.
“At Siemens, we want to add even more partners to the Industrial Edge Ecosystem, especially those in the field of automation,” said Rainer Brehm, CEO of factory automation at Siemens. “A larger selection increases flexibility for our customers, who can build individual IoT solutions from Siemens and partner modules (Industrial Edge apps and devices). We create the greatest value for our customers when we work together across company boundaries.”
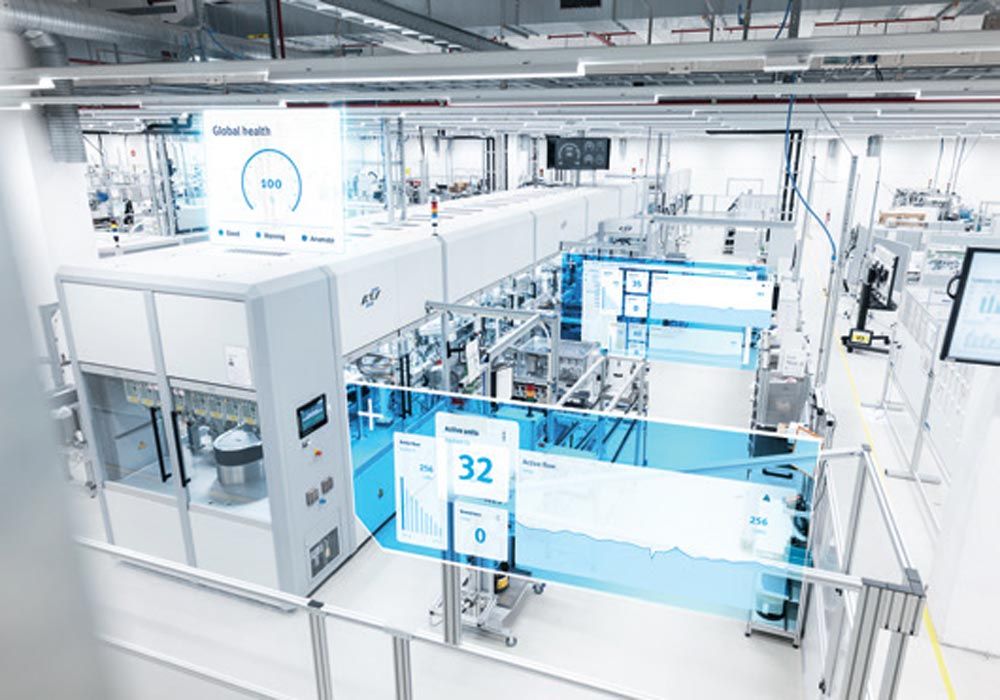
Festo AX provides a blueprint to increase productivity, reduce energy costs, prevent quality losses, optimize the factory floor, and create new business models. Photo courtesy of Festo.
Festo launched its Industrial Intelligence portfolio with the Festo AX Data Access connectivity solution, which feeds data from Festo components into Siemens Industrial Edge to supply analysis applications with data. Customers can build a monitoring solution based on the data and thereby improve maintenance processes, lower their energy consumption, and improve quality. Additional industrial apps from Festo are expected to be available on Siemens Industrial Edge, such as AI-based wear prediction for pneumatic drives.
Festo AX Industrial apps like AX Data Access are building blocks that can be combined with other applications from Festo, Siemens, and third parties to form larger solutions. They enable production employees to independently build digital solutions for optimizing productivity. The partnership allows Festo and Siemens to support their customers on the path to becoming more sustainable, more flexible, and highly efficient.
festo.com