The Importance of Safety in the Mining Industry
Regal Rexnord examines operational efficiency of braking systems
The rugged, high-stakes environment of the mining industry requires safety to be non-optional. Every piece of equipment, every process, and every decision must come together to ensure the livelihood of the workforce is preserved and operational excellence is achieved.
From conveyor systems to hoists and grinding mills, these critical components play a large part in providing essential raw materials to the global economy. One crucial element that plays a vital role in all these sectors, however, is the braking systems of these heavy applications.
The Critical Role of Brakes in Mine Safety
Brakes are a fundamental component in various mining applications, playing a crucial role in ensuring the safety of operations. Some key examples of how brakes are properly utilized within the industry include:
- Conveyors: Conveyor systems are used to transport materials over long distances within a mine. Brakes are essential for controlling the speed of conveyor belts, preventing overloading and mechanical failures that could lead to accidents. Effective braking systems ensure that conveyors can be stopped quickly in emergencies, reducing the risk of injury to workers.
- Hoists: Hoists are used to lift and lower materials and personnel in mines. Reliable braking systems are critical for hoists to prevent uncontrolled descent, which could result in severe accidents. Advanced braking technologies, such as fail-safe braking systems, ensure that hoists can stop safely even in the event of a power failure.
- Grinding Mills: Grinding mills are used to crush and grind ore into smaller particles. Brakes are vital for controlling the rotational speed of the mills, ensuring safe operation. In case of an emergency, brakes can quickly stop the mills, preventing potential hazards such as mechanical failures.
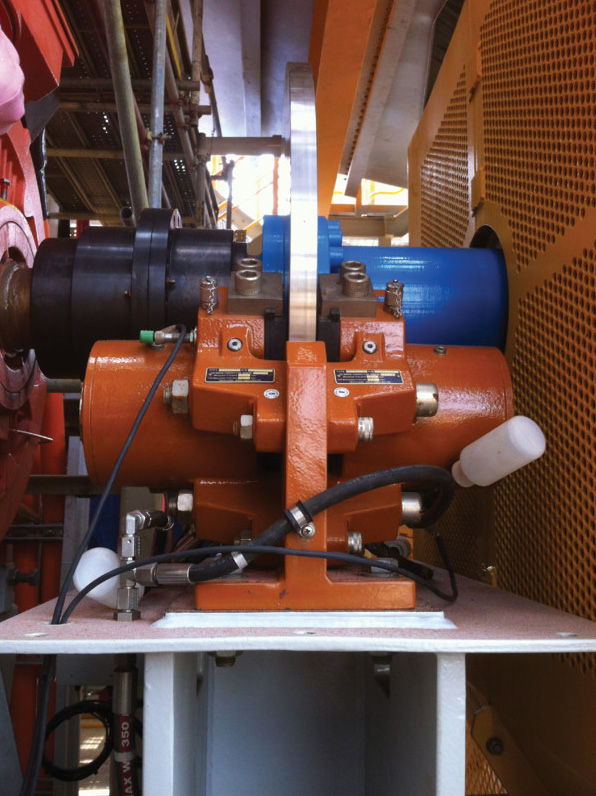
Application Considerations and Technological Advancements
There are many factors reviewed when designing and selecting a braking system—the torque applied when braking, location and orientation of the equipment, and operating conditions to name a few. However, braking is not as simple and on or off; often it requires accurate speed modulation and contingencies for power loss, speed signal errors, or mechanical failures.
Innovations in smart braking technologies have aided significantly in managing increased demands, detecting and monitoring equipment wear and status, and responding to changes in system resource availability.
A good example of these safety features being considered can be seen in Regal Rexnord’s emphasis in advanced braking solutions from one of its brands, Svendborg Brakes. Innovative braking solutions incorporate features like hydraulic releases and soft braking, significantly reducing wear and tear while ensuring precise control. Having these systems installed and in mind ensure proactive steps are being taken to significantly reduce the chance of injury on the work site.