Advanced robotics, especially with Virtual Commissioning will handle these changes without harming everyday operations. Technologies like AI and ML will modernize manufacturing so tasks can be optimized through advanced robotics. Businesses can leverage Virtual Commissioning for identifying issues during simulations, facilitating early validation and achieve informed decision-making. Shifting development and planning processes to an earlier stage allows problems to surface in the simulated environment rather than on the shop floor.
“You can have one application that does it all, eliminating the need for any data translation. Every time you do a translation, there is the possibility of losing accuracy and fidelity in that data,” Garg said. “By using the same data, you are ensured and guaranteed—the analysis, design work, machining, production—all of it is working off the same data set enabling simulation to be done through the design process–Simulate early and simulate often. “By simulating the whole production line, we can identify defects and problems in the design to make necessary corrections before real production.” Garg added.
This also ensures that if you make any changes anywhere in your process, that change is accounted for along the entire process chain.
“It’s important and becomes a lot more seamless to use all the applications within the software suite,” Garg said. “Track any changes as well. This is the biggest value that we see today whether you’re designing a gearbox or an airplane. You need to have the ability to see the impact of changes. Siemens’ MES allows us to spread process improvements and eliminate legacy tools. The dual benefit helps improve product quality and process efficiency, while also reducing operational risk and setting the stage for future shared improvements.”
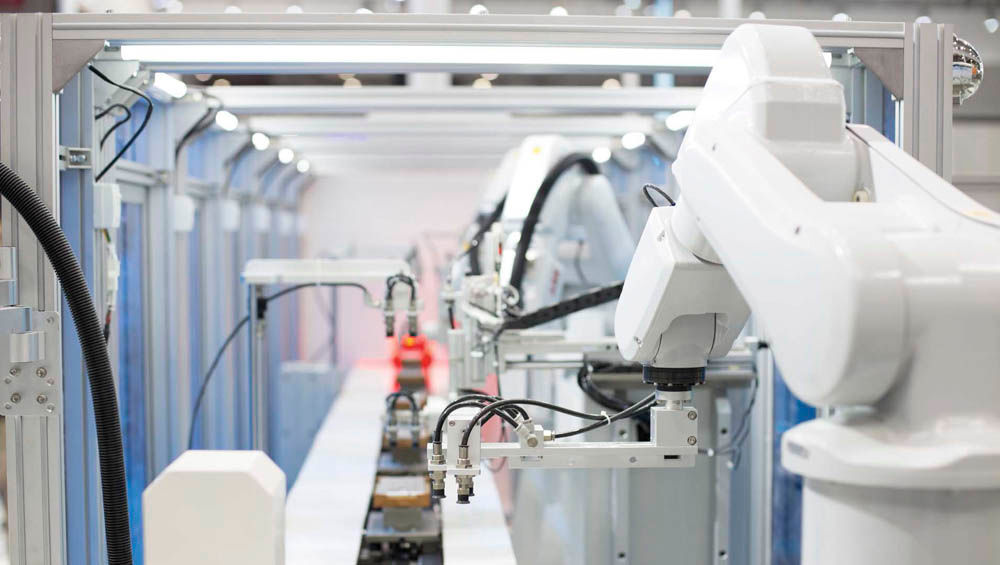
Simulate highly automated manufacturing processes in the digital twin before investing in expensive equipment. (Images courtesy of Siemens)
New Toys in the Toolbox
How would today’s mechanical engineer want to conceptualize the products that they’re trying to make—from the engineering phase to the manufacturing phase to the service, repair and maintenance? What’s the best way to make sure that you’re doing it in a sustainable way?
“For us, it’s like the whole cradle to grave process of a product. This is where Siemens PLM software really shines. I think there are two important things that are coming into picture, two core technologies that have become more relevant today. One is Generative AI, and then the second is the Industrial Metaverse,” Garg said.
Generative AI makes it very easy to leverage AI technologies to create and design new things without having the burden of starting from scratch, according to Garg. “It’s much easier to take a piece of paper and edit versus writing anything from scratch, right? This can have a huge impact in terms of innovation and the speed of innovation. The testing, the validity, the various ways to attack a project, etc., now this can all be done using Generative AI tools.”
The industrial metaverse is the concept of a digital world to mirror and simulate real machines and factories, buildings and cities, grids and transportation systems. By seamlessly integrating technologies like cloud and edge computing, industrial AI and digital twins, the industrial metaverse can optimize processes and drive sustainable practices, ultimately shaping the future beyond simulation.
The construction of the Industrial Metaverse relies on collaboration, openness, and strong ecosystems. Serving as a digital business platform, Siemens Xcelerator brings together a strong ecosystem of partners and offers solutions that work easier, faster, and at scale to use, helping customers to accelerate their digital transformation and enable the industrial metaverse.
Siemens Industrial Copilot opens the language models and gives engineers the ability to have human-like conversations with the equipment. Garg said the Siemens Industrial Copilot gives designers real-time access to non-proprietary information (manuals or guides, for example), proprietary product information and those language models.
“We’re giving our customers the ability to access all three pieces of information through Siemens Industrial Copilot. If someone has made a new design in Brazil, they can share it in real time with the company or share it with customers around the world,” Garg said. “Someone said it took the internet 20 years to become pervasive. I think it was on a podcast with the CIO from Google. Many believe Generative AI is going to do the same thing in five years’ time. Keep an eye on the pace in the coming months, it’s going to explode at a mind-boggling rate!”
At the show, Siemens also unveiled its collaboration with Sony’s XR technology. Sony’s XR head-mounted display is a fundamental part of the forthcoming NX Immersive Designer, an integrated solution that combines Siemens’ NX, exclusively with Sony’s breakthrough XR technology to deliver immersive design and collaborative product engineering capabilities. The head-mounted display and dedicated controllers let designers create more intuitively in a fully immersive environment, allowing you to move freely between the virtual and real worlds. It will allow designers to play around in the virtual environment without ever having to build a physical prototype. Siemens’ NX Immersive Designer is expected to launch at the end of 2024.
“Lastly, we are looking at new ways to make our more accessible. Through a token-based approach and subscription models, small- and medium-size enterprises can now have easy access to applications that in the past were only in the reach of larger enterprises. “Instead of investing in a large upfront payment or managing a large IT system to support the software, there are many other options available. Now you can pay as you go, you can leave the application support to Siemens. There is much more flexibility,” Garg added.
As a society, we take for granted how quickly technology is changing. Manufacturing production can slim down from months to weeks to days—even hours in certain circumstances. We can build things faster and more efficiently thanks to these new software tools.
Siemens Xcelerator is a comprehensive, integrated portfolio of software and services. It is designed to form a software foundation for digital business transformation—helping companies accelerate their evolution into digital enterprises, enabling them to be poised for ongoing success.
The factory of the future will allow designers to test, research and validate hundreds of “what-if scenarios” in real-time. They will no longer feel the restraints from budgets, time or resources. Creativity and innovation will play as big a role as the design execution itself in areas such as energy, e-mobility, packaging and aerospace.
sw.siemens.com