The above factors are extremely important for lubricants within the dredging industry. Furthermore, in an industry where vessels are utilized all year round in extreme environments, the need for functioning equipment is imperative. Margear offers customers economic benefits due to the extremely long oil-change intervals resulting in reduced downtime and maintenance costs.
Environmentally Certified and OEM Approved
Panolin Margear offers antiwear and anticorrosion properties, and has been successfully used in a variety of applications including, but not limited to:
- Gearboxes
- Roller Bearings
- Propulsion systems including bow thrusters, Azipod thrusters, azimuth thrusters
- CPPs
panolin.com
Klüber on the Way to a Clean Future in Shipping
Between 2006 and 2013, Klüber Lubrication developed EALs for stern tubes (Klüberbio RM 2 series) and thrusters (gear oils, Klüberbio EG 2 series) based on ester-oil technology. Both oil series are benchmarks for ester oil-based EALs and gained approvals from all leading propeller equipment and thruster manufacturers.
Klüber Lubrication was one of the first lubricant makers to conduct research and development in the field of readily biodegradable lubricants that are nontoxic and meet the tribological performance for lubrication of propeller shafts and thrusters.
The Problem with EALs Under High LoadsFor the lubrication of the propeller shaft running in the stern tube and propeller shaft seals, the VIDA stipulates the use of EALs for the protection of the environment as an escape of oil into the sea through the propeller seal cannot be completely prevented. Biodegradable lubricants for stern-tube application from several suppliers have been available for nearly two decades. So far, however, no one has succeeded in offering an EAL with a performance capacity equaling that of a mineral oil-based product in all important performance criteria such as a strong lubricating oil film, consistency in the presence of water in the oil, and excellent seal compatibility.
Why can an insufficiently strong oil film be a problem? Under particularly high loads, for example during voyages with partially immersed propellers or at hard maneuverings, insufficient strength of a lubricant film can lead to metal-on-metal contact and higher journal bearing temperatures eventually causing bearing damage. Many commercially available EALs show insufficient resistance to oxidation and hydrolysis as well as poor lubricating capacity under high loads. Excessive shear loads may cause them to lose their viscosity and hence their ability to form a load-bearing lubricant film. High oxidation and aging can cause their viscosity to increase in an undesirable way. Chemical processes and the presence of water tend to decompose the lubricant. A failure of components and possibly even a breakdown of the propulsion system are possible. Frequent oil changes are therefore inevitable with some commercially available EALs, leading to additional operating costs.
An additional challenge in propeller shaft lubrication is that not only does lubricant leak into the water, but vice versa: The lubricant becomes contaminated with water via the same path. The insufficient resistance to hydrolysis of most commercially available ester oil–based EALs results in a rising TAN (Total Acid Number), leading to an unscheduled complete or partial oil change and a shorter service life of the seal in the stern tube. The only way to prevent early oil changes due to a rising TAN has so far been the installation of expensive filter systems and oil dryers. This, however, constitutes a major investment and increases complexity on board.
Eco-Compatibility vs. Performance
The objective of developing Klüberbio RM 8-100 was to obtain a stern tube oil that is not susceptible to hydrolysis, extends service life in comparison to conventional EALs, and meets all sustainability requirements of the EU Ecolabel and the former VPG and current VIDA for operation of ships in the United States. Besides biological eco-compatibility, the new product was designed to achieve excellent performance in terms of compatibility with seals, shear stability, wear behavior, corrosion protection, and friction. While the lubricant films formed by some EALs found in the market are not thick enough to prevent damage to stern tube bearings under unfavorable load conditions, the new product is designed to build up a load-bearing film that is close to that of a mineral oil–based product.
Next Generation of EAL Lubricants
The newly developed Klüberbio RM 8-100 successfully meets maximum environmental as well as performance requirements. Klüberbio RM 8-100 generates a lubricant film of excellent thickness that persists even under high edge loads in the propeller shaft bearing. Due to this lubricant film, the propeller bearing, and the shaft remain separated and overheating of, or damage to, the bearing is prevented. Klüberbio RM 8-100 shows very good compatibility with the elastomer material in the propeller shaft seal, providing it with optimal lubrication. This ensures a long service life and full function of the components.
Regarding TAN and resistance to hydrolysis, the new product’s performance ratings are multiples of those of ester-based EAL stern tube oils—almost up to the standard of mineral oil-based lubricants. This means the oil’s chemical composition prevents it from reacting with water getting into the stern tube through the elastomer seal. The TAN hardly rises, leading to a significantly longer life expectancy for both the propeller shaft seal and the oil.
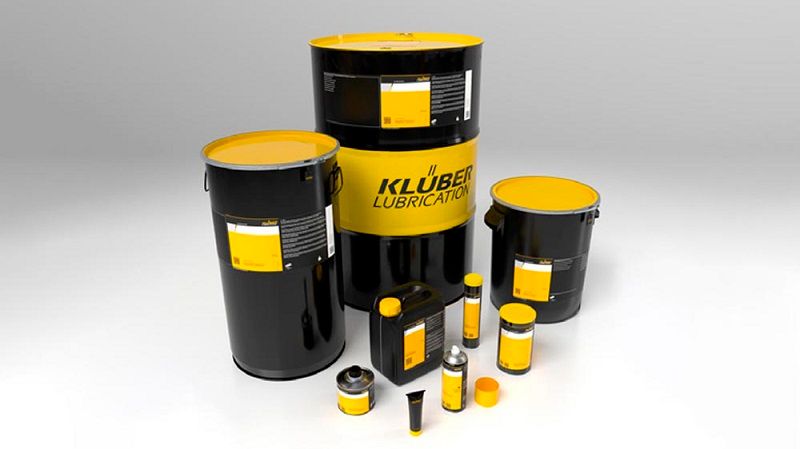
Klüberbio RM 8-100 is the first lubricant based on a new technology Klüber Lubrication will adopt into its range of EAL gear oils designed for tunnel and azimuthing thrusters.
Two Worlds Come Together
Klüber Lubrication already showed in the past that bio in a lubricant no longer stands for a compromise of a product being green but having weaker technical performance. With the new generation of Klüberbio stern tube and gear oils, Klüber provides excellent lubricant performance, often considerably better than the direct mineral oil–based competition, and the products are also biodegradable and nontoxic.
With Klüberbio RM 8-100, users obtain a technology-leading product meeting legal environmental requirements and offering at the same time the extremely good performance ratings of a conventional, mineral oil–based lubricant. This is important for international shipping operations, where sustainable approaches are increasingly required.
klueber.com
Sidebars:
Advantages of EALs Over ECLs
1. Environmental Accountability: EALs are backed by a clear definition and regulatory framework, making their environmental benefits more transparent and dependable.
2. Ecosystem Protection: EALs’s biodegradability and nonbioaccumulative properties contribute to the protection of aquatic ecosystems. Their use aligns with global efforts to reduce pollution and maintain biodiversity.
3. Regulatory Compliance: Mandatory usage of EALs in certain regions ensures that industries are actively contributing to environmental protection.
4. Enhanced Performance: EALs are developed to match or surpass the performance of conventional lubricants, dispelling the notion that eco-friendly options compromise functionality.
5. Innovation Incentive: Regulatory demands for EALs have spurred lubricant manufacturers to innovate and develop high-performing, sustainable products.
The Role of the Stern Tube
All types of vessels, whether container ships, bulk carriers, harbor tugs, or cruise liners, have one thing in common: propulsion is by means of large propellers of varying design. With few exceptions, the shafts of fixed-pitch and controllable-pitch propellers run in journal bearings mounted inside the stern tube filled with oil. The radial movements of the propeller shaft in the bearing are larger than those of other industrial shafts and may be intensified by the force of waves or vibrations.
Radial shaft seals or mechanical seals prevent the oil from leaking into the sea and keep the stern tube tight against the engine compartment. Thrusters are filled with gear oil and must be sealed at the propeller shaft as well as at the rotating steering shaft of azimuthing thrusters to prevent leakage into the water. It is, however, not possible to seal the stern tube or the thruster 100 percent tight against exiting oil.
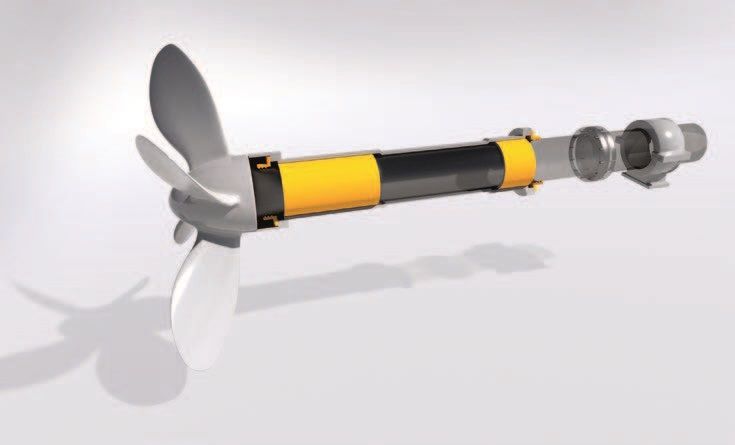