Modernizing Component Technology
Liebherr offers innovative solutions for heavy–duty applications
Between trade shows including MINExpo and CES 2025, we’ve been treated to a great deal of new technology in areas like mining, agriculture, construction and heavy industrial components. Liebherr has modified its component portfolio to include digital measurement, electrification and maintenance-free technologies. Liebherr’s component product segment offers advanced solutions for slewing bearings and slew drives that meet the rising demands across a variety of applications and industries. These components are future-ready and play a vital role in making operations much more efficient.
Slewing Bearings of the Future
Industries worldwide are under pressure to reduce their environmental footprint, while becoming more efficient, sustainable and safer. But how can these goals be achieved? Often, the answer lies in the hidden champions of heavy industry: slewing bearings and slew drives. These components are at the heart of machines in a wide range of applications, including excavators, cranes, tunnel boring machines, antennas, offshore cranes, bridges and wind turbines. To meet the growing demands, Liebherr focuses on continuous innovation. These advanced slewing bearings and slew drives are designed to seamlessly adapt to modern standards, making operations more efficient, safer and environmentally friendly.
Bearing clearance monitoring (BCM), for example, provides a digital solution for measuring wear in slewing bearings. Built-in sensors allow precise measurements of axial and radial wear without requiring technicians to perform manual checks in hard-to-reach areas. This does not only improve safety but also speeds up the monitoring process. Permanently installed sensors enable quick wear measurement via a web app, which can reduce downtime by up to 75 percent.
An upgrade to the BCM can be seamlessly integrated into the customers’ system without the need for additional measuring devices or gateways, reducing system complexity and allowing users to analyze measurement data within your own systems.
These slew drives can be powered electrically, offering clear advantages: They reduce noise emissions and do not require hydraulic oil, which prevents the risk of oil leaks. Electrically driven slew drives are ideal for applications where no hydraulic systems are used. They offer a clean solution, especially in sensitive environments. The electric motors are also highly adaptable and can be combined with various gears. Thanks to intermediate flanges, motors can be easily integrated and installed in a space-saving manner. Electrically powered slew drives excel in precise positioning tasks, as their power control allows for accurate movements.
Liebherr’s innovative solid lubrication, Lifinity, eliminates the need for regular relubrication. In this process, a heated polymer-oil mixture is introduced into the heated bearing. As it cools, it forms a stable layer that provides long-term lubrication for the bearing. A major advantage is the significant reduction in maintenance, as regular relubrication is no longer necessary, leading to considerable savings in operating costs and time. This increases productivity, as equipment requires less downtime for maintenance, thus extending the lifespan of machines and boosting overall operational efficiency. Lifinity also reduces the risk of corrosion, enhancing the longevity of the bearing. Conventional greases and oils can leak and pollute the environment, but with Lifinity, there’s no such risk. This technology also meets strict NSF/H1 standards, making it suitable for food-related environments.
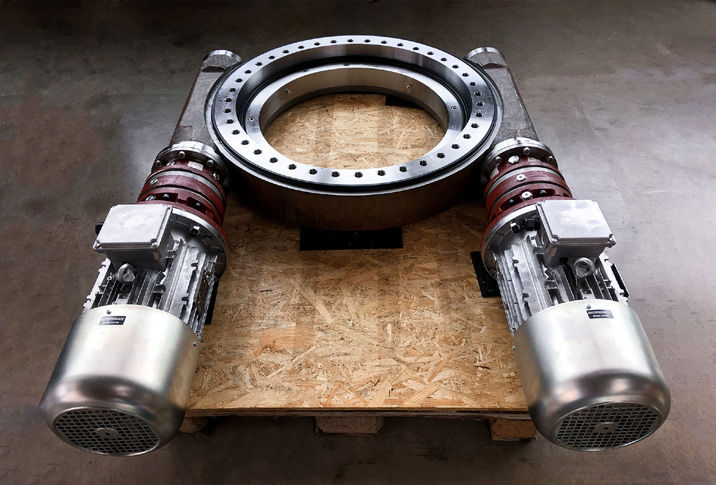