Extending Inverter-Motor Systems Service Life
Protecting electric drives from erosion caused by motor-bearing currents
More energy efficiency, higher performance and better controllability are the main reasons why more electric drive systems are being operated with frequency converters. However, these devices can cause high-frequency, asymmetrical interference currents, which, as a current passage through the output and fan-side bearings, can cause damage and premature failure.
Current-compensated CoolBlue toroidal cores made of Magnetec’s nanocrystalline material Nanoperm have proven to be effective protection against such conducted interference and its consequences. In addition, the Nanoperm Line Absorbers NaLA can also be used to significantly suppress symmetrical interference currents.
Together, these technologies offer optimal protection of inverter-motor systems against motor bearing damage caused by interference current, thus significantly increasing the availability and service life of electric drives in complex industrial applications including chemical, paper, rail, shipping, logistics, or energy generation with solar and wind power plants.
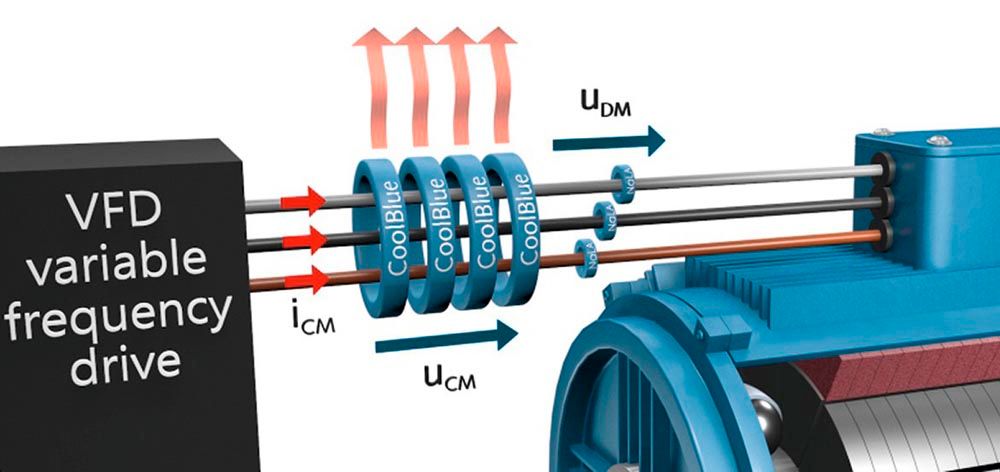
Current Passage Causes Electrical Erosion in Gearbox Bearings
The wiring of converter-motor systems is very often carried out exclusively with shielded three-phase cables. Although these can shield radiated interference of the three-phase AC voltage from other systems when connected in accordance with EMC, they do not completely protect against conducted interference. These result from over voltages caused by switching operations in the frequency converter. As asymmetrical interference currents in the range from about 300 kHz to 400 kHz, they flow from the frequency converter to the motor. Before they start their return journey via ground and earth, the interference currents in the motor from the stator and rotor are coupled via—almost like a capacitor. From there, they flow in the contact zone of the rotor and housing through the output- and fan-side bearings. This results in an electrical discharge from the inner ring via the balls to the outer ring, the energy of which leads to sparks and the formation of electric arcs. The high punctual thermal energy released in this process melts the bearing treads at the transition point. As a result, microcraters and loose particles of molten material are formed there. These delicate consequences of electrical erosion become visible under the microscope—without a microscope, a matte, greyish tread indicates the consequences of the passage of electricity. In further operation, washboard- or zebra-like, gray corrugations can be seen on the treads, which are the result of the melted out microcraters and particles. The course of damage in the gearbox is accompanied by the fact that the heat generated by sparks destroys the lubricant in the rolling bearing. The base oil burns, additives char—the lubricant decomposes rapidly. This turns dark—an unmistakable indicator of rapid aging, poor lubricity, and shortened service life.