Mechanical removal of weeds and debris avoids the use of threatening substances, but working in the water with hydraulic equipment poses a new set of challenges. These machines require essential fluids for transmitting power, lubricating the system, and dissipating heat. While there are many options available, most are not suitable for use in water. Mineral-based options are not biodegradable, cause long term pollution, and are toxic to aquatic life, so even a small leak, much less a blown hydraulic hose, can have disastrous effects on the environment. Plus, there are potentially high fines for these accidental discharges. Water-based fluids are a logical consideration, but they are only moderately biodegradable, must be replaced frequently, and they tend to wash away. They’re also better for low pressure systems and places that are not environmentally sensitive. To make matters even more complicated, regulations for chemical use in waterways become more stringent every year. In 2024, the Environmental Protection Agency (EPA) introduced the toughest clean water legislation so far, with stiff penalties for violators.
Weedoo realized that an environmentally friendly hydraulic fluid was in order. While researching the options, they found that not all eco-conscious choices are the same. Even though they are the same ISO weight, there are significant differences in oxidation process, resulting in critical variances in performance. Oxidation is a complex series of chain reactions common to most hydraulic fluids and consists of three stages: initiation, propagation, and termination. During the initiation phase, hydrocarbon molecules react with various catalysts, such as heat, pressure, or contaminants, which leads to the formation of free radicals (highly reactive molecules that combine to create new products). In propagation, the radicals keep the process going by reacting with oxygen, creating peroxides and other reactive species. Sometimes the byproducts from these reactions also act as propagators, speeding up the process even more. Many factors including high temperatures, moisture, metal contaminants, and agitation can also accelerate the oxidation process, leading to very rapid degradation. Consequences of oxidation include increased oil viscosity and organic acids; the formation of sludge, varnish and deposits; additive depletion (including anti-wear additives, dispersants, and corrosion inhibitors) and the loss of other vital performance properties. The termination phase occurs when stable, nonreactive products have formed, and oxidation has ended.
Hydraulic Fluids Exceed Expectations
Companies and government agencies that buy biobased anti-wear (AW) hydraulic fluids at the lowest bidding cost are assuming all biobased fluids (in the required ISO viscosity) perform the same, which is simply not true. Fortunately, Renewable Lubricants solves the problem with their patented, fully biodegradable options. A recent study conducted on seven brands of biobased hydraulic fluids demonstrated Renewable Lubricants’ remarkable performance in resisting oxidation. The ASTM D-2272 Rotary Pressure Vessel Oxidation Test (RPVOT) is a standardized method of comparing the oxidation life of lubricants in similar formulations. In the accelerated life-cycle testing format, all Renewable Lubricants lines significantly outperformed the other biobased and synthetic polyol ester (POE) based AW hydraulic fluids. The longer the time in minutes the greater the stability of the fluid. The US Steel requirement for anti-wear hydraulic fluid is greater than 120 minutes, which equates to 1800 hours of service life. While many brands do not achieve that minimum, every Renewable Lubricants formulation exceeded the requirement by more than double, with some products such as the Bio-Ultimax 2000 providing an impressive 650 minutes of product life (more than five-times the requirement). Bio-Fleet is particularly suitable for the demanding conditions encountered by Weedoo’s workboats, which operate in heat and water.
As Bobby O’Shields from Weedoo noted, “We use BioFleet ISO 46 in our machinery. The fact that it is 100 percent biodegradable makes it favorable for use with our Weedoo Boats, as we are running our equipment in fragile ecosystems.”
Superior fluid performance ensures reliable operation, maintaining hydraulic systems’ performance while minimizing environmental impact.
Bio-Fleet Hydraulic Fluids are environmentally accepted lubricants (EALs) that are formulated from renewable biobased resources. Ideal for both high-pressure and low-pressure hydraulic applications, they meet the Environmental Protection Agency (EPA) 2013 Vessel General Permit (VGP) guidelines for Environmentally Acceptable Lubricants (EALs). A direct replacement for mineral oil based hydraulic fluids, they should be used when low toxicity, biodegradability, and nonbioaccumulation properties are required. They exceed the acute toxicity (LC-50 / EC-50 >1000 ppm) criteria adopted by the U.S. Fish and Wildlife Service and the EPA. Because they meet the environmental requirements, they can also be used where ISO 15380 (HEES/HETG) Hydraulic Fluids are specified.
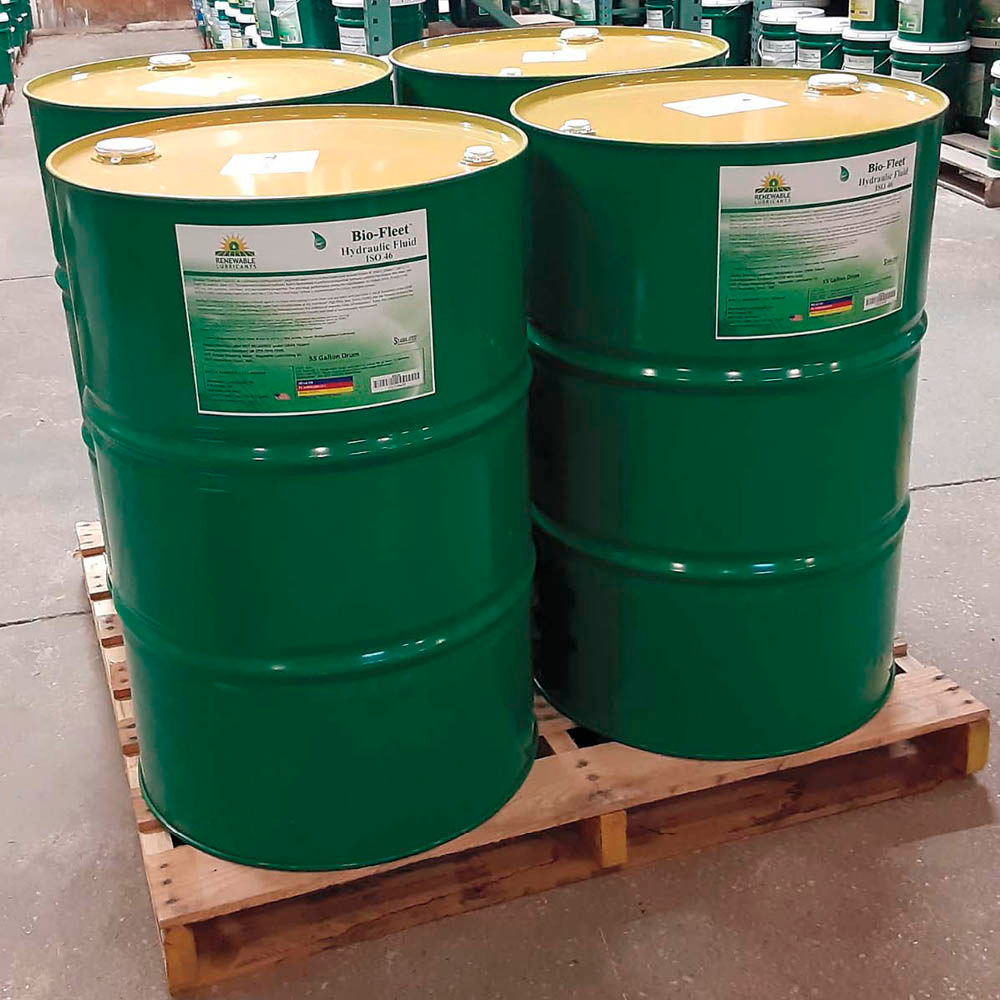
Bio-Fleet Hydraulic Fluids are formulated from renewable biobased resources and ideal for both high-pressure and low-pressure hydraulic applications.
Highly inhibited against moisture and rusting in both fresh and seawater, Bio-Fleet fluids passed both A and B Sequences of the ASTM D-665 Turbine Oil Rust Test, and they provide excellent water separation as shown in an ASTM D-1401 Demulsibility Test. With a higher viscosity index than synthetics, they provide improved thermal shear stability and increased load capacity, which translates to better performance and longer equipment life.
Green Alternatives Are
the Future
Intense OSHA monitoring and new regulations for water supply safety add increased urgency to eco-friendly business efforts. Transitioning to environmentally safe hydraulic fluids ahead of regulatory requirements has benefits for companies. In addition to ensuring compliance, companies can reduce the risk of operational disruptions or expensive fines. Minimizing environmental liabilities is a sound operational policy and demonstrates a commitment to sustainability. There are also financial incentives such as grants and tax breaks. By adopting these greener technologies now, companies can future-proof their operations, align with global sustainability goals, and gain a competitive edge in an increasingly eco-conscious market.