Bearing Mounting Arrangements
It seems like everyone is jumping into the electric gearbox market. Even Schaeffler is in the electric drive module (EDM) market now with their own 800v system. With all these new entries, some companies are satisfied with following traditional bearing arrangements while some want new and unique solutions or some combination of both. There is heavy debate over which styles are the best.
In this article, we will talk about the different types of 2-bearing arrangements for each shaft with the pros and cons of each for a simple three shaft, single speed parallel axis gearbox (ala Tesla style).
Let’s start with the classic fixed-float ball bearing design. This is a great, simple, almost one-size fits all approach to fixing 2 bearings on a shaft. One bearing is going to be your designated fixed bearing, which means it is going to take 100 percent of the axial loads plus a proportional part of the radial loads, depending on where the loads are coming from. To force the fixed bearing to take all the axial loads, it must be constrained on all four corners by shoulders, snap rings, retaining plates, screws, whatever your flavor is. The other bearing obviously takes none of the axial load and this is done simply by leaving a loose fit on the housing with no constraints. In all of our textbook examples, we will have a tight fit on the shaft. There are a couple of drawbacks to this system. Usually, snap rings or a retaining plate is needed for the fixed bearing and there is no way to reduce endplay. The fixed bearing can have decent amount of axial play just due to the internal axial clearance of the bearing (a function of the installed radial clearance). If snap rings are used, those introduce additional axial endplay. A bearing plate eliminates snap ring tolerances though at a significant cost and added complexity. Some people like to try and press fit the outer ring of the fixed bearing as well. You will find that after you increase the bearing internal clearance to compensate for the housing press fit, you are not any farther down the road in terms of reducing overall runout. In either case, we never rely on press fits as a retaining feature when taking direct axial loads. A snap ring is still needed in the loose or tight fit configurations. You can usually get away without a snap ring on the press fit side of the float side – though it is always recommended to package protect for it.
Another popular design is called a full float or straddle mount type of design. In this configuration, each bearing takes the axial load in one direction – the bearings share the axial load. This is done by constraining the outer rings in only one direction. This can be handled from the inside corners or the outsides. In the outer shoulder arrangement below (Figure 3), the right bearing will take all axial loads going to the right and the axial loads going to the left will be taken by the left bearing. A big benefit to this system is that endplay can be reduced with a selective shim, mounting screw or nut. As you shim one side, the reaction is taken by the opposite bearing through the shared loose fit housing and the outer rings are slightly pushed together. Unlike the fixed-float system, in a paired shim system, internal axial clearance be reduced or even eliminated.
Figure 2-Fixed-float design.
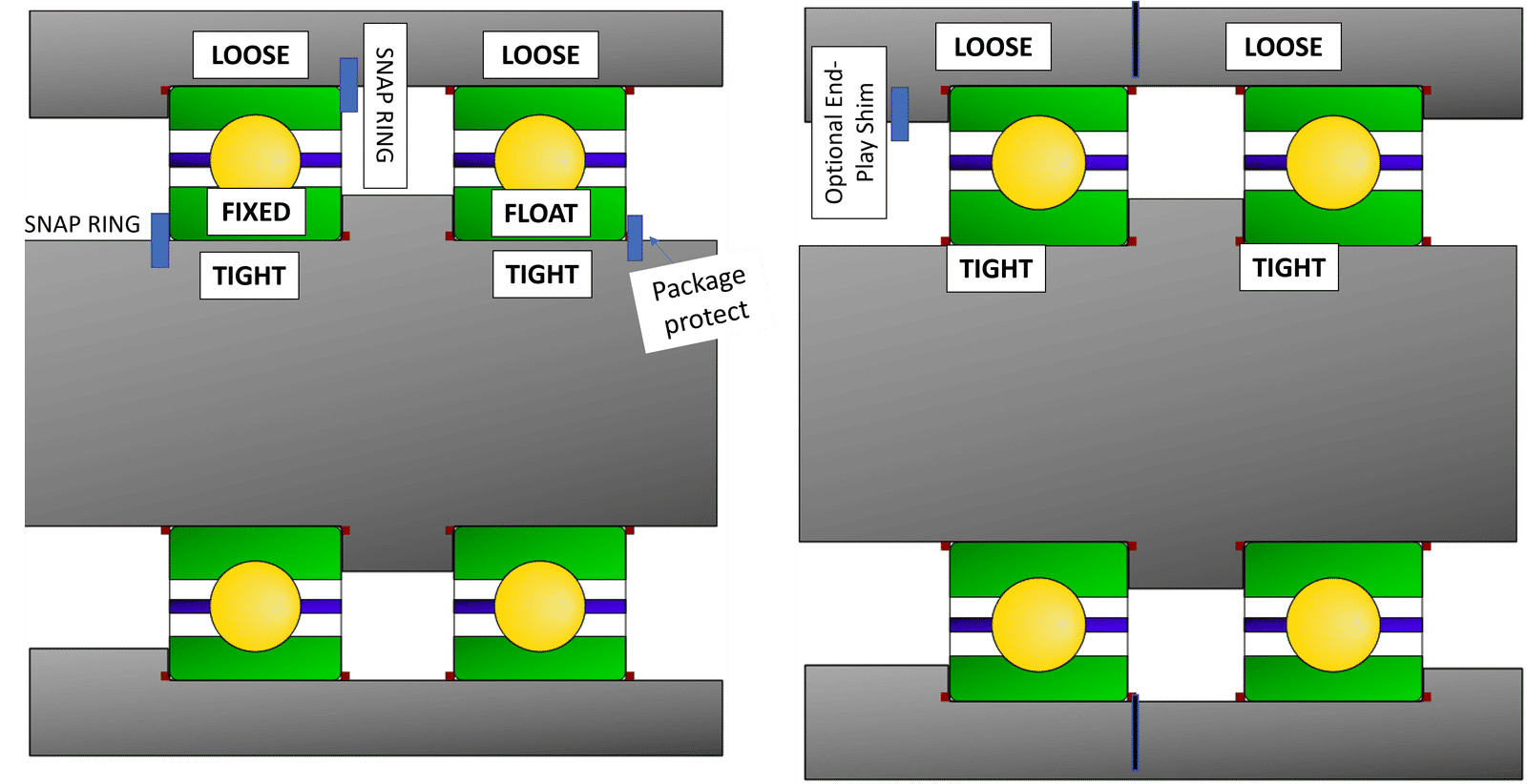