Aluminum Housing Series: Preload Change Due to Bearing Span Change with Temperature.
Previously we discussed how to determine your cup interference fit based on thermal expectations. Then we discussed how the bearing cup contracts and grows with temperature, compared with how much the housing grows and contracts. Now we will talk about how to convert that growth into an actual preload gain/loss value.
Following our last example, let’s say we started with an HM804846/10, pressed it into a 100 µm interference fit, and have since lost half of our fit due to temperature — resulting in a 10 µm growth of the outer ring.
Since we usually talk about preload in terms of axial preload for tapers, we need to convert our estimated radial loss into an axial equivalent. The example in Figure 1 is an exaggeration, of course; we usually aren’t talking about complete loss of preload. Rather, how preload changes with temperature so that we can eventually design that back into our system.
Figure 2 shows the simple conversion from radial loss to axial loss with a known bearing cup angle. This value can be found on most manufacturers’ websites. For our example, a 10 µm ring growth translates to a 27.4 µm axial loss.
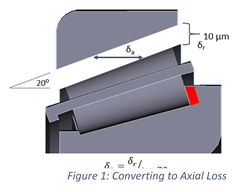
One of my go-to places to evaluate this is Koyo’s website. That isn’t a plug — they just have the easiest-to-use calculator for axial and radial displacement vs. load (in the Elastic Displacement section).
Looking at the chart in Figure 3 you’ll notice that 27.4 µm in axial loss could result in 20kN of preload loss — if that is all you looked at. Don’t panic just yet; we still have a lot of elastic displacement to consider.
People have tried in various ways to eliminate this cup growth by simply starting with a slip fit on the cup — no
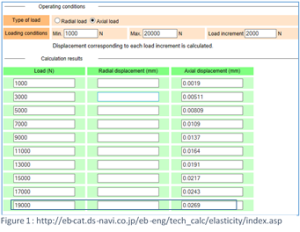
Next week we will discuss the losses due to the change in bearing span with temperature and start putting together a full preload loss vs. temperature estimation.