Considerations for Choosing the Correct Rolling Element Bearing Characteristics
Daily experience in application engineering has proven that the selection of the correct bearing type can be successfully achieved by customers based on the documentation and tools provided by the bearing manufacturer and using comparable applications as a guideline.
This selection process is typically dominated by two complementary factors: First, the required bearing life rating in the application as a result of the relation between the bearing’s dynamic load rating and the magnitude and direction(s) of the forces acting and the speed of rotation. Second, the build size of the bearing in relation to the available space in the application.
In addition, there are several other, critical bearing characteristics which are not always considered with the required diligence and may later cause questions and issues to arise in the actual bearing application. From practical experience these are, amongst others: Clearance; cage type; lubrication; standard, pre-installed sealing variants in radial deep groove ball bearings and others.
The following shall be considered an overview and aid when considering those characteristics in a design and aims at addressing reoccurring questions regarding these topics.
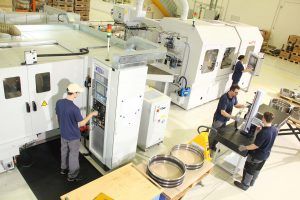
Clearance
The nominal bearing clearance is the distance between end positions which the rings of a rolling element bearing may be moved against each other. For most radial rolling element bearings this radial distance of movement, better known as radial clearance, is provided in publications while paired or double row angular contact ball bearings and taper roller bearings are listed with an axial clearance. Ranges of clearances are combined in (radial) clearance classes which are standardized to a large degree acc. to DIN 620 and easily identifiable by the suffixes C3, C4 etc.The bearing clearance has a significant influence on the function and performance of a rolling element bearing and it shall be considered that with few exceptions in special applications a bearing always needs a certain amount of clearance for proper operation – the so called “operating clearance.”
This operating clearance results primarily from the chosen clearance class of the rolling element bearing in conjunction with the shaft and housing fits required for a specific application, the material of shaft and housing resp. their thermal expansion coefficient and the temperature difference between shaft and housing during operation potentially including additional heat being transferred into the application via the shaft. Typically these factors cause a „constriction“ of the bearing thereby reducing the nominal clearance often considerably and in a worst case scenario may lead to an unintentional preload.
To recognize the risk of an unintentional preload which typically causes additional friction loss and heating thereby posing a very real risk for a premature bearing failure it is highly recommended to add an operating clearance evaluation to any bearing selection process. The bearing clearance class offering sufficient clearance during operations shall be chosen.
Corresponding formulas are published in the bearing manufacturers‘ technical documentation and the application engineering department is able to support the customer with a detailed analysis and recommendations.
Cage type
Every bearing is supplied by the manufacturer equipped with a standard cage type which in the sum of it’s characteristics - mainly the material and the cage guidance - is suitable for use in „standard“ applications.A more detailed check of the cage type typically in cooperation with the bearing manufacturer to be used in a specific application is recommended when the following operating conditions occur, amongst others:
- Operating temperature – for example, polyamide cages (PA 6.6.) reach their limit of use at operating temperatures of 120°C. Beyond this temperature metal cages must be used or the application of special plastic cages such as PEAK evaluated.
- Fast acceleration and/or low loads – in such cases depending on the bearing type and size the use of lightweight cages i.e. polyamide or pressed steel cages or ring guided cages must be considered to avoid the weight of the cage decelerating or blocking the movement of the rolling elements subsequently causing smearing damage due to slippage.
The same principle also applies to applications in which rolling element bearings are subjected to shock loads, vibrations and high centrifugal forces e.g. on eccentric shafts.
- Lubrication situation – in general, grease lubricated applications favour the use of rolling element guided cages as the formation of a sufficiently stable lubricant film in the gap between a ring guided cage and the ring itself oftentimes cannot be reliably achieved.
Oil lubricated bearings are typically not subject to such restrictions. They do however require additional design effort of the bearing‘s periphery. One additional consideration must be the compatibility of hi-tech, fully synthetic lubricant oils with plastics and rubber used for cages and external seals. These custom rubber parts can be ordered directly from a custom rubber parts manufacturing service company.
Lubrication
The selection of the correct lubricant resp. the evaluation of the suitability, and service life of a lubricant e.g. in pre-greased and sealed radial deep groove ball bearings represents – besides the topic of bearing clearance – one of the most underestimated topics in the use of rolling element bearings. On one side the best possible lubrication effect to minimize friction and metallic contact under realistic operating conditions must be considered. On the other side any lubricant is subject to aging during operation depending on the actual operating conditions. Most often the lubricant’s performance is degraded to an extent that it has reached the end of it‘s service live well before the rolling element bearing itself. The actual operating temperature again plays a significant role in this context. In summary an evaluation of the lubricant is definitely recommended for most applications in cooperation with the lubricant manufacturer and supported by the bearing manufacturer.Standard, pre-installed sealing variants in radial deep groove ball bearings and others
Several misconceptions exist in regard to the use and performance of pre-installed bearing seals offered by the manufacturer which in turn may have an impact on the actual bearing’s performance and longevity.First and foremost is the fact that contacting bearing seals shall not be considered liquid-tight. This results from the very limited space into which such seals are integrated and the necessary design compromise between sealing efficiency and minimization of friction and associated frictional loss. Depending on the actual application it is therefore recommended to carefully evaluate pre-installed bearing seals in terms of the required sealing efficiency and balance it against acceptable, frictional loss. If the solutions on hand are found to be insufficient the use of special bearings e.g. with integrated radial oil seals can be considered or provision must be made for additional, external sealing measures of the bearing position.
A second topic often occurring in the context of pre-greased and sealed rolling element bearings is the build-up of a „grease collar” at the sealing gap or sealing lip. This grease collar results from a small amount of grease being expulsed during the internal grease distribution process once a bearing starts to operate. Although it may impact on the visual perception of a bearing this grease collar is actually not a defect but rather an additional protection for the bearing as it captures contamination well outside the bearing and away from the actual sealing gap or sealing lip thereby helping to further delay an intrusion of contamination into the bearing itself. In certain applications were a grease collar is not desired for practical reasons it can be minimized by reducing the grease quantity and performing a run-in procedure prior to the installation.
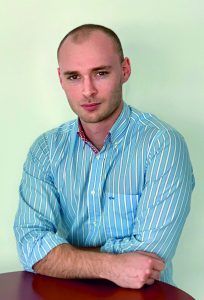
Conclusion
The topics mentioned are naturally only a small – but important – selection from the multitude of aspects to be considered when using rolling element bearings.It is therefore recommended to also take advantage of the information contained in technical literature such as the NKE Austria General Catalog.
In addition, NKE Austria offers the customers it’s application engineering services to facilitate the design of bearing applications and help clarify any technical aspects of rolling element bearings.
For more information:
NKE Bearings Austria
Phone: +43 7252 86667
www.nke.at
About the author:
David Schaljo is head of application engineering with NKE Austria GmbH in Steyr, Austria.