Schaeffler Optimizes Lubrication Systems with Mechatronics
The following is an update on Schaeffler's DuraSense relubrication system for linear recirculating roller bearing, ball bearing, and guideway assemblies. The technology was featured during Hannover Messe 2019 in Germany. The product in question can save customers up to 30 percent on lubricant. It can also reduce the number of lubricant system malfunctions and the number of failures due to contamination.
Certain auxiliary equipment is prone to being forgotten once initial operation has been completed – including lubrication systems. If no unexpected failures occur, the lubrication intervals and lubricant quantities that were initially defined generally go unquestioned. In this context, a requirement and load-based lubricant supply – which can be achieved with Schaeffler DuraSense – offers enormous potential for extending machines’ operating times and reducing maintenance costs.
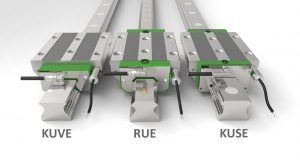
Three relubrication options
Schaeffler DuraSense provides three different ways of carrying out relubrication. In its basic development stage, the system can be used to monitor, assess, and if necessary optimize manual relubrication or interval lubrication systems. The Schaeffler DuraSense sensors and the relubrication system are independent of each other in this case.
In the automatic variation, the Schaeffler DuraSense sensors and the lubrication system are linked together in a single control loop. Fixed lubrication intervals are omitted and the lubrication system is activated only according to the lubrication indicator. Suitable lubrication systems include both Schaeffler products such as the Concept2 and Concept8 automatic lubricators and central lubrication systems, for example.
There are two ways in which lubricating impulses can be triggered. The first is for the evaluation unit to deliver 24V trigger signals for each of the seven channels. The 24V outputs can connected to both the relubrication units and the machine control system. The second option allows the lubrication indicator value to be emitted as a 4-20mA signal for each of the seven channels as an alternative to the 24V signals. Using this variant makes it possible for lubrication conditions to be continuously monitored, the relubrication function to be adjusted with even greater flexibility, and the signal used for further analyses such as future remaining useful life calculations. In addition to the two analog outputs, Schaeffler DuraSense will also feature field bus protocols from the second half of the year onwards. Anybody can then configure the selection of the outputs as well as the type and number of carriages using a new software program.
Manifold benefits with a simple system design
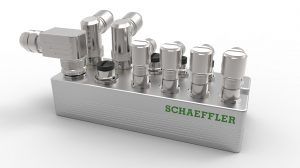
Schaeffler DuraSense also reliably detects relubrication system failures, e.g. due to defective lubrication units, leaking hoses, or blocked lubricating nipples, by correlating the relubricating impulses and the subsequent vibration signals. Complex monitoring using pressure sensors such as those used in centralized lubricating systems is not required. The new system thus optimally protects even heavily interconnected systems against very costly downtimes.
For more information:
Schaeffler Group
https://www.schaeffler.de/content.schaeffler.de/en/products-and-solutions/industrial/industry-4.0/mechatronics/index.jsp