During Automate 2023 (Detroit), Kuka Robotics will feature a well-rounded range of solutions for meeting the automation mobility, education, safety and other needs of today’s manufacturers in Booth #2623. Within two cells for the Fast Moving Consumer Goods (FMCG) industry sector and in a mobile machine tool-tending cell, Kuka will showcase its KMR iiwa, KMP 600-S diffDrive and KMR Cybertech mobile robots. Kuka’s new LBR iisy cobot will be on display with an education package along with Kuka’s new Ready2_educate and Ready2_educate_arc training carts. Also on display will be Airskin technology for safe, fenceless operation of industrial robots when humans are present as well as a large composite 3D printing cell.
For the FMCG industry, Kuka will show the capability of its Agilus, Delta HM and Scara robots working with a KMR iiwa mobile automation platform in a pick and place/bin picking demonstration cell. For vision capability, the cell uses a 3D camera and Mech-Mind 3D vision system for recognizing randomly situated materials, even those with dark or reflective surfaces and complex structures. Once an object has been identified and selected, the trajectory planning system governs robot movements and provides the orientation required to remove the object without colliding against the walls of a container or other nearby elements.
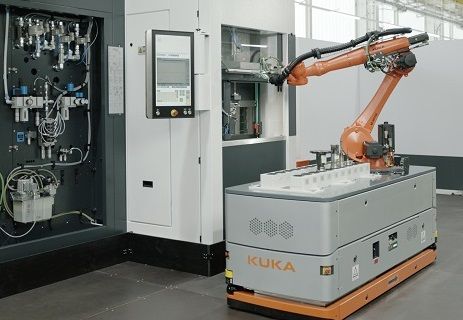
Kuka’s KMR iiwa mobile robot in the FMCG cell is human/robot compatible, combining the strengths of the company’s sensitive LBR iiwa lightweight robot with those of a mobile, autonomous platform. The KMR iiwa is location-independent and highly flexible, making it the perfect fit for today’s Industry 4.0 requirements.
To highlight its newly launched KMP 600-S diffDrive mobile platform automated guided vehicle (AGV) system, Kuka partnered it with a KR IONTEC robot in a cell developed by Mujin for efficiently palletizing and depalletizing consumer goods. To coordinate robot movement, the cell incorporates a Mujin controller and camera system.
With an operating speed of up to two meters per second, the Kuka KMP 600-S diffDrive mobile platform is fast and uses laser scanners and 3D object detection to meet the highest safety requirements, taking industrial intralogistics to new levels. Its payload capacity is up to 600 kilograms, and the vehicle requires no safety fencing to provide maximum freedom of movement for employees, while laser scanners mounted at the front and rear ensure safe operation at high speeds in all directions of travel when cycle times require it.
In answer to the ongoing lack of skilled labor, Automate 2023 attendees will see a Waybo mobile machine tending cell featuring a KMR Cybertech as a solution for today’s manufacturers. The Waybo series of pre-engineered compact machine tending cells are well suited for small and medium job shops that want to automate CNC machines for high-mix/low-volume manufacturing applications.
The KMR Cybertech utilizes a KMP 1500, an omnidirectional, mobile platform that navigates autonomously and flexibly. Combined with the latest Kuka controller, it provides modular, versatile and above all mobile production. This intelligent, autonomous vehicle supplies materials to robots and machines when needed. The KMP 1500 makes flexible production possible and integrates seamlessly into manufacturing operations.
kuka.com
Suhner USA, Inc.
Recognizing the role robotics plays in adding efficiency and lowering production costs for manufacturers of all types and sizes, Suhner (Booth #1850) continues to expand its robotics offering. The fully electric EFC-02 delivers precise, constant force throughout robotic grinding, sanding and deburring processes – resulting in superior, consistent surface quality.
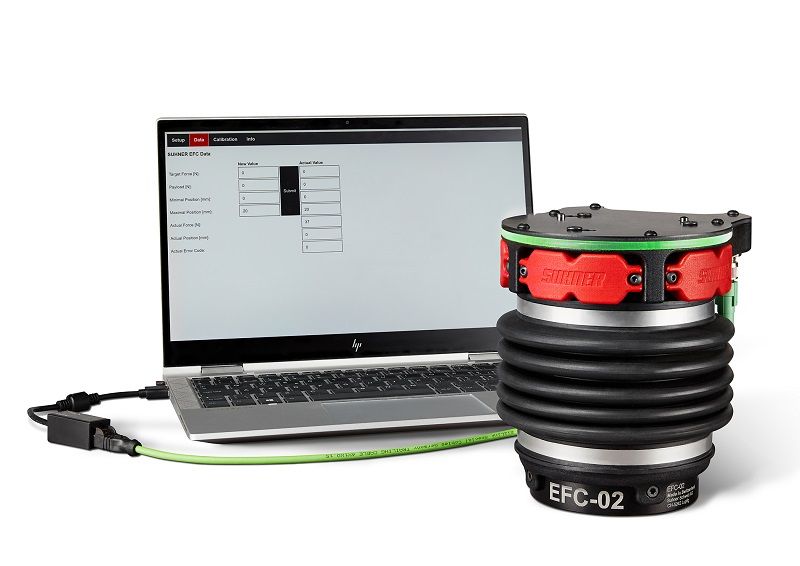
With today's supply chain and labor challenges, manufacturers of all types and sizes are looking for solutions to help them do more with fewer resources. That's what smart manufacturing is all about – and why Suhner is expanding its suite of robotic grinding accessories and tools with the fully electric EFC-02 active compliance system.
Exact contact force with the surface is the single most crucial factor in robotic grinding, sanding and deburring processes. It's also one of the biggest challenges, especially for hard-to-reach areas. Thoughtfully designed based on Suhner's decades of material removal process know-how – the EFC-02 helps overcome that challenge.
As with any end-of-arm tooling, the EFC-02 connects a grinding machine – angle grinders, orbital sanders, angle polishers, straight grinders and others – to the robot. What makes Suhner's system unique, however, is its compact design and fully electric operation.
The lightest and smallest in its category, the EFC-02 can be used for material removal or surface finishing even in tight or narrow spaces often found when processing stainless tanks and vessels for the food and pharma industries or fiberglass bathtubs and sinks. The all-electric technology also allows high-frequency measurements to monitor force and acceleration throughout the process. An advanced control algorithm then dynamically adjusts force and automates grinding processes based on pre-programmed parameters.
The result? Constant contact force with each movement from start to finish for a consistent surface quality – regardless of the surface type, shape, size or orientation.
suhner.com