The cost-efficient solution combines condition monitoring with decarbonization by supplying the user with important additional data and energy costs. Another new feature is pump analytics, which Drivetrain Analyzer Cloud can use to calculate and analyze system efficiency and specific pump parameters.
In addition to the cloud solution, Siemens is also presenting another new product, a PC-based condition monitoring solution consisting of three components: the new VIB (Vibration) and FPP (Fast Process Parameters) (CM FPP) connection modules, the Drivetrain Analyzer X-Tools software, and the corresponding sensors and sensor cables. The CM VIB and CM FPP connectivity modules record vibration and analog signals at a sampling rate of 96 kHz. All sensor information can be recorded and transmitted synchronously.
Now users can also analyze high-speed, intermittent machines such as automotive presses, cranes, or machine tools with two synchronous axes. Drivetrain Analyzer X-Tools is an expert tool for highly dynamic data acquisition up to 192 kHz as well as for manual data analysis. Because X-Tools can connect to almost any data source, users can ideally use X-Tools as an analytics toolbox to link their own analytics with elements of a preconfigured library.
For example, the software can be used to monitor bearing temperature, housing vibrations, and oil lubrication, meaning pressure and flow, in heavy machinery equipped with plain bearings. In this way, Drivetrain Analyzer X-Tools and the new connectivity modules contribute to higher machine availability, better performance, and a longer system service life.
usa.siemens.com/ddt-pr
Festo Introduces ELGD-Based Handling System
Festo introduced its newest generation of Cartesian-handling-system mechanical axes at Automate 2024. The ELGD-TB, tooth belt, and ELGD-BS, ball screw, axes feature an innovative Festo design for high-load bearing and compact size. These axes are manufactured on two new global-scale manufacturing lines to ensure competitive price, performance, and availability.
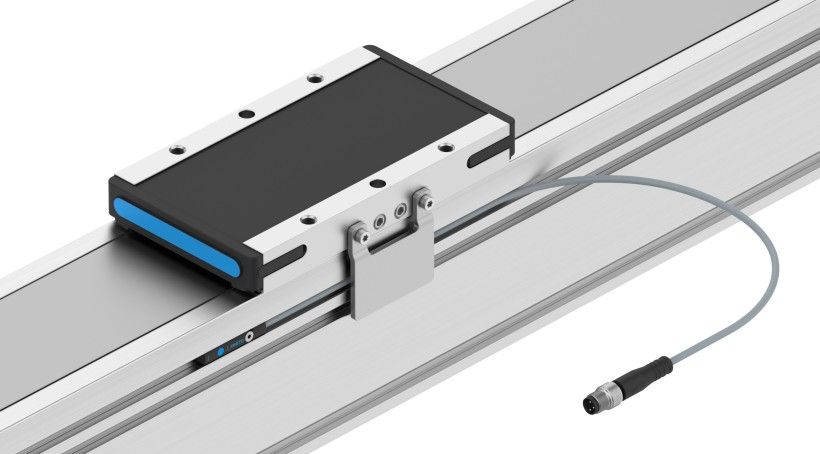
Festo demonstrated an integrated dispensing, gluing, and picking-and-placing electric light assembly cell. The cell simulates an actual application and features ELGD-based handling systems. The demonstration showcases the application’s precision and versatility in performing three assembly functions, all in a compact footprint.
Suited to most electromechanical handling tasks, the ELGD series brings specific benefits to applications, such as:
Cantilever systems and pick-and-place solutions for small parts handling, where short cycle times, high precision, and repeatability are key handling systems for top loaders, which benefit from the ELGD’s attractive price/performance ratio, high travel speed, and long stroke lengths.
Automation of 3D printing, additive manufacturing, dosing, gluing, and picking and placing are enhanced with the ELGD’s dynamic, virtually vibration-free movement.
Festo inlaid the bearings into the aluminum extrusion and extended bearings to the full width of the axis. This design enhancement enables high loads in a compact footprint. Machine builders can pack even more powerful tooth belt or ball screw axes in smaller footprint systems to achieve excellent feed forces and acceleration profiles. The integrated bearing design also enabled Festo to develop the lower profile ELGD-WD (wide actuator) for reduced force applications. This low-profile ELGD is 30 percent lighter than larger units while its rigidity and guide load capacity are similar.
The ELGD features a stainless-steel cover strip, which minimizes particle emissions in cleanroom applications and reduces ingress of particles in dirty environments. Festo enhanced particle emissions capability by including a pneumatic connection to provide sealing air (0.1 – 0.2 Bar) or a vacuum to the internal structure of the mechanics. Another innovation is the magnetic deflection of the cover strip, which eliminates mechanical wear and further reduces the likelihood of particle emissions.
festo.com
Kardex Demonstrates FulfillX Robotic Cube Storage System
Intralogistics solutions provider Kardex appeared at Automate 2024, North America’s largest robotics and automation event in Chicago (May 6-9), demonstrating the fastest order fulfillment solution per square foot on the market. Kardex FulfillX is a warehouse execution system (WES) purpose-built to allow new AutoStore systems to ramp up faster and is capable of meeting or exceeding business cases in as little as six months. It has been specifically created by experts at Kardex, a global AutoStore partner, to maximize the capabilities of AutoStore robotic cube storage systems for manufacturing customers.
Kardex solutions offer manufacturers efficiency, flexibility and short training times
Visitors to Automate 2024 saw FulfillX in action, with demonstrations of how it can create user-friendly, highly configurable AutoStore systems. FulfillX optimizes picking and packing, while also streamlining putaway and other inventory processes. It provides a real-time overview of the whole operation in a simple window. Enhancements can be rapidly deployed by Kardex’s dedicated AutoStore support team and digital twins enhance planning and commissioning.
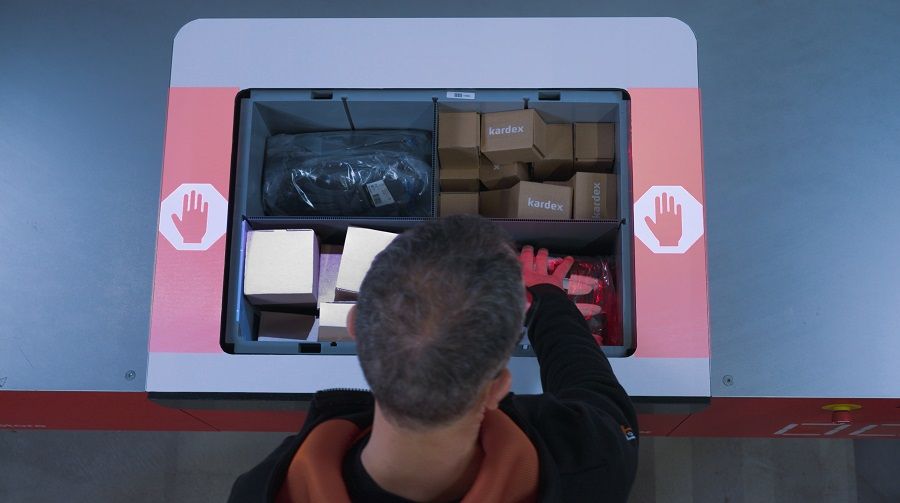
As well as promoting the benefits of FulfillX, Kardex’s booth used digital tools and augmented reality to bring to life the Kardex Intuitive Picking Assistant and its range of smart intralogistics solutions. Kardex’s Intuitive Picking Assistant solution is suitable for a wide range of industrial manufacturing applications, including spare parts picking, visual direction, and kitting. It uses digital tools and augmented reality to enhance picking processes by responding to movements and projecting relevant picking information directly onto the surface of the access opening. The Intuitive Pick Assistant is compatible with both and AutoStore ports to facilitate accurate, ergonomic picking, and can be tailored to specific customer requirements. In addition, it can be used to direct operators through kitting processes.
As US manufacturers increasingly turn to warehouse automation technology, AutoStore empowered by Kardex FulfillX provides them with the opportunity to slash their facility footprint, reduce workload, manage spikes in demand, and address labor and skills shortages.
Automate offered the ideal opportunity to introduce US manufacturers to AutoStore empowered by Kardex FulfillX. FulfillX represents the next evolution of ASRS technology. At Kardex we are committed to pushing the boundaries of what is possible with intralogistics automation. Our advanced software solutions provide manufacturers with the flexible, convenient and efficient capabilities they need to meet industry challenges now and, in the future,” said Mitch Hayes, president of Kardex Solutions.
kardex.com
ABB Introduces Mobile Robot with AI-Based Navigation Technology
ABB Robotics has announced its first Flexley Tug T702 autonomous mobile robot equipped with AI-based Visual SLAM navigation technology and the new AMR Studio software, enabling first-time robot users to easily program and operate entire fleets of mobile robots. The new capabilities simplify configuration and can reduce commissioning time by up to 20 percent, paving the way for a workplace where intelligent robots operate autonomously, amid a critical shortage of skilled labor.
“Following our acquisition of Sevensense in January, I’m pleased to offer our first AMR with AI-based Visual SLAM technology and AMR Studio software. This combination of mobile robotics and leading AI-powered navigation technology brings unmatched intralogistics flexibility and scalability for ABB’s customers, in an environment that is shifting from linear production to dynamic manufacturing networks,” said Marc Segura, president of ABB Robotics. “The AMR T702 is a perfect match for a wide range of industries, such as automotive, consumer goods sector or logistics, especially in large, busy warehouses and fulfilment centers where the environment is constantly changing.”
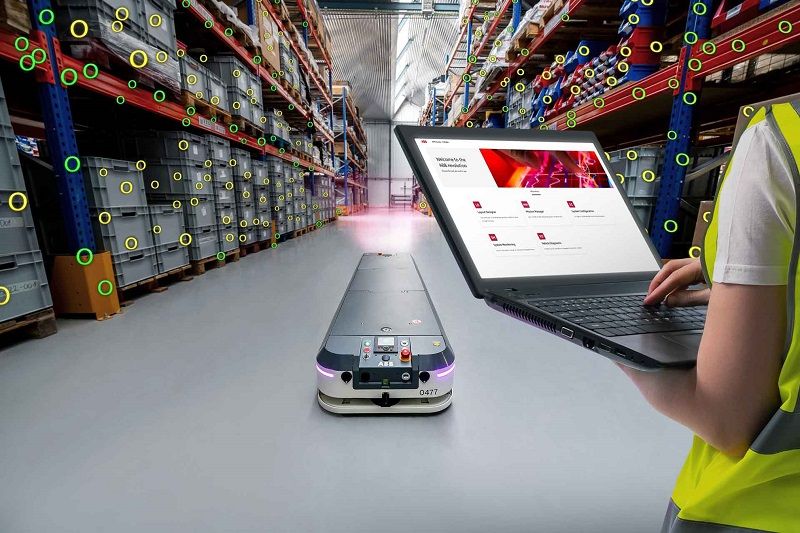
The latest announcement follows the acquisition of Swiss start-up Sevensense in January as ABB continues to expand its portfolio to meet the growing market for mobile robots, which is expected to expand at a rate of 20 percent CAGR through 2026, from $5.5bn to $9.5bn.
Combining AI and 3D vision, Visual SLAM technology enables AMRs to make intelligent decisions, differentiating between fixed and mobile objects in dynamic environments. Using Visual Simultaneous Localization and Mapping (Visual SLAM), the robots can create a map that is used to operate independently, reducing commissioning time from weeks to days and enabling fully autonomous operation in highly complex, dynamic environments alongside people. Maps are constantly updated and shared across the fleet, offering instant scalability without interrupting operations and greater flexibility compared to other navigation technologies.
The new capabilities offered by Visual SLAM are further enhanced by the launch of ABB’s AMR Studio software, which enables inexperienced users to easily create and configure AMR routes and jobs, with no programming knowledge needed. AMR Studio streamlines the process of setting up an entire AMR fleet from start to finish, guiding users through the necessary steps, from environment mapping to mission generation and system configuration.
go.abb/robotics
Ellison Technologies’ AutoPilot Powered by D:PLOY
OnRobot has also collaborated with provider of advanced machining solutions, Ellison Technologies, on the new AutoPilot powered by D:PLOY showcased recently at Automate 2024. Ellison’s AutoPilot powered by D:PLOY simplifies the process of deploying and redeploying CNC machine tending applications.
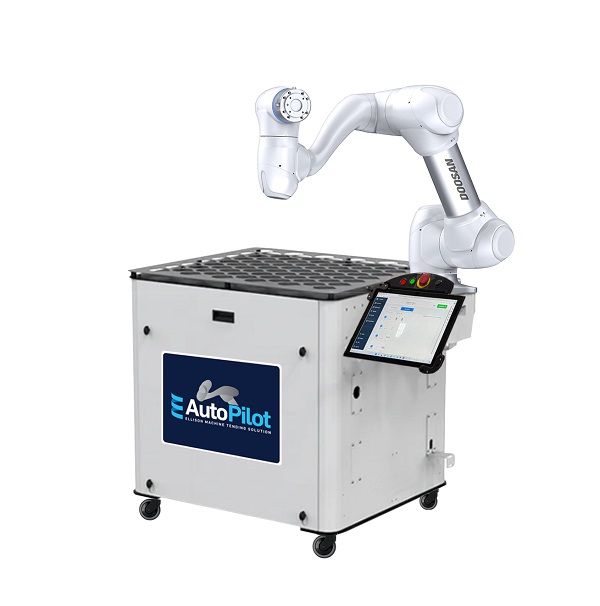
OnRobot’s D:PLOY is industry’s first automated platform for building, running, monitoring, and redeploying collaborative applications. D:PLOY automates the deployment process, which slashes deployment times and enables deployments to take place on the factory floor - with zero programming and zero simulations required.
“Companies racing to plug labor gaps and meet growing demand in an uncertain economic climate can’t afford to spend weeks deploying and redeploying CNC machine tending automation,” says Greg Haley, VP of Automation at Ellison Technologies. “D:PLOY is the perfect software for Ellison’s AutoPilot solution as it decreases the programming complexity and makes part changeover a snap. This puts automated CNC machine tending in reach for more customers than ever, even those with high mix, low volume part runs.”
onrobot.com