Kollmorgen robotics experts will be available throughout the show to answer questions and discuss real-world applications.
kollmorgen.com
KUKA Robotics: Booth #1832
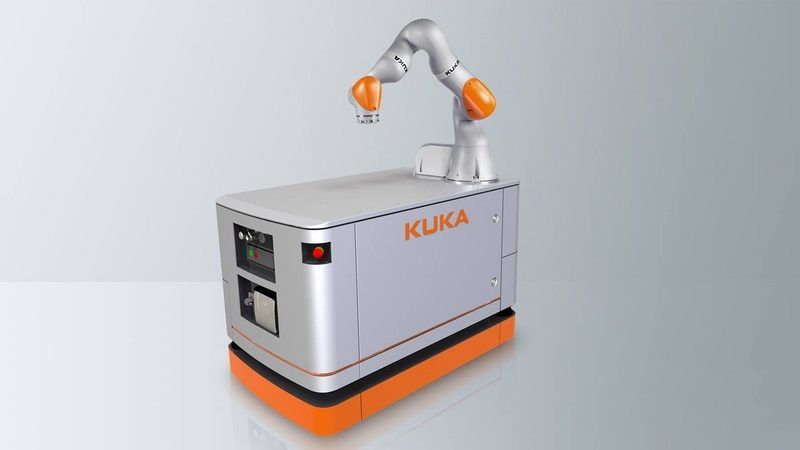
At Automate 2022, attendees will have the opportunity to experience how complete, end-to-end automation solutions from KUKA Robotics can help them exceed their production goals. In Booth #1823 at Huntington Place in Detroit, MI – near the company’s North American headquarters – KUKA will spotlight a multi-robot cell targeting the Fast-Moving Consumer Goods (FMCG) industry, a bolt-picking cell, palletizing/depalletizing cell, automation software and simulation technology and robots performing bin picking and friction stir welding (FSW).
From receiving raw material and sorting to packing and distributing the finished goods, the FMCG demonstration will showcase three different KUKA robots and advanced vision software, such as KUKA.VisionTech, working together to show attendees from the FMCG industry sector an example of end-to-end automation relevant for their production facilities. The cell features the new KR 3 DELTA robot, a KR 6 SCARA, a KR 6 AGILUS and KMR mobile robot with an LBR iiwa.
The KR DELTA hygienic robot, which is rated IP 67 and constructed entirely of stainless steel, performs challenging high-speed pick-and-place applications in the food and packaging industries. KUKA’s KR SCARA ultra-compact robot provides fast and efficient operation for practically any FMCG-related task. Perfect for small automation cells, the KR 6 AGILUS combines an ultra-compact, interference-free design, while the KMR mobile unit carries a light-weight robot for a location-independent and highly flexible automation solution.
Showcasing vision technology and robot accuracy in challenging applications, KUKA System’s automated bolt-picking system will show how the company has accomplished the impossible automation task of precision bin picking of bolts for automotive assembly tasks. The production proven system uses a Keyence 3D vision system to identify which parts to pick and calculate the optimal robot motion paths that eliminate collisions between the robot and its surroundings as it approaches and picks the parts. The system outperforms traditional bowl feeding systems, providing increased uptime and availability required in high throughput automotive applications.
In another demonstration of machine vision technology, a palletizing/depalletizing cell will feature the results of the company’s work with Roboception GmbH, a pioneer of 3D sensor technology interfacing with KUKA’s robot controller. Roboception developed a cost-effective 3D vision system that applies artificial intelligence (AI) and can quickly identify box locations for the next pick action to be completed by the KR Iontech robots.
Visitors to the KUKA booth at Automate will also have two opportunities to directly interact with the company’s automation technologies. KUKA’s ready2_pilot intuitive controller package will allow visitors to actually “teach” a robot through manual guidance as an alternative to conventional programming, while the company’s smart simulation software, KUKA.Sim, will provide them with a virtually interactive experience through a virtual reality (VR) headset. KUKA.Sim provides efficient offline robot programming for optimizing both systems and robots outside of an actual production environment.
Automate attendees will also see KUKA’s robotic friction stir welding (FSW) process as part of a live demonstration welding aluminum parts to manufacture an assembly. The cell will consist of multiple robots. One robot will pick parts from bins and place them into a fixture using both Roboception and Sick PLB 3D vision technologies, and a second robot will perform FSW. The FSW process applies to many applications, including the production of Electric Vehicle (EV) battery trays. For this process, KUKA has engineered its cost-effective KUKA cell4_FSW modules to provide up to 95% more process efficiency and maximize the available configuration options for manufacturers.
Used for both 2D and 3D welding tasks, the modules are scalable and accommodate either one or two 6-axis robots. Shops can arrange several workpiece clamping tools in the working area of the cell so that robots can work simultaneously on larger components if needed.
kuka.com
FANUC America: Booth #3323
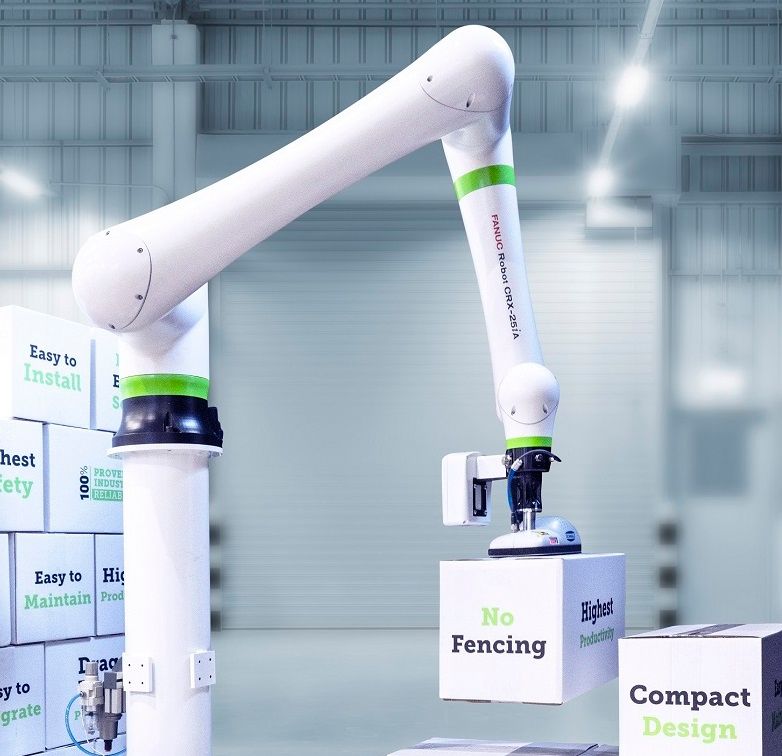
FANUC America will introduce the new DR-3iB/6 STAINLESS delta robot for primary food handling at Automate 2022. FANUC will also demonstrate its latest products including the new CRX cobot series and CR-35iB collaborative robot, the new M-1000iA heavy-payload robot, the new LR-10iA/10 material handling robot for machine tending and warehousing applications, and much more.
The new DR-3iB/6 STAINLESS is FANUC’s first stainless steel food-grade delta robot for picking and packing primary food products. Rated IP69K, the robot meets USDA and FDA food safety standards, and sets a new benchmark for robotic food handling in terms of payload, speed, reach and sanitation.
The DR-3iB/6 STAINLESS features a fully enclosed stainless-steel body that is resistant to the chemicals and high pressure/temperatures required in strict wash down environments. The robot’s mirror-like surface finish ensures that any microbial contaminants can be washed away cleanly. With additional features such as NSF H1 food grade lubricant, secondary oil catch basins (with viewing windows to monitor potential leaks), self-draining surfaces, and many other small details driven by USDA/FDA standards, the DR-3iB/6 STAINLESS is ideally suited for primary food handling applications.
FANUC recently expanded its series of CRX collaborative robots with the new CRX-5iA, CRX-20iA/L and CRX-25iA. The new CRX cobots complement FANUC’s existing line of CR and CRX cobots that now total 11 model variations able to handle products from 4 to 35kg. Designed for companies looking to increase their capabilities and overcome labor issues, FANUC’s CRX cobots are extremely robust and can run for up to eight years without maintenance.
FANUC’s new CR-35iB collaborative robot with a 35kg payload can work in a variety of applications that typically require lift assist devices or custom equipment. In addition to being the industry’s strongest cobot, the CR-35iB has a large work envelope, and small installation footprint, making it ideal for tight spaces. A more streamlined and lighter mechanical unit includes FANUC’s latest sensor technology for safety.
At Automate, the CR-35iB will help an operator assemble a bicycle. The operator will program various assembly positions with the easy-to-use tablet TP featuring a “drag and drop” user interface. The demonstration underscores the cobot’s ability to make the assembly process quicker while eliminating ergonomic stress.
In addition, FANUC will offer a Linear Motor demo arranged in an X/Y table application. FANUC’s LiS-B series linear motors have set new standards for acceleration, precision and speed, delivering high gain and rigidity with excellent path accuracy. Unlike conventional drives, these motors work without any force transmission mechanisms, making machine design and maintenance easier (no ball screws, no backlash). The linear design enables rigid long-stroke axes, increased thrust force and multi-head configurations by arranging multiple coil sliders on a single magnet track.
All the industrial PC options FANUC provides for its CNCs at the Panel i Industrial PC demo. Designed with the latest technology, these industrial PCs provide a powerful platform for custom developments and are available in a variety of display options. Plus, if you have legacy PCs, check out our Panel i Upgrade program to keep your operations safe from cyberattacks.
fanucamerica.com
Automate 2022 takes place June 6-9 in Detroit. (Booth numbers subject to change prior to show).
automateshow.com
powertransmission.epublishing.com/articles/8538-rapid-advancement-at-automate-2022