Dr. Michael Platten, Senior Product Manager—Romax, explains some of the highlights from the 2023.1 release of the Romax software suite which includes updates to Romax Spin.
Modeling and Usability: The 2D Worksheet now shows which bearings have 1D raceway connections. This allows users to quickly check all the bearings in a model to see which are configured to have 1D raceway flexibility and which do not. (Note, a similar visual check if bearings have 3D (FE) raceway flexibility is enabled.)
Journal Bearings: The operating temperature of the journal bearing lubricant film can now be directly specified. In previous versions, the journal bearing operating temperature was determined as the mean temperature of its shaft and housing. This can now be overridden with a custom value, for example, obtained outside of Romax software, and this temperature will affect the lubricant viscosity used in the journal bearing component calculations.
Rolling Element Bearings: Multi-lobe ovalization and custom bearing ring distortion. Rolling bearings may be radially deformed by design from a circular shape to a bi-lobe, tri-lobe, or other geometry to limit skidding. Previously it was possible to define ovalization (i.e. bi-lobe shape) in Romax software. Now, this has been extended to allow multiple lobes and custom shapes, primarily to enable the modeling of tri-lobe raceways, but more lobes or an entirely custom shape are also enabled. This allows parametric investigation of the applied raceway distortion and its impact on load and stress distribution and ring deformation.
Previous bearing dynamics capability in Romax Spin has a simplified representation of cages. The cages are considered rigid and they were only allowed to rotate about their own axis. This development addresses one of these limitations by adding lateral and tilt degrees of freedom to the cages, in addition to the rotation about their own axis. This would allow engineers to analyze the lateral motion of a cage and its stability by looking at the whirl orbits under various operating conditions.
A new bearing catalog from NTN has been added to Romax software. It is available alongside existing bearing catalogs and offers matching functionality. The catalog data is based on the General Rolling Bearing Catalog issued separately by NTN. As with other bearing supplier catalogs, limited data has been provided by NTN and the rest of the bearing internal and advanced data has been estimated by Romax.
The EP Additives setting is now reported alongside the lubricant name and level of contamination in the reports ISO 281 and ISO/TS 16281 Results to give the user more context when reviewing bearing life results. This feature minimizes the effort required to check the status of EP additives on individual bearings.
The EP Additives setting is now reported alongside the lubricant name and level of contamination in the reports ISO 281 and ISO/TS 16281 Results and Bearing Certification Report (ISO 281 and ISO/TS 16281) to give the user more context when reviewing bearing life results. This feature minimizes the effort required to check the status of EP additives on individual bearings.
Learn more here:
simcompanion.hexagon.com/customers/s/article/Whats-New-Romax-DT-2022-1
Schaeffler’s OPTIME Ecosystem Balances Plant Assets
OPTIME is an easily scalable condition monitoring system that consists of wireless, battery-powered vibration sensors, a cellular gateway and an app to visualize the resulting data. This information, which is captured by the sensors, is analyzed using proprietary algorithms that draw on Schaeffler’s technical expertise, its extensive library of physical models developed and refined over many decades, and the experience in condition monitoring that Schaeffler has built up during its bearing servicing operations.
OPTIME is designed to provide advance warning of potential damage to machines such as electric motors, fans and pumps. It also offers early notification of imbalance, misalignment, and loose-fitting components. The OPTIME mobile app displays trends in graph format and visualizes the severity of incidents using traffic light colors, alarm states and other information. Assets can be grouped according to the user’s requirements, and their condition can be presented in a range of user group-specific views. With OPTIME, in-house maintenance personnel and external service contractors receive specific recommendations regarding the steps required to remedy any issues, enabling them to easily plan their maintenance activities, manpower requirements and spare parts procurement in a timely and cost-effective manner.
Frank Mignano, Schaeffler condition monitoring sales manager for North America, recently discussed some of the new updates and future considerations for OPTIME:
How the OPTIME Ecosystem works
The Ecosystem consists of many elements including user interfaces, cloud and analytics, existing customer ecosystems, other Schaeffler measuring devices, condition monitoring, mesh network, smart lubrication and more.
The latest updates include vibration/temperature sensors for all “balance of plant” assets; a Smart Lubricator which reports status of single-point lubricators—full, empty, days left, clogged, excessive temperature; a cellular gateway for unimpeded connectivity to the Schaeffler Cloud; a Cloud application for implementing Schaeffler-proprietary diagnostic algorithms on the mountains of collected data—thereby converting data into actionable information; a web dashboard and smart phone application to help manage the asset health and maintenance planning activities.
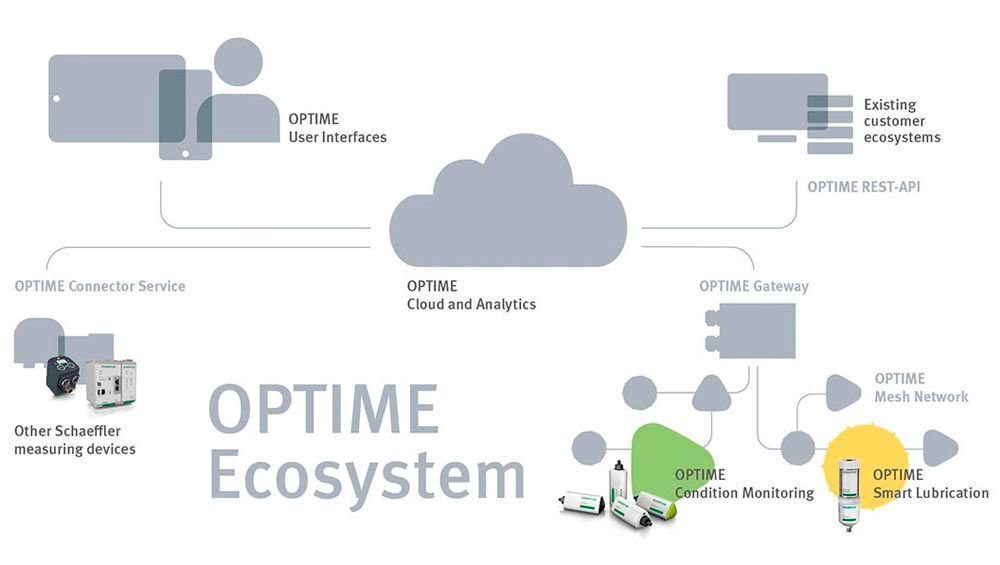
In addition, the ProLink multi-channel monitoring solution, designed for more critical assets, can also be sent to the same Cloud so the end user can manage all their asset health information in one place.
Food and Beverage Boiler Fan Application
A machine critical to the food and beverage industry—boiler fan in the fryer area—can cease production on any failures. Prior to enabling the “learning mode” alarm set points, OPTIME uses the ISO velocity recommendation (based on machine size) which alerted the customer to a higher-than-normal vibration on the machine. Utilizing the “Expert Viewer” application, the customer was able to identify the peaks in the demodulation vibration plot as lining up with the outer race frequency of the bearing. The peaks were prevalent in both the standard acceleration and the demodulation signal processing technique, indicating an advanced defect. Maintenance plans were scheduled for the fan resulting in cost savings of at least 20,000 CDN. The pilot OPTIME project identified this issue within two weeks of initial install.
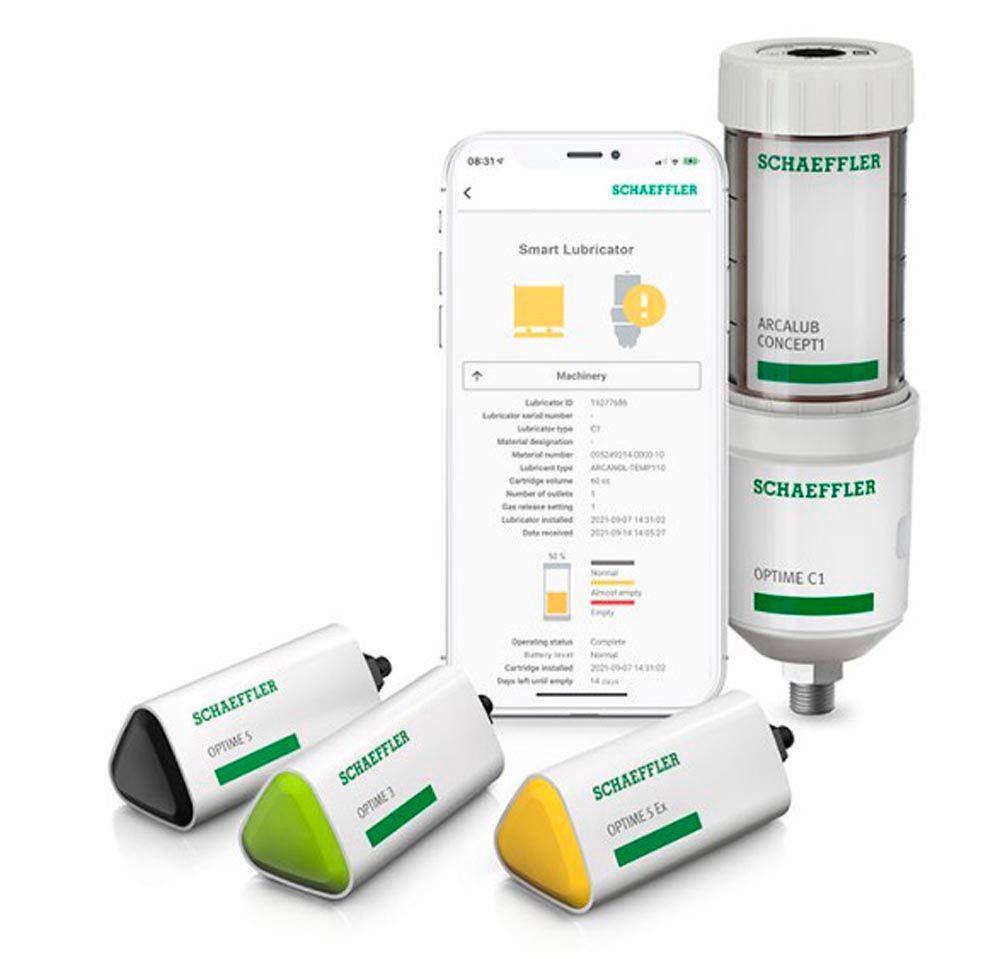
Future Considerations
Mignano offered a few planned features for future updates including: a simple drop-in, 4-port smart lubricator—connecting directly to the Ecosystem; lubrication on condition from the 4-port lubricator; dynamic mode and high dynamic mode for intermittently operating machinery (cranes, etc.) as well as significant, automated diagnostic enhancements (AI, machine learning) and electric motor-specific monitoring capabilities.
medias.schaeffler.us/en/monitor/optime-ecosystem