Posidyne retrofit with worm gearbox.
A simple actuation system allows torque in the clutch and brake to be precisely controlled. Adjustment for rapid or soft starts and stops is easily accomplished. Manifold-mounted control valves reduce response times by eliminating hoses and fittings and are recommended for high-cycle applications. By reducing the high starting inrush currents and the associated power factor imbalance in the motor these unique clutch/brakes can also reduce energy costs.
The Posidyne clutch brake can be actuated by air or hydraulic pressure for use in a plant or outside remote applications. The hydraulic actuation package includes a hydraulic pump, solenoid valve, regulators, and a filter. A heat exchanger can be added for additional cooling. It’s also inherently explosion-proof with the addition of an explosion-proof actuation valve or locating the valve in an explosion-proof cabinet. Multiple sizes are available to suit particular applications from one-half to 350 hp (99 lb. in. to 79,000 lb. in.) with cooling options, control logic, and mounting arrangements to simplify and speed installation.
Oil shear technology is the reason that clutch brakes by Force Control last up to 10 times longer than standard dry friction clutch brakes and do not need maintenance, adjustment, or disc replacement. Oil Shear Technology is the function of a boundary layer of transmission fluid in shear between the friction discs and drive plates. As the parts come together, the fluid in shear will transmit torque between the two parts, as well as absorb heat. This eliminates direct contact of the friction discs and drive plates during high-speed slip. Heat from the friction surface is dissipated as the fluid circulates to the housing.
Heat dissipation is a major component when selecting a clutch brake. The Posidyne clutch brake basic unit dissipates heat through a unique internal design pumping system which causes the transmission fluid to be drawn into the center of the hub, flow through the friction stack, and by centrifugal force is pulled out of the stack to the housing. Cooling occurs as the fluid flows down the housing walls. Additional heat can be dissipated by adding internal water-cooling or pulling the fluid out to external-oil-to water or oil-to-air heat exchangers. This also allows for the use of an oil filter extending the life of the fluid. These cooling options allow the same compact size Posidyne clutch brake to be used on high inertia loads, or in extremely high or low temperatures.
The Force Control brake also saves money, both in manufacturing costs and ongoing maintenance costs, so it’s a winning proposition not only for Wysong but also for the customers who will be using them. The company has also designed modular retrofit kits so that older-style flywheel models can be upgraded to enhance accuracy and reduce maintenance costs.
forcecontrol.com
Miki Pulley BXR Spring Applied Brakes Ideal Safety Brake for Robotic Arms
Miki Pulley is introducing their BXR Spring Applied Brakes for direct sale to OEMs in North America. The BXR safety brake may serve as an emergency brake, as well as a holding brake. Its low-profile design is two-thirds the thickness of other brakes in their lineup. In addition to saving space, weight is also dramatically reduced.
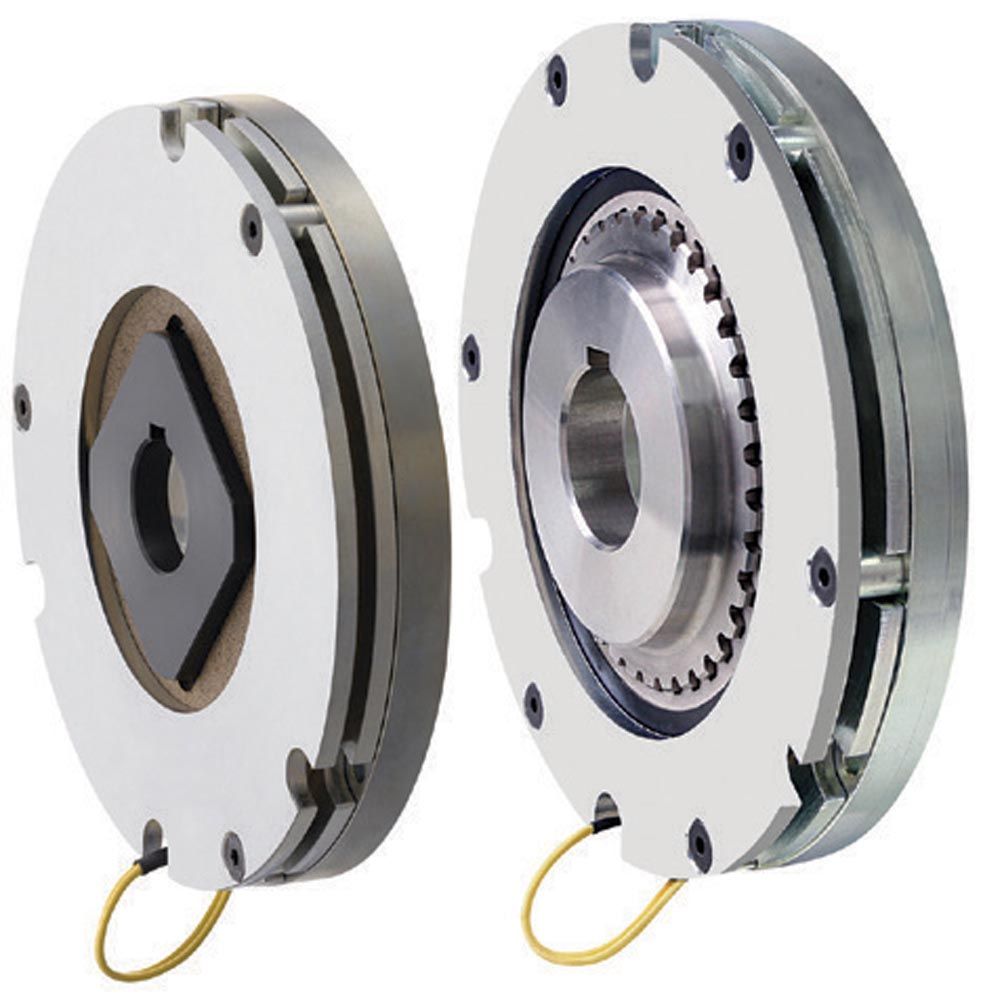
BXR Brake’s low-profile design is two-thirds the thickness of most other brake models. Lightweight and energy-saving, this fast-response brake is ideal for servomotor applications.
The BXR is an ideal safety brake for robotic arms. In these applications, when a catastrophic power failure occurs, robotic arm movement must be halted immediately to prevent mechanical system collapse and equipment damage. In the event of power failure using the BXR safety brake, compression springs engage and capture the brake’s rotor hub immediately stopping arm movement. Designed with a very thin profile, the BXR saves space in articulating joints. Idling wear is also reduced significantly because of its lightweight construction. The BXR brake may also be installed on the output face of a servomotor, serving as a power-off holding brake. This can be an advantage when the overall assembly size must be contained in a small envelope.
Additional design benefits include a single friction plate, which provides fast response in high-cycle applications. Armature engagement is smooth, quiet, and operates with no chatter.
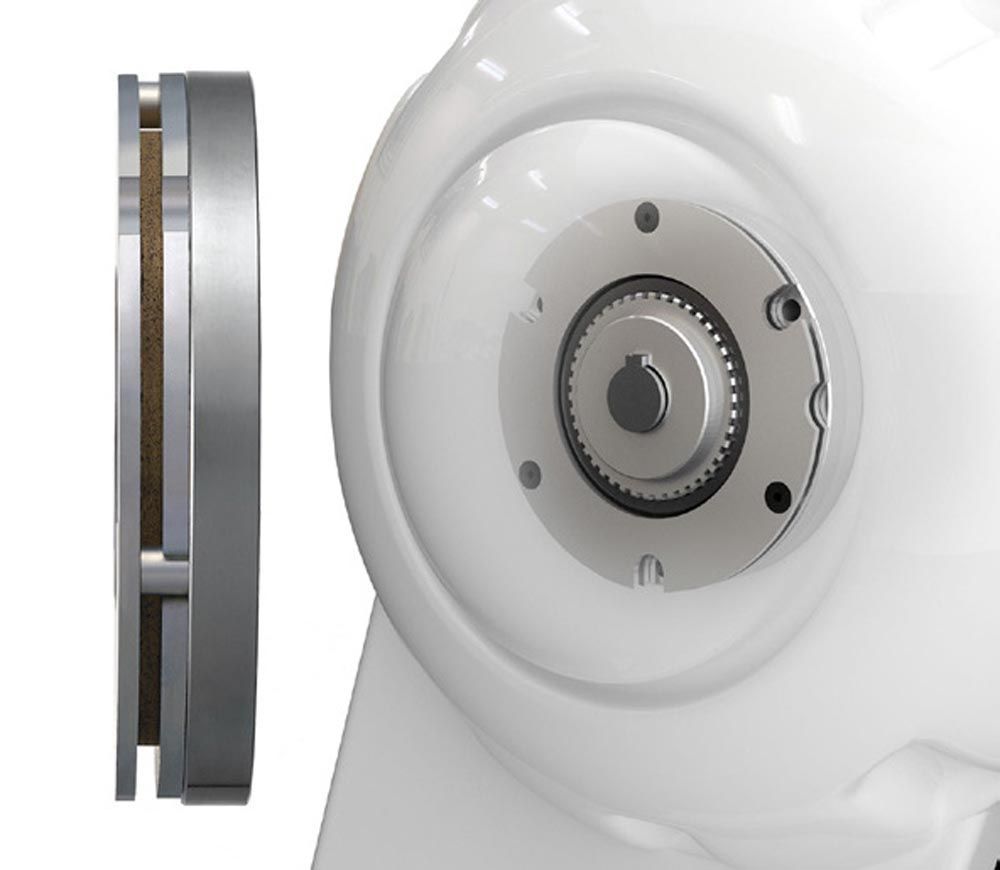
Sleek, extra thin-designed Miki Pulley BXR Brake blends perfectly into this compact articulating robotic arm joint application.
Successful in articulating joint applications where a cantilevered load must be minimized, the extra thin BXR brake operates in this way: to open the brake and allow free rotation, voltage flows to the coil. When power is disengaged from the coil, internal compression springs push the armature plate toward the rotor disc, halting it against the top plate. The square/splined rotor hub affixed to the input shaft interfaces with the rotor disc holding rotational movement.
The Miki Pulley BXR brake is also a space and weight-saving option for servomotor applications. Operating specifications are:
- Brake torque: 3.688 ft. lb. ~ 40.566 ft. lb.: (5N · m ~ 55N · m)
- Brake outer diameter: 3.287 in. ~ 7.280 in.; (83.5mm ~ 185mm)
- Ambient Temperature: 14°F ~ 104°F; (-10°C ~ 40°C)
Miki Pulley also makes available even smaller sizes with the designation BXR-LE, (low energy) for miniature applications 0.06 Nm to 3.20 Nm.
mikipulley-us.com
Ringfeder’s Customizable Solutions for Precise Power Transmission Requirements
The MTL Bidirectional, One-Way Clutch
A clutch that is both bidirectional and one-way might sound like a contradiction. But in fact, Ringfeder offers just such a clutch. As a bidirectional clutch, the MTL can transmit torque from input to output shaft in either rotational direction. And its one-way functionality prevents output shaft loads from backdriving into your other power transmission components. These capabilities make the MTL bidirectional one-way clutch excellent at sustaining torque overloads and shock loading.
Choose from three standard models with torques ranging from 15 to 120 ft. lbs. and bore sizes ranging from seven-eighths to 1⅞ in. The clutch’s driving end achieves smooth rotation regardless of the direction of the load, and it is self-locking—made possible by a friction disc and ball ramp design.
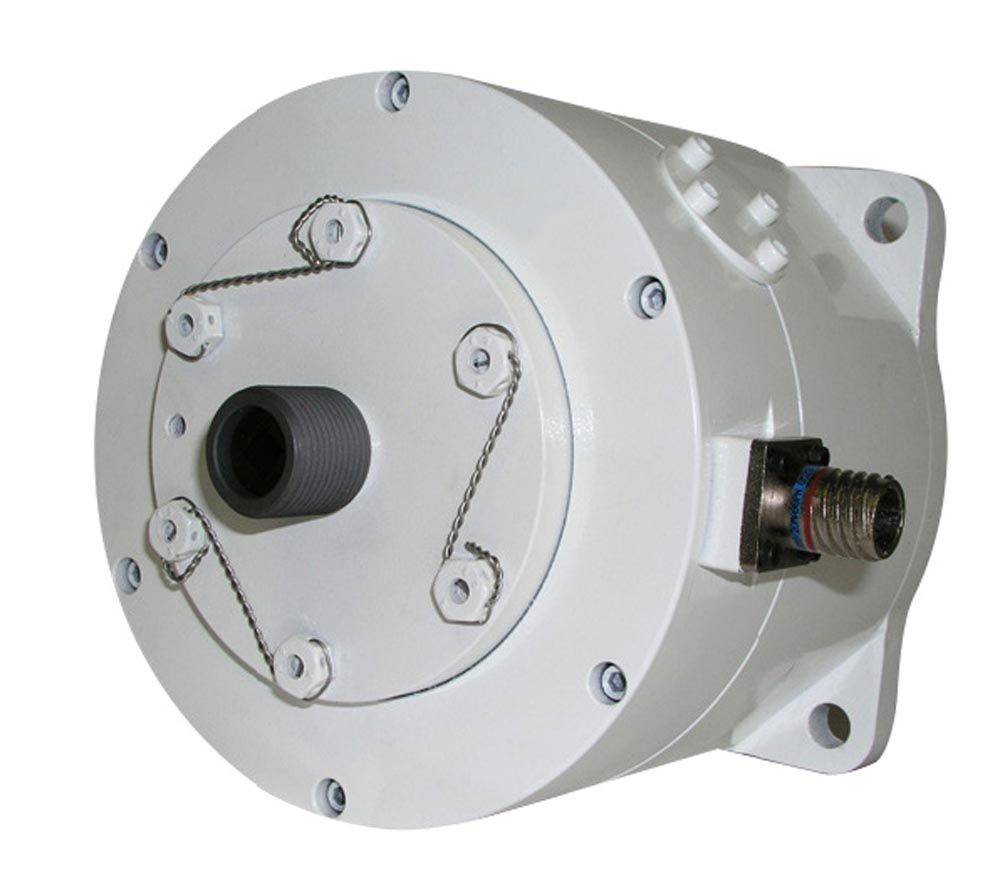
The MTL bidirectional one-way clutch can sustain substantial torque overload and shock loading while preventing the output shaft from backdriving the input shaft in either direction.
You can easily integrate the MTL bidirectional one-way clutch with other Carlyle Johnson clutches, brakes, and torque limiters, creating lighter and more compact designs depending on the component combination. For example, pair the MTL clutch with a Carlyle Johnson spring-applied clutch for braking, torque limiting, and manual driving functionalities—all without having to worry about backdriving.
We can even include a torque limiter as part of the MTL bidirectional one-way clutch. If you place it on the input side, it will limit the driving torque. If you place it on the output side, it will allow slipping in the stationary component if there is an excess load, protecting either upstream or downstream components. Both the internal torque limiter and spring-applied clutch are available customization options. Another option is the ability to set a firm slipping point.
Our experienced engineers can customize the MTL bidirectional one-way clutch to meet your design and application requirements. We can also alter any of our standard products or design an entirely new clutch.
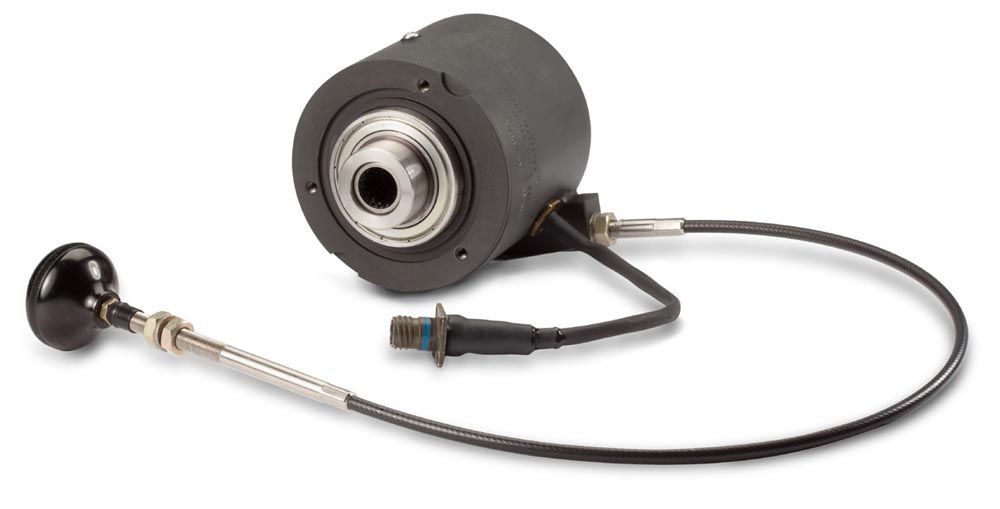
The FEA clutch is ideal for heavy-duty applications and provides a long service life. Its powerful electromagnetic disengagement force ensures a low-drag neutral.
The FEA Fail-Safe Spring Set Electromagnetic Clutch
When developing fail-safe systems for precise, delicate, or heavy-duty machine applications, components that deliver extreme reliability and high performance are invaluable. The FEA Fail-Safe Spring Set Electromagnetic Clutch features a durable design with high-strength components to provide high torque in a compact, easy-to-install, completely assembled package.
Our FEA unit is a spring-applied, positive-acting electric clutch with high repeatability. A powerful electromagnetic force disengages the discs to provide a low-drag neutral, and the radial magnetic flux path provides maximum torque throughout the clutch’s lifespan. To extend the clutch’s lifespan even further, a unique, adjustable end-plate design facilitates easy wear compensation.
The FEA’s coil is sealed within a stationary housing—enabling operation in both wet and dry environments—that is supported by ball bearings. For additional protection, internal compressive forces are contained within the clutch and not transmitted through the bearings. With a focus on dependability, the FEA’s design contains no levers, cams, or other highly stressed parts.
Because there are few moving parts and no slip rings, brushes, or complex wiring that make repair difficult, this clutch can be rebuilt without requiring any special tools. Like all their electromagnetic clutches, the FEA is precision-engineered and undergoes thorough testing to ensure proven, dependable performance across a diverse range of applications.
Custom Solutions
Ringfeder dedicates a significant portion of its production efforts to designing and manufacturing special clutches, brakes, and integrated systems that are custom-tailored to exact user specifications. If you need a custom electromagnetic clutch solution, Ringfeder has the experience and skills to meet your toughest power transmission challenges. Some common modifications include increased torque or adding electronic controls to achieve different actuation and release speeds as well as acceleration and deceleration control.
ringfeder.com