For 87 years following the first Ball Drop in 1907, the Ball was raised and lowered by six men with ropes and a stopwatch—a solution that is far from practical, if even possible, for the current six-ton Ball. “Although it operates on a limited basis, the Ball must always remain functional,” said Brant Underwood, senior project manager at Hudson Scenic Studios.
Whether the Ball is descending on New Year’s Eve or serving as a backdrop for tourist photos the rest of the year, its full weight—including the LED modules, aluminum frame and electrical system at its center—is supported by a powerful winch system. Designed for inverted mounting below the mast platform, this winch includes a two-line system and 42-inch drum with helical grooving. Two 3/4-inch wire ropes, which connect to the Ball, wrap around the drum in opposing directions, maximizing handling control and keeping the winch system as compact as possible.
Also hooked up to the drum is the SEW-Eurodrive gearmotor that holds the weight of the Ball at full torque. The machine incorporates a planetary and helical-bevel gear, AC motor, encoder and brake. A closed loop regenerative variable frequency drive (VFD) uses the encoder to provide highly accurate speed control of the motor. According to Underwood, this regenerative VFD is what turns the winch “into a kind of generator” during the 60-second Ball Drop. “As it resists the load of the Ball during the 75-foot descent, the regenerative system pushes power back to the electrical grid,” Underwood added.
A gearmotor is a combination gear unit and motor, usually an AC or servo motor. Its central function, which is performed by the gear unit and its gear unit stages, is to transmit the motor’s force from the input end to the output end, thereby acting as a kind of converter of speed and torque. In most applications, the gear unit slows down the motor’s rotational speed while at the same time transmitting higher torques than what the electric motor can accomplish on its own.
The SEW-Eurodrive gearmotor incorporates two gears—a planetary gear that produces most of the required torque for the Ball application, as well as a helical-bevel gear. Other components include an AC motor, encoder, and rectifier brake.
- Horsepower: 40 Hz
- RPM: 7.5
- Voltage: 230/460 V
- Shaft: 90 mm
- Flange: 450 mm
- Brake voltage: 230 AC
- Brake torque: 221.2
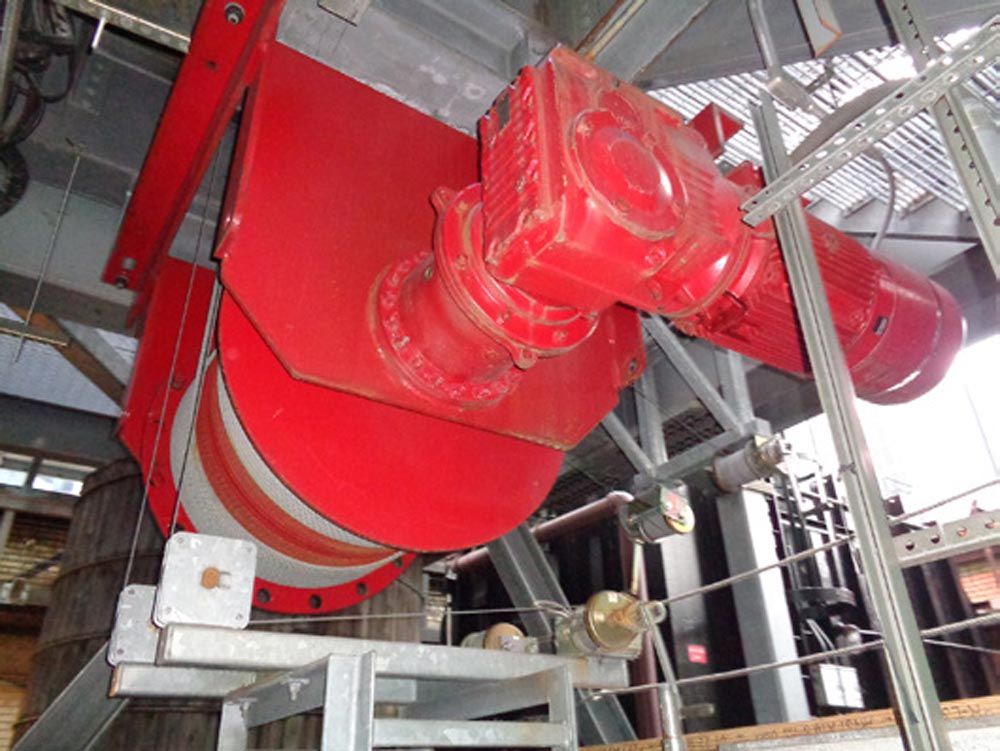
Essential to the winch system the SEW-Eurodrive gearmotor.
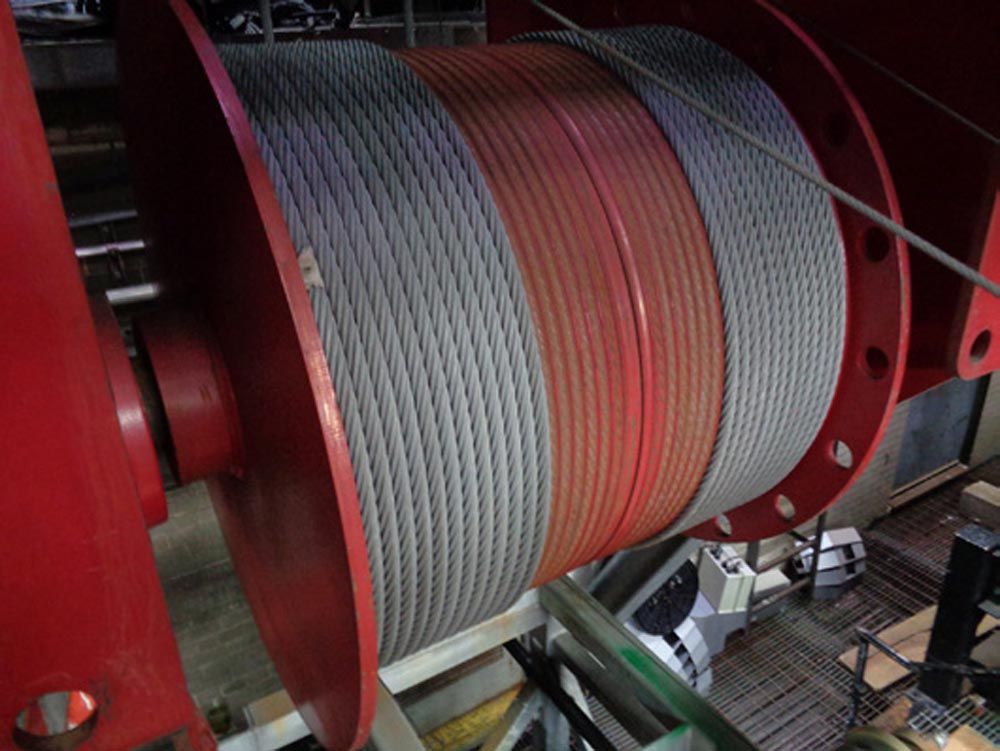
The winch also includes two 3/4-inch wire ropes that wrap around the drum.
Rounding out the winch system is a programmable logic controller (PLC) for controlling all the movements, as well as roughly 20 to 30 multiconductor cables that supply power and data to the whole system. Operators can control the Ball using either a local controller or the human machine interface (HMI) on the 22nd floor of One Times Square.
“The local controller is a secondary interface that acts as a redundancy,” Underwood said. “Using a handheld device, we can go out onto the roof and raise or lower the Ball from there.”
Remote Control Means More Safety
Because the roof of One Times Square contains various signs, railings and other building appendages, the ability to control the Ball remotely creates a critical failsafe. “It can be a tight space up there,” Turnstall says. “Sometimes there’s only a foot of space between the Ball and other building elements. If the Ball descends too low, for example, we need a way to stop it before it hits something and cracks a crystal. Having this ability to control the Ball remotely means there are more eyes on it, ensuring it’s handled and treated with the utmost of care.”
Along this topic of safety, the Ball includes an emergency (E)-stop function, as well as various subsystems and I/O control that enable operators to monitor aspects of the Ball’s position and operation. Examples include the ability to monitor the Ball’s power, as well as sensors that will alert operators if the main disconnect switch turns off.
Improving the Ball’s Reliability Through Routine Servicing
Times Square is one of the most frequently photographed buildings in New York City. “This fact makes routine maintenance critical for the Ball’s ongoing operation, as well as for the forward-facing presentation of the building,” says Ryan Tunstall, senior vice president of development and construction at Jamestown, L.P., which owns One Times Square.
To ensure the winch system will perform its annual duty, the Ball is raised and lowered roughly once a month. SEW-Eurodrive technicians also come in and provide regular inspections of the gearmotor.
The Ball is in good hands. We drain the oil, inspect the internal components of the gearbox, and analyze the oil samples in a lab. The elemental analysis tells us whether there’s any abnormal wear taking place in the equipment. We often apply these same maintenance techniques to other machines.
The gearbox—which was recently serviced by SEW-Eurodrive technicians in early December 2022—has very minimal wear and tear. As the unit ages, the plan is to “be more aggressive” in terms of making technical recommendations.
Fortunately, the gearmotor doesn’t need extensive servicing due to its limited operational frequency. Because of the low duty cycle, the gearbox rarely experiences a significant rise in temperature, which has a direct effect on the health and longevity of the equipment.
To 2023—and Beyond
According to Straus of Countdown Entertainment, the Ball, with a billion eyes on it each year, depends on the gearmotor and winch system to ensure the New Year starts. “One year, when the Ball was still controlled by ropes, a person even got tangled up, causing the Ball to stop halfway through its descent and delaying the New Year,” Straus said with a chuckle. “Thanks to the winch system, we’ve never had an issue.”