Next-generation technology—everything from the electrification of vehicles to e-motors, bearings, mechatronics, and thermal management—was recently discussed during the Schaeffler Symposium 2022 in Detroit.
Daniel Sayre, director of the eMotor and power electronic business, sat down to discuss the evolution of electric motors and power electronics at the event. Topics included new process innovations, green steel initiatives, magnet-free motor technology and advancements in power electronics.

The Versatility of E-Drives
The global increase in electric vehicles provides a unique opportunity in the design and manufacture of components. Due to the variety of design topologies, a company like Schaeffler must provide a wide range of options in a flexible manner. They’re currently building a technology platform which defines and standardizes all relevant production steps for all types and sizes of motors. Large investments in these areas will eventually lead to an annual production capacity of four million electric motors by 2029.
Schaeffler can accomplish this flexibility thanks to the experience and ingenuity brought to the table by the company’s design, testing and industrialization teams.
“For the initial motor concept, for example, we have the design, testing and industrialization team look at all aspects,” Sayre said. “Here’s the technologies we’re confident in, here’s the technologies we’re developing and here’s the technologies that cause problems. This is about looking at everything from simulation to design all the way to the actual performance of the products.”
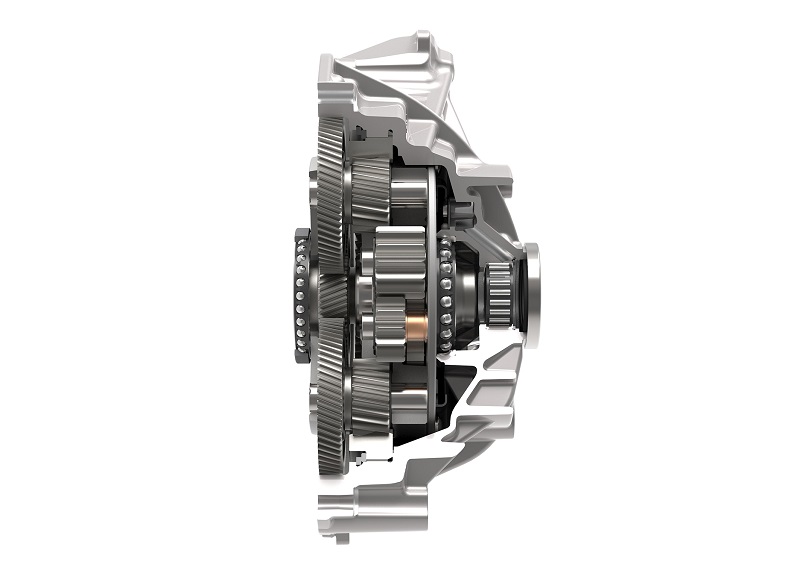
The company has an e-mobility history that dates back 20+ years in all aspects of electric motor industrialization. Mass production of the electric axle transmission, a key component of electric axle systems, has been running successfully since 2017, providing optimum transmission ratios and power transfer from the electric motor to the wheels. This is a highly versatile component with a wide range of applications.
Furthermore, the 4in1 electric axle, integrates the thermal management system as well as the electric motor, power electronics, and transmission into the axle drive. This makes the axle drive more compact and lighter and ensures greater comfort. A particularly efficient thermal management system also ensures that a car travels further on one battery charge and charges faster. Another new development are electric beam axles for pick-up trucks. In the future, Schaeffler will supply beam axles to automobile manufacturers, particularly in North America.
A Focus on Green Energy
Schaeffler has partnered with H2greensteel (H2GS) in Sweden to develop new products. The steel produced in Sweden requires non fossil fuels and reduces Schaeffler’s annual CO2 emissions—a strategically important collaboration as the company moves toward lower CO2 steel production in support of decarbonization.

“The goal is to not only limit the carbon footprint but develop products in collaboration with H2greensteel in order to address any problems or differences in the products as the volume of green steel increases across the globe,” Sayre said.
The production of green steel is energy-intensive and must be done from sustainable sources. Northern Sweden offers excellent conditions for this. The production of steel without carbon dioxide is realized by H2GS by the direct reduction method, in which hydrogen produced from renewable energies is used instead of coking coal, thus enabling a 95-percent reduction in the CO2 emissions produced with previous methods.
“By eliminating waste and providing more efficient components, we’re taking that next step to reach our own sustainability goals,” Sayre added.
Evolving Technology
Sayre said that e-motor technology would be evolving in the coming years in a variety of ways. Magnet-free motors (induction motors with a cast aluminum rotor) and separately excited motors (where Schaeffler has a next-generation design) will provide high-speed performance benefits in the future.
Process innovations such as annealing of stator laminations and advanced continuous hairpin winding make it possible to boost the efficiency of current radial flux machines even further. With the development of a new axial flux motor, Schaeffler is making it possible to realize electric powertrains with very high-volume power densities.
“Packaging is another key criterion depending on where the motor is placed in the vehicle, what it’s attached to—whether it’s a simple gearbox, a multi-speed gearbox, it’s in the wheel, it’s paired between an existing engine and transmission—the packaging really drives what motor technology we need to use for a particular application,” Sayre said.
Power density and torque density are also very important.
“Not just the peak performance, but also the continuous performance. As I talked about during my presentation, for example, a high-performance motor with integrated slot cooling is critical,” he added.
The concept of an externally excited synchronous motor which avoids resistive loses at lower speeds through slot cooling is enabling new advancements in electric drives.
“The roads only allow you to go so fast in EVs from a stop sign or traffic signal,” Sayre said, “but in order to consistently drive down a highway in an electric vehicle we need to simplify the thermal system. We are responsible for making better use of the components and the automotive technology for our customers by essentially doing more with less.”
Schaeffler has invested nearly $200 million over the last five years to support e-mobility growth. The 800,000+ square-foot facility, located in Wooster, Ohio, incorporates production assembly for the hybrid module, a battery and fuel cell technology lab, an e-motor test lab as well as development of power electronics units and e-axles.